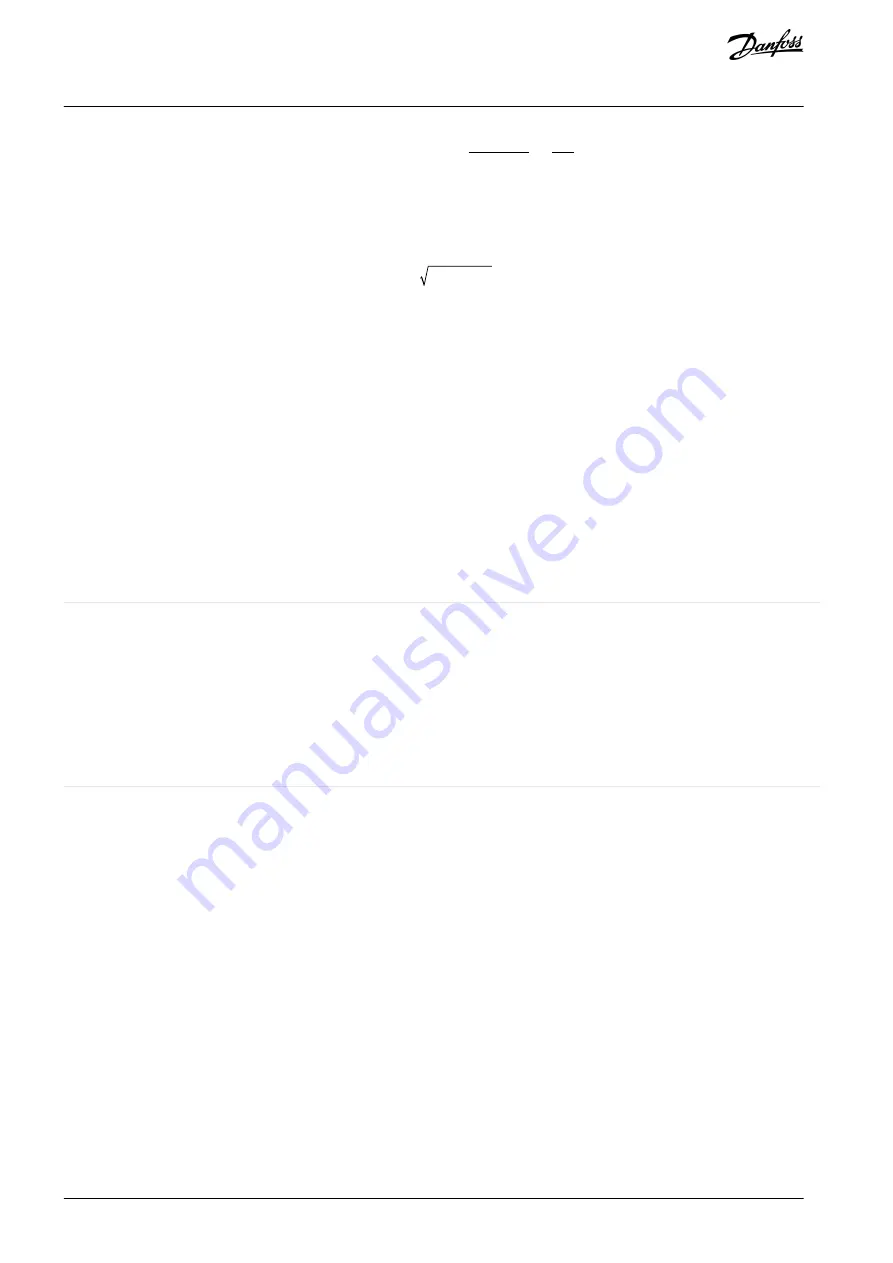
Power factor =
I
1
× cos
ϕ
1
I
RMS
=
I
1
I
RMS
since cos
ϕ
1 = 1
The power factor indicates to which extent the drive imposes a load on the
mains supply.
The lower the power factor, the higher the I
RMS
for the same kW perform-
ance.
I
RMS
=
I
1
2
+
I
5
2
+
I
7
2
+ .. +
I
n
2
In addition, a high-power factor indicates that the different harmonic cur-
rents are low.
The DC coils in the drive produce a high-power factor, which minimizes the
imposed load on the mains supply.
Preset reference
A defined preset reference to be set from -100% to +100% of the reference
range. Selection of 8 preset references via the digital terminals.
Process PID
The PID control maintains the required speed, pressure, temperature, and
so on, by adjusting the output frequency to match the varying load.
Pulse input/incremental encoder
An external, digital pulse transmitter used for feeding back information on
motor speed. The encoder is used in applications where great accuracy in
speed control is required.
Pulse reference
A pulse frequency signal transmitted to the digital inputs (terminal 29 or
33).
R
RCD
Residual-current device.
Ref
MAX
Determines the relationship between the reference input at 100-% full scale
value (typically 10 V, 20 mA) and the resulting reference. The maximum ref-
erence value is set in
parameter 3-03 Maximum Reference
.
Ref
MIN
Determines the relationship between the reference input at 0-% value (typi-
cally 0 V, 0 mA, 4 mA) and the resulting reference. The minimum reference
value is set in
parameter 3-02 Minimum Reference
.
S
SFAVM
Switching pattern called stator flux-oriented asynchronous vector modula-
tion (
parameter 14-00 Switching Pattern
).
SLC
The SLC (smart logic control) is a sequence of user-defined actions execu-
ted when the associated user-defined events are evaluated as true by the
SLC. (See
parameter group 13-** Smart Logic Control
).
STW
Status word.
Safe Torque Off (STO)
The STO function brings the drive safely to a no-torque state.
Setup
Save parameter settings in 4 setups. Change between the 4 parameter set-
ups and edit 1 setup, while another setup is active.
Slip compensation
The drive compensates for the motor slip by giving the frequency a supple-
ment that follows the measured motor load keeping the motor speed al-
most constant.
Start-disable command
A start command belonging to Group 2 control commands, see the
table
Function Groups
under
Control Command
.
Stop command
A stop command belonging to Group 1 control commands, see the
table
Function Groups
under
Control Command
.
AU275636650261en-000101/130R0334
720 | Danfoss A/S © 2022.12
Glossary
VLT AutomationDrive FC 301/302
Programming Guide
Summary of Contents for VLT AutomationDrive FC 301
Page 2: ......