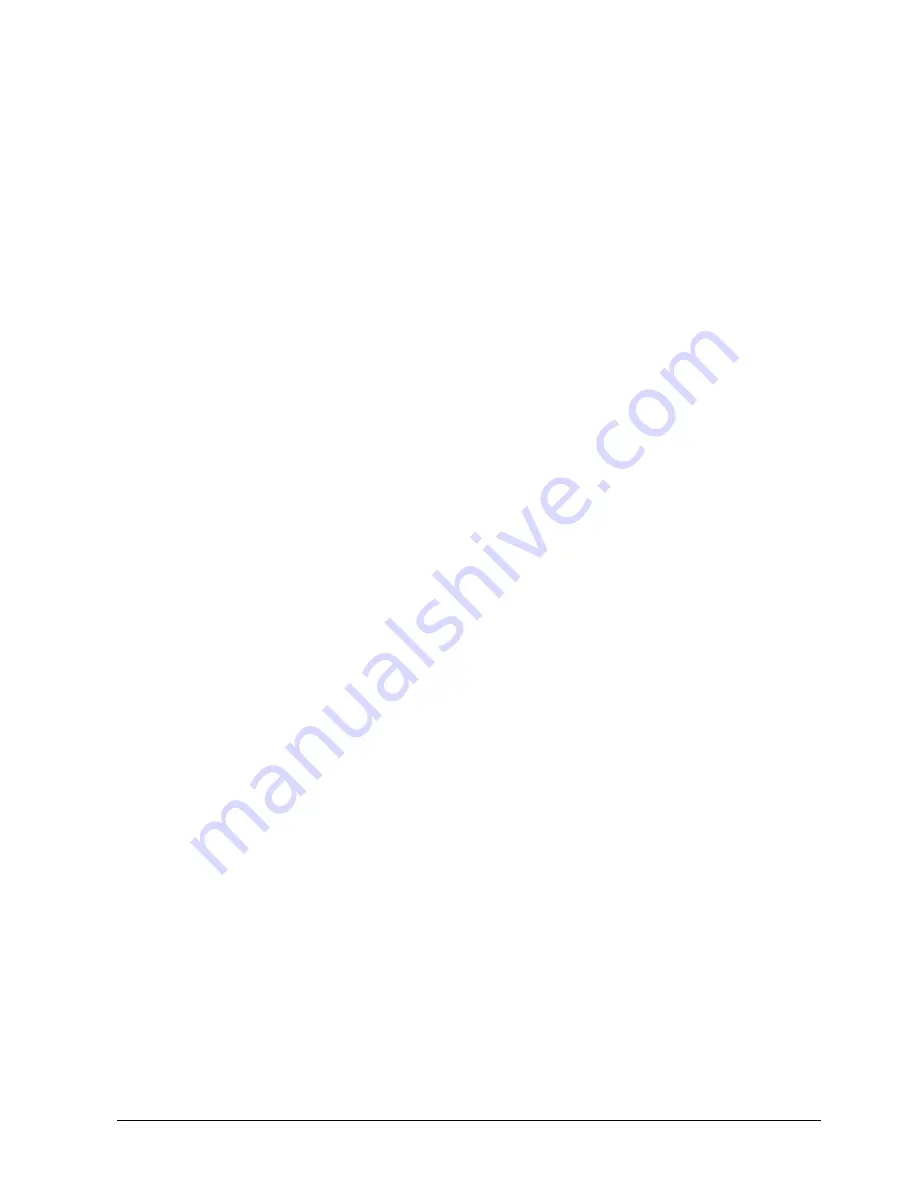
101/226
Building Technologies
Boiler Sequence Controller RMK770
CE1P3132en
HVAC Products
7 Boiler temperature control
01.03.2005
With the basic configuration, a boiler temperature sensor is automatically configured for
each of the boilers 1 and 2. The boiler temperature sensor is required if the burner shall
maintain a boiler temperature setpoint and / or if minimum or maximum limitation of the
boiler temperature shall be ensured.
With the plant types that include maintained boiler return temperature with a mixing
valve, a return temperature sensor will automatically be preconfigured. In these cases,
the sensor is a mandatory requirement. In all other cases, a return temperature sensor
can be configured for display purposes.
Using the release input, a boiler can be locked from an external location. The operating
action of the input can be parameterized at the respective terminal on
Main menu >
Set-
tings > Inputs
.
Additional supervision of the burner is made possible with the checkback signal burner.
If the checkback signal is not received after an adjustable period of time, the burner will
initiate lockout. With the burner checkback signal, the burner hours run counter is
started only after the checkback signal has been received. When there is no checkback
signal, the burner hours run counter is started with the output signal for stage 1. In this
way, the prepurge time, etc., is also acquired.
Also refer to section 7.13 “Boiler faults”.
With the help of the checkback signal shutoff valve, the correct functioning of the shut-
off valve can be monitored. Also, the burner is started only after the “Open“ position of
the shutoff valve has been confirmed by the checkback signal.
If there is no checkback signal, the burner will initiate lockout also.
Also refer to section 7.13 “Boiler faults”.
Using the flue gas temperature sensor, the flue gas temperature can be displayed and
monitored.
Also refer to section 7.11 “Flue gas temperature supervision”.
With the flue gas measuring mode contact, function “Flue gas measuring mode” can be
activated at the respective boiler.
Also refer to section 7.11 “Flue gas temperature supervision”.
Using the checkback signal from a modulating burner (0…1000
Ω
, DC 0…10 V), the
current burner output can be acquired. It can be used for display purposes and for
producing the output balance.
This terminal can be used for the burner fault status message.
Also refer to section 7.13 “Boiler faults”.
For additional fault supervisions, there are 3 universal fault inputs available.
Also refer to section 7.13 “Boiler faults”.
Fault input for supervision of the boiler pump
Fault input for supervision of boiler pump B in the case of twin pumps.
Input for flow supervision of the boiler pump.
Control input, used to operate boiler 1 in individual operation.
Also refer to section 7.6 “Individual operation”.
Boiler sensor
Return sensor
Release input
Checkback signal
burner
Checkback signal
shutoff valve
Flue gas temperature
sensor
Flue gas measuring
mode contact
Current burner output
Fault burner
Fault input 1…3
Boiler pump overload
Boiler pump B overload
Flow signal
Individual operation