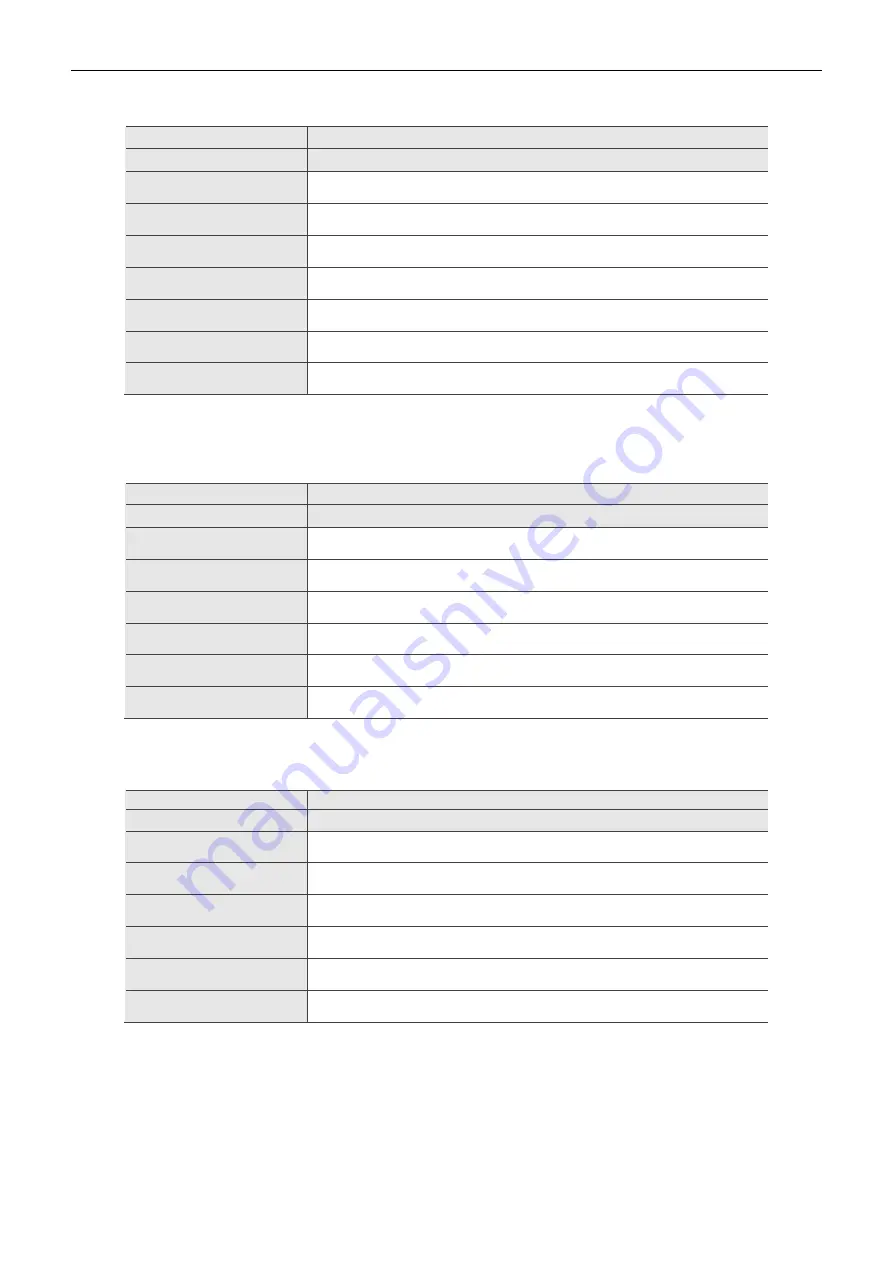
ASDA-B2-F Appendix B Accessories
September, 2015
B-15
B
1 kW Servo Drive with 1 kW Low-inertia Motor
Servo Drive
ASD-B2-1021-F
Low-inertia Motor
ECMA-C
△
0910
S
Motor Power Cable
(without brake)
ASDBCAPW020X
Power Connector
(without brake)
ASDBCAPW0000
Motor Power Cable
(with brake)
ASDBCAPW030X
Power Connector
(with brake)
ASDBCAPW0100
Incremental Encoder Cable
ASDBCAEN000X
Absolute Encoder Cable ASD-B2EB000X
Encoder Connector ASDBCAEN0000
(X = 3 indicates that the cable length is 3 m; X = 5 indicates that the cable length is 5 m)
1 kW Servo Drive with 1 kW Medium-inertia Motor
Servo Drive
ASD-B2-1021-F
Medium-inertia Motor
ECMA-E
△
1310
S
Motor Power Cable
(without brake)
ASDBCAPW120X
Motor Power Cable
(with brake)
ASDBCAPW130X
Power Connector
ASD-CAPW1000
Incremental Encoder Cable
ASDBCAEN100X
Absolute Encoder Cable ASD-B2EB100X
Encoder Connector ASDBCAEN1000
(X = 3 indicates that the cable length is 3 m; X = 5 indicates that the cable length is 5 m)
1 kW Servo Drive with 900 W High-inertia Motor
Servo Drive
ASD-B2-1021-F
High-inertia Motor
ECMA-G
△
1309
S
Motor Power Cable
(without brake)
ASDBCAPW120X
Motor Power Cable
(with brake)
ASDBCAPW130X
Power Connector
ASD-CAPW1000
Incremental Encoder Cable
ASDBCAEN100X
Absolute Encoder Cable ASD-B2EB100X
Encoder Connector ASDBCAEN1000
(X = 3 indicates that the cable length is 3 m; X = 5 indicates that the cable length is 5 m)
Summary of Contents for ASD-B2-0121-F
Page 3: ...September 2015 This page is intentionally left blank...
Page 9: ...VI September 2015 This page is intentionally left blank...
Page 29: ...Installation ASDA B2 F 2 12 September 2015 2 This page is intentionally left blank...
Page 185: ...Parameters ASDA B2 F 7 68 September 2015 7 This page is intentionally left blank...
Page 199: ...Communications ASDA B2 F 8 14 September 2015 8...
Page 201: ...Communications ASDA B2 F 8 16 September 2015 8 This page is intentionally left blank...
Page 217: ...Troubleshooting ASDA B2 F 9 16 September 2015 9 This page is intentionally left blank...
Page 239: ...Absolute System ASDA B2 F 10 22 September 2015 10 This page is intentionally left blank...