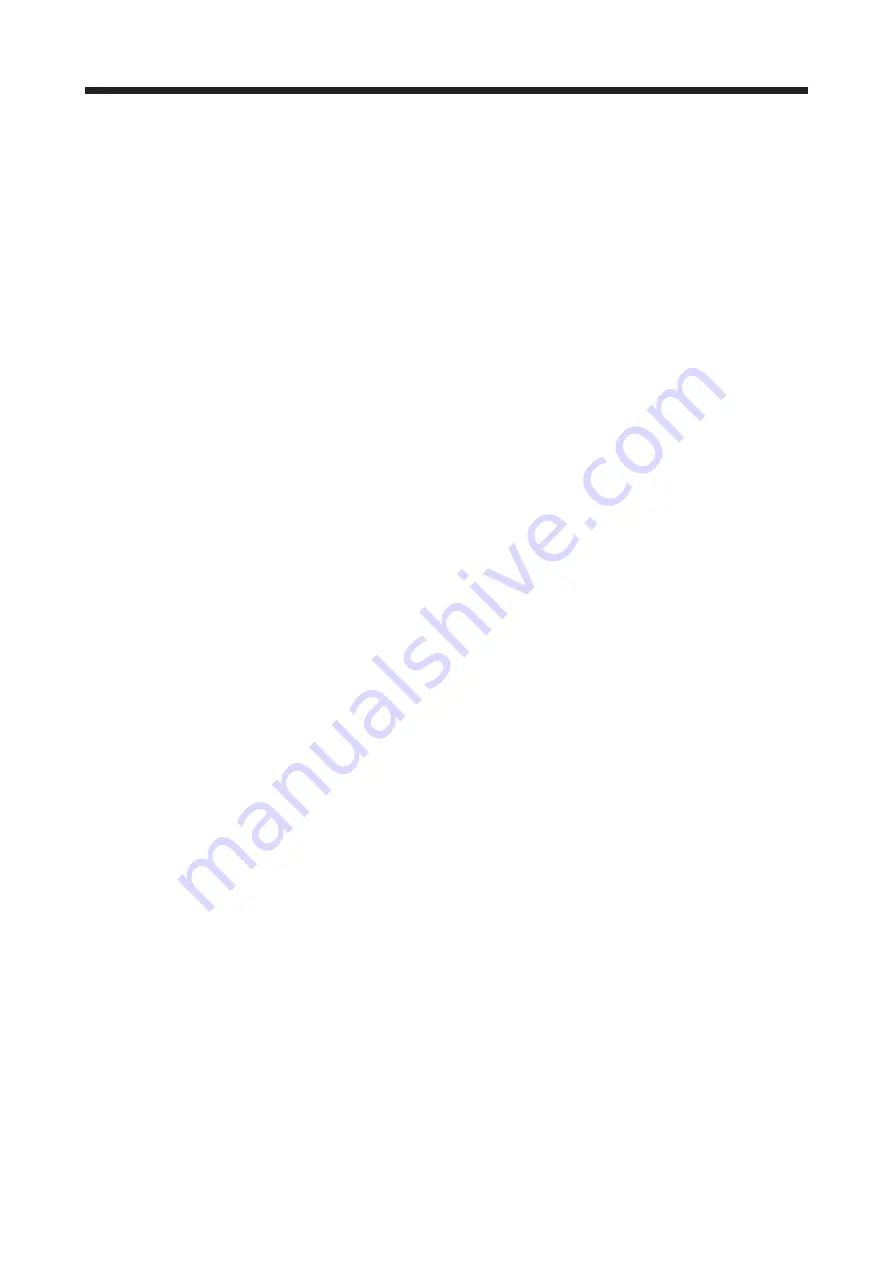
1. FUNCTIONS AND CONFIGURATION
1 - 13
Note 1. 0.5 A is the value applicable when all I/O signals are used. The current capacity can be decreased by reducing the number of
I/O points.
2. When closely mounting the servo amplifiers, operate them at the ambient temperature of 0
˚
C to 45
˚
C or at 75% or smaller
effective load ratio.
3. Test pulse is a signal which instantaneously turns off a signal to the servo amplifier at a constant period for external circuit to
self-diagnose.
4. Except for the terminal block.
5. The rated current is 2.9 A when the servo amplifier is used with a UL or CSA compliant servo motor.
6. 1 Mpulse/s or lower commands are supported in the initial setting. When inputting commands over 1 Mpulse/s and 4
Mpulses/s or lower, change the setting in [Pr. PA13].
7. RS-422 communication is supported by servo amplifier with software version A3.
8. Use an external dynamic brake for this servo amplifier. Failure to do so will cause an accident because the servo motor does
not stop immediately but coasts at emergency stop. Ensure the safety in the entire equipment.
9. For the compatible version for the fully closed loop system, refer to table 1.1. Check the software version of the servo amplifier
with MR Configurator2.
10. The MR-J4-_A servo amplifier is compatible only with the two-wire type.
The MR-J4-_A-RJ servo amplifier is compatible with the two-wire type, four-wire type, and A/B/Z-phase differential output
method. Refer to table 1.1 for details.
11. This value is applicable when a 3-phase power supply is used.
12. The external dynamic brake cannot be used for compliance with SEMI-F47 standard. Do not assign DB (Dynamic brake
interlock) in [Pr. PD23] to [Pr. PD26], [Pr. PD28], and [Pr. PD47]. Failure to do so will cause the servo amplifier to become
servo-off when an instantaneous power failure occurs.
13. RS-485 communication is available with servo amplifiers manufactured in November 2014 or later.
14. When using 1-phase 200 V AC to 240 V AC power supply, operate the servo amplifier at 75% or smaller effective load ratio.
15. The safety level depends on the setting value of [Pr. PF18 STO diagnosis error detection time] and whether STO input
diagnosis by TOFB output is performed or not. For details, refer to the Function column of [Pr. PF18] in section 5.2.6.
16. Follow the restrictions in section 2.6 when using this product at altitude exceeding 1000 m and up to 2000 m above sea level.
17. The DC power supply input is available only with MR-J4-_A-RJ servo amplifiers. For the connection example of the power
circuit when a DC input is used, refer to app. 13.
Содержание MR-J4-100A(-RJ)
Страница 19: ...10 MEMO ...
Страница 75: ...1 FUNCTIONS AND CONFIGURATION 1 56 MEMO ...
Страница 83: ...2 INSTALLATION 2 8 MEMO ...
Страница 159: ...3 SIGNALS AND WIRING 3 76 MEMO ...
Страница 203: ...4 STARTUP 4 44 MEMO ...
Страница 351: ...7 SPECIAL ADJUSTMENT FUNCTIONS 7 40 MEMO ...
Страница 365: ...8 TROUBLESHOOTING 8 14 MEMO ...
Страница 387: ...9 DIMENSIONS 9 22 MEMO ...
Страница 403: ...10 CHARACTERISTICS 10 16 MEMO ...
Страница 553: ...12 ABSOLUTE POSITION DETECTION SYSTEM 12 30 MEMO ...
Страница 567: ...13 USING STO FUNCTION 13 14 MEMO ...
Страница 607: ...14 COMMUNICATION FUNCTION MITSUBISHI ELECTRIC GENERAL PURPOSE AC SERVO PROTOCOL 14 40 MEMO ...
Страница 639: ...15 USING A LINEAR SERVO MOTOR 15 32 MEMO ...
Страница 767: ...18 MR J4 03A6 RJ SERVO AMPLIFIER 18 84 MEMO ...
Страница 856: ...APPENDIX App 41 ...
Страница 905: ...MEMO ...