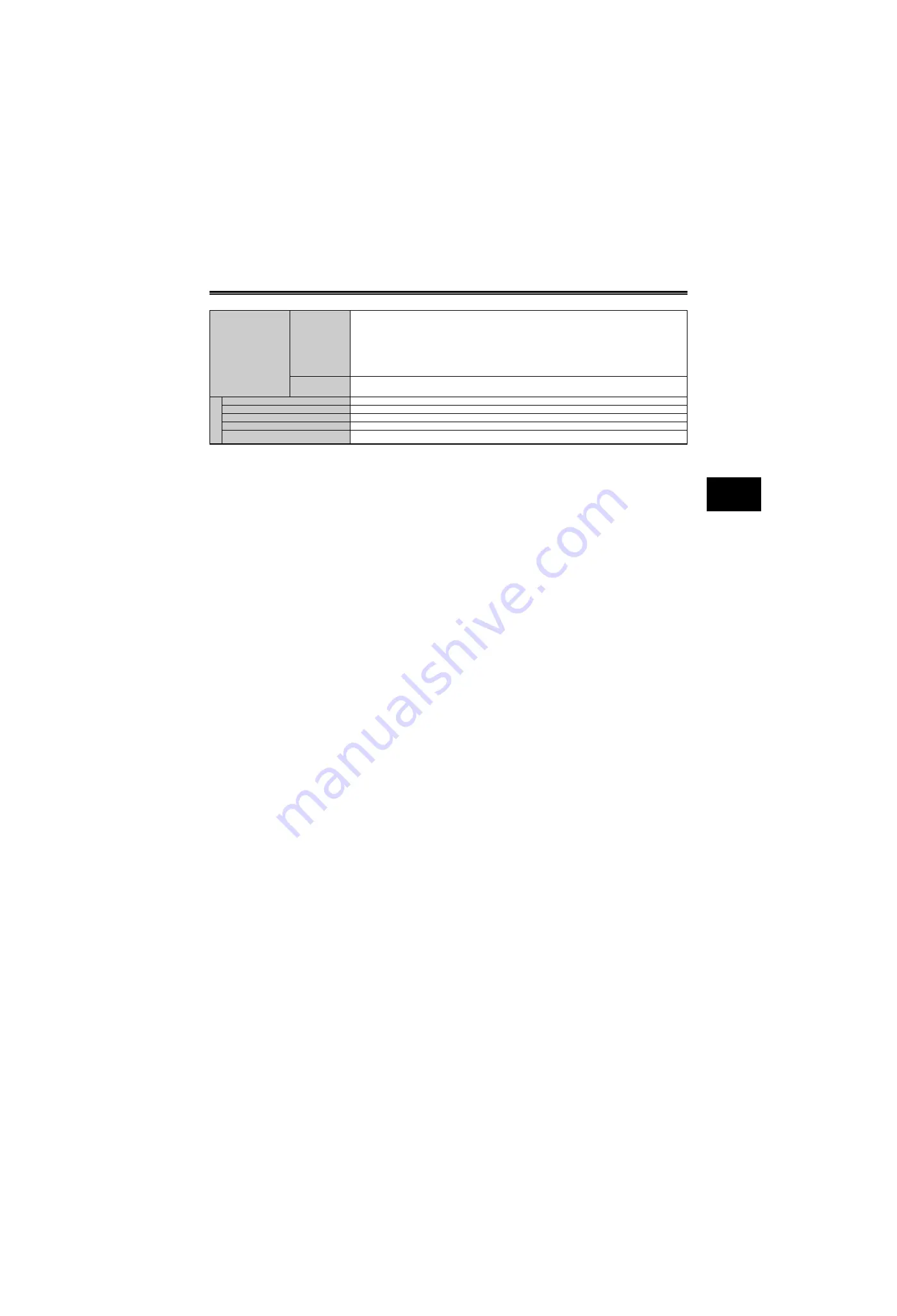
13
1
S
PECIFI
C
A
T
IONS
SPECIFICATIONS
Protective/warning
function
Protective
functions
Overcurrent during acceleration, overcurrent during constant speed, overcurrent during deceleration, overvoltage
during acceleration, overvoltage during constant speed, overvoltage during deceleration, inverter protection
thermal operation, motor protection thermal operation, heatsink overheat, input phase failure, output side earth
(ground) fault overcurrent at start
, output phase failure, external thermal relay operation
, option fault,
parameter error, PU disconnection, retry count excess
, CPU fault, brake transistor alarm, inrush resistance
overheat, communication error, analog input error, USB communication error, brake sequence error 4 to 7
Warning functions
Fan alarm
, overcurrent stall prevention, overvoltage stall prevention, PU stop, parameter write error,
regenerative brake prealarm
, electronic thermal relay function prealarm, maintenance output
, undervoltage
E
n
vi
ro
nm
en
t
Surrounding air temperature
-10°C to +50°C (non-freezing) (-10°C to +40°C for totally-enclosed structure feature)
Ambient humidity
90%RH or less (non-condensing)
Storage temperature
-20°C to +65°C
Atmosphere
Indoors (without corrosive gas, flammable gas, oil mist, dust and dirt etc.)
Altitude/vibration
Maximum 1000m above sea level, 5.9m/s
2
or less at 10 to 55Hz (directions of X, Y, Z axes)
*1
The braking torque indicated is a short-duration average torque (which varies with motor loss) when the motor alone is
decelerated from 60Hz in the shortest time and is not a continuous regenerative torque. When the motor is decelerated from
the frequency higher than the base frequency, the average deceleration torque will reduce. Since the inverter does not contain
a brake resistor, use the optional brake resistor when regenerative energy is large. (Not available for 0.1K and 0.2K.) A brake
unit (FR-BU2) may also be used.
*2
Temperatures applicable for a short time, e.g. in transit.
*3
As the 0.75K or less are not provided with the cooling fan, this alarm does not function.
*4
When using the inverters at the surrounding air temperature of 40°C or less, the inverters can be installed closely attached
(0cm clearance).
*5
This protective function does not function in the initial status.
Summary of Contents for FR-A700 Series
Page 245: ...279 2 PARAMETER PARAMETER MEMO ...
Page 440: ...474 PARAMETER MEMO ...
Page 522: ...556 SELECTION MEMO ...