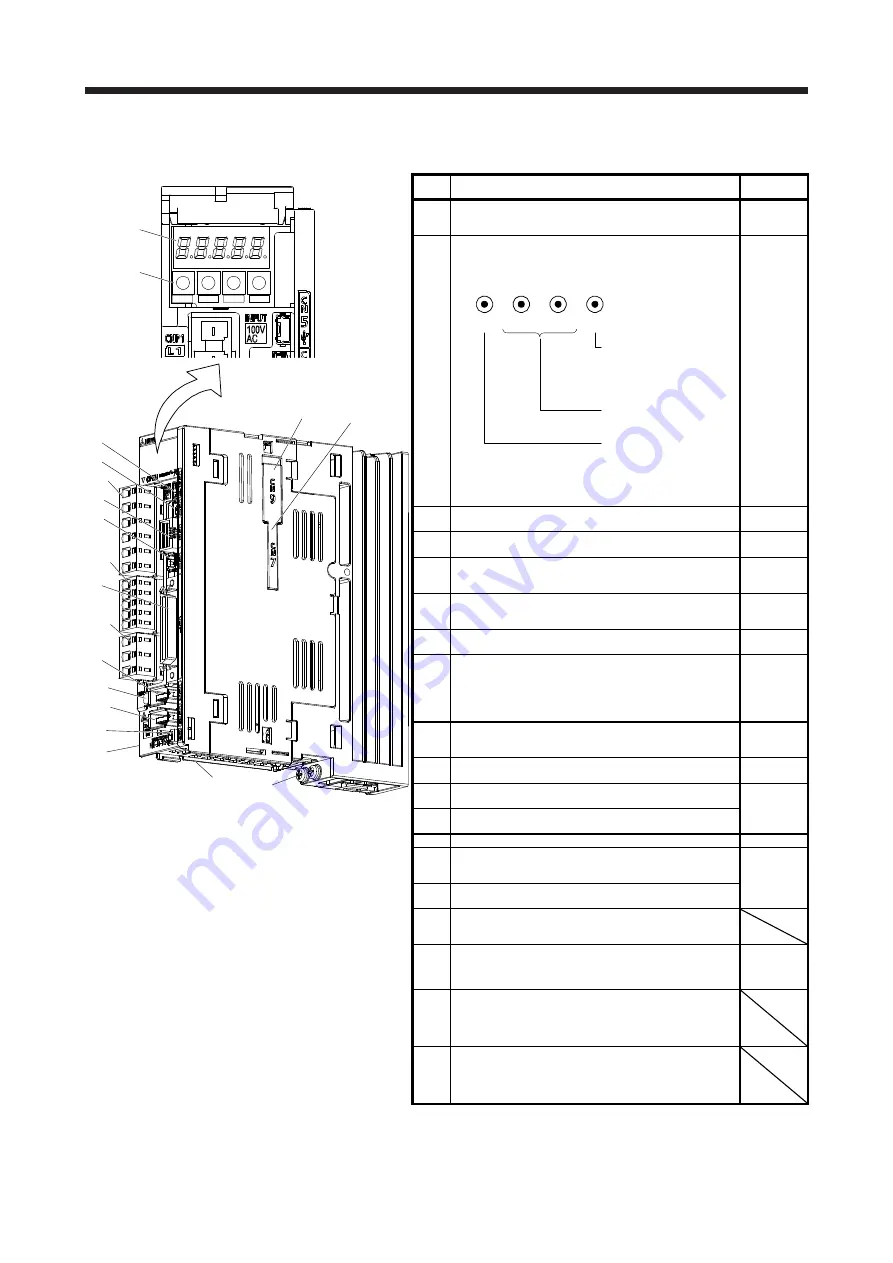
1. FUNCTIONS AND CONFIGURATION
1 - 37
(3) 100 V class
The diagram is for MR-J4-10A1-RJ.
Inside of the display cover
MODE
UP
DOWN
SET
(1)
(2)
(4)
(12)
(14)
(13)
(17)
Side
(9)
(5)
(6)
(7)
(16)
(15)
(8)
(3)
(18)
(10)
(11)
(19)
No. Name/Application Detailed
explanation
(1)
Display
The 5-digit, 7-segment LED shows the servo status and the
alarm number.
Section 4.5
(2)
Operation section
Used to perform status display, diagnostic, alarm, and
parameter setting operations. Push the "MODE" and "SET"
buttons at the same time for 3 s or more to switch to the
one-touch tuning mode.
Used to set data.
Push this button
together with the "MODE"
button for 3 s or more
to switch to the
one-touch tuning mode.
MODE UP DOWN SET
Used to change the
display or data in each
mode.
Used to change the mode.
Push this button
together with the "SET"
button for 3 s or more
to switch to the
one-touch tuning mode.
Section 4.5
(3)
USB communication connector (CN5)
Connect with the personal computer.
Section
11.7
(4)
Analog monitor connector (CN6)
Outputs the analog monitor.
Section 3.2
(5)
RS-422/RS-485 communication connector (CN3)
Connect with the RS-422/RS-485 communication controller,
parameter unit, etc.
Chapter 14
(6)
STO input signal connector (CN8)
Used to connect the MR-J3-D05 safety logic unit and
external safety relay.
Chapter 13
App. 5
(7)
I/O signal connector (CN1)
Used to connect digital I/O signals.
Section 3.2
Section 3.4
(8)
(Note
2)
Encoder connector (CN2)
Used to connect the servo motor encoder or external
encoder. Refer to table 1.1 for the compatible external
encoders.
Section 3.4
"Servo
Motor
Instruction
Manual
(Vol. 3)"
(9)
Battery connector (CN4)
Used to connect the battery for absolute position data
backup.
Chapter 12
(10)
Battery holder
Install the the battery for absolute position data backup.
Section
12.2
(11)
Protective earth (PE) terminal
Grounding terminal
Section 3.1
Section 3.3
(12)
Main circuit power supply connector (CNP1)
Connect the input power supply.
(13)
Rating plate
Section 1.6
(14)
Control circuit power supply connector (CNP2)
Connect the control circuit power supply and regenerative
option.
Section 3.1
Section 3.3
(15)
Servo motor power output connector (CNP3)
Connect the servo motor.
(16)
Charge lamp
When the main circuit is charged, this will light up. While
this lamp is lit, do not reconnect the cables.
(17)
(Note
1, 2)
External encoder connector (CN2L)
Refer to table 1.1 for the compatible external encoders.
"Linear
Encoder
Instruction
Manual"
(18)
Optional unit connector (CN7)
Connect the optional unit. It is available with MR-J4-_A1-RJ
servo amplifiers manufactured in November 2014 or later.
The MR-J4-_A1 servo amplifier does not have this
connector.
(19)
Optional unit connector (CN9)
Connect the optional unit. It is available with MR-J4-_A1-RJ
servo amplifiers manufactured in November 2014 or later.
The MR-J4-_A1 servo amplifier does not have this
connector.
Note 1. This is for the MR-J4-_A1-RJ servo amplifier. The MR-J4-_A1 servo amplifier does not have the CN2L connector.
2. "External encoder" is a term for linear encoder used in the linear servo system and load-side encoder used in the fully closed
loop system in this manual.
Summary of Contents for MR-J4
Page 9: ...A 8 MEMO ...
Page 19: ...10 MEMO ...
Page 73: ...1 FUNCTIONS AND CONFIGURATION 1 54 MEMO ...
Page 155: ...3 SIGNALS AND WIRING 3 76 MEMO ...
Page 199: ...4 STARTUP 4 44 MEMO ...
Page 289: ...6 NORMAL GAIN ADJUSTMENT 6 24 MEMO ...
Page 335: ...8 TROUBLESHOOTING 8 8 MEMO ...
Page 357: ...9 OUTLINE DRAWINGS 9 22 MEMO ...
Page 517: ...12 ABSOLUTE POSITION DETECTION SYSTEM 12 30 MEMO ...
Page 617: ...16 USING A DIRECT DRIVE MOTOR 16 20 MEMO ...
Page 641: ...17 FULLY CLOSED LOOP SYSTEM 17 24 MEMO ...
Page 725: ...18 MR J4 03A6 SERVO AMPLIFIER 18 84 MEMO ...
Page 763: ...APPENDIX App 38 ...
Page 789: ...MEMO ...
Page 793: ......