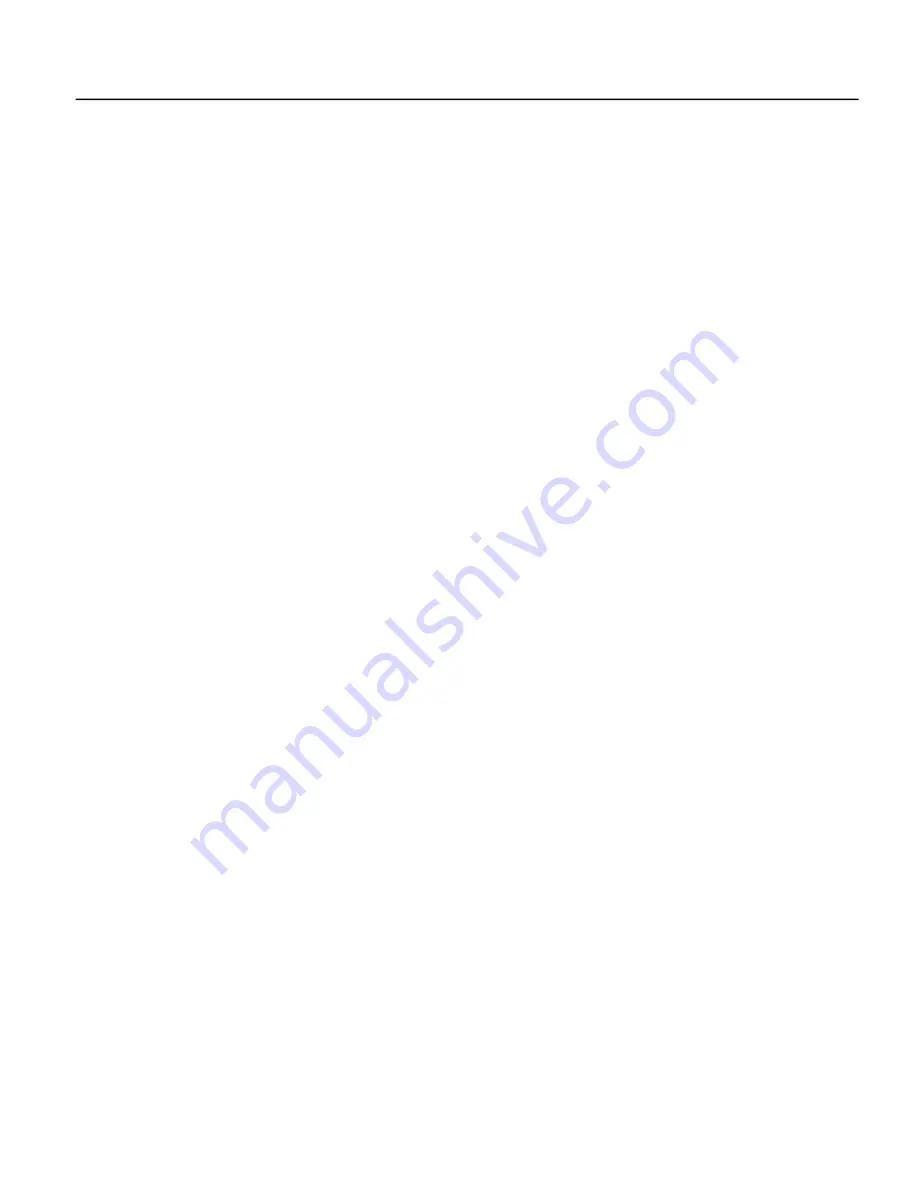
OPERATION
Control Options
69
When the drive is in
AUTO
mode, it runs the motor at a variable frequency based on information from the
automation system through the input selected in
Auto Speed Ref [SET–07]
.
Standard Operation with PID Feedback Control
A PID controlled application, such as a fan system or a constant pressure pump system, uses feedback from
a transducer to measure system performance against a user defined Setpoint (target) to control motor
speed. The VFD can use several types of measurement, including pressure, flow, level, air volume, tempera
-
ture, speed, etc.
For example:
•
In a pumping application, the default measurement unit is
PSI
. As user demand (flow) causes pressure
changes, the drive varies the output frequency (motor speed) to maintain pressure at the target set
-
point. When the drive determines a no-demand condition, it enters Sleep mode and stops the motor.
•
In a fan application, the default measurement unit is
inWC
(air pressure).
When the drive is in
AUTO
mode, it runs the motor at a variable frequency based on a comparison between
the
PID Setpoint [SET–21]
and feedback from the PID transducer, up to the
PID Hi Hz Limit [SET–23]
. PID operation is
disabled in
HAND
mode.
When basic setup is complete, including motor specifications, verify or set the following parameters for PID
operation:
Auto Speed Ref [SET–07]:
Set to
7_PID Output
.
Auto Run Command [SET–08]:
Select source of Run Command, either Keypad or external. If using a Digital
Input (MI1-MI8) with a switch, set the terminal to
38_FWD
(or
39_REV
)
[IO–21 ~ 28]
.
PID Mode [SET–17]:
Set to
1_PID Direct
for most PID operations.
Feedback Source [SET–18]:
Set to the terminal used for transducer connection. Make sure impedance is set
correctly.
PID Feedback Units [SET–19]:
Set to the appropriate measurement unit for the transducer type.
PID Feedback Max [SET–20]:
Set to the maximum rating of the transducer.
PID Setpoint [SET–21]:
Set to the desired measurement target.
PID P-Gain [SET–24]:
Proportional Gain controls motor speed adjustments based on the proportional dif
-
ference between the PID setpoint and PID feedback. Higher settings result in a faster response. However, if
the value is too high, it may cause system oscillation and instability. Used along with
PID I-TIme [SET-25]
to
smooth and balance system response.
PID I Time [SET–25]:
Integral Time determines PID response time. Lower values increase system response
to the feedback signal, which reduces overshoot, but may cause system oscillation if set too low. Greater
values provide slower response, which may cause overshoot of the setpoint and oscillation of output fre
-
quency.
Sleep Mode [SET–26]:
This should be enabled for most pump applications, and
0_Disabled
for most HVAC
applications.
Summary of Contents for CERUS X-DRIVE CXD-003A-4V
Page 2: ......
Page 3: ...CERUS X DRIVE INSTALLATION AND OPERATION MANUAL Firmware Version 1 2 Franklin Electric Co Inc ...
Page 96: ...OPERATION Protection Features 96 ...
Page 112: ...ADVANCED APPLICATION OPTIONS Multi Drive Configurations 112 ...
Page 124: ...COMMUNICATIONS BACnet Communication 124 ...
Page 128: ...ACCESSORIES Optional Extension Cards 128 Frame D Frame E Frame F ...
Page 129: ...ACCESSORIES Optional Extension Cards 129 Frame G Frame H ...
Page 132: ...ACCESSORIES Optional Extension Cards 132 ...
Page 234: ...PARAMETER REFERENCE TABLES Parameter Descriptions Motor Menu 234 ...
Page 250: ...GLOSSARY 250 ...