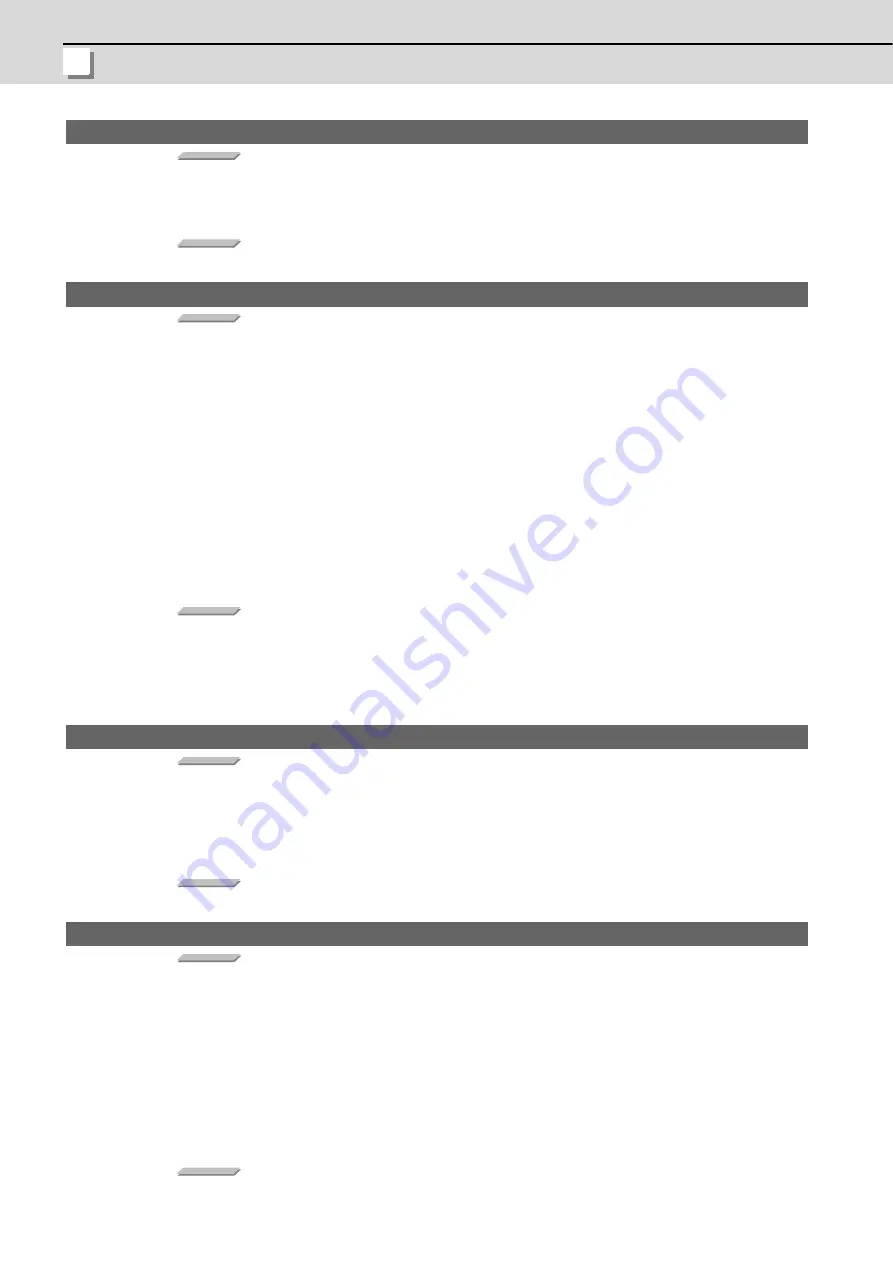
Appendix 6 Explanation of Alarms
MITSUBISHI CNC
IV - 136
P484 R-pnt ret incomplete (mill)
Details
- Movement was commanded to an axis that had not completed reference position return during the
milling mode.
- Movement was commanded to an axis that had not completed reference position return during
cylindrical interpolation or polar coordinate interpolation.
Remedy
- Carry out manual reference position return.
P485 Illegal modal (mill)
Details
- The milling mode was turned ON during nose R compensation or constant surface speed control.
- A T command was issued during the milling mode.
- The mode was switched from milling to cutting during tool compensation.
- Cylindrical interpolation or polar coordinate interpolation was commanded during the constant
surface speed control mode (G96).
- The command unacceptable in the cylindrical interpolation was issued.
- A T command was issued during the cylindrical interpolation or polar coordinate interpolation mode.
- A movement command was issued when the plane was not selected just before or after the G07.1
command.
- A plane selection command was issued during the polar coordinate interpolation mode.
- Cylindrical interpolation or polar coordinate interpolation was commanded during tool radius
compensation.
- The G16 plane in which the radius value of a cylinder is "0" was specified.
- A cylindrical interpolation or polar coordinate interpolation command was issued during coordinate
rotation by program.
Remedy
- Correct the program.
- Issue G40 or G97 before issuing G12.1.
- Issue a T command before issuing G12.1.
- Issue G40 before issuing G13.1.
- Specify the radius value of a cylinder other than "0", or specify the X axis's current value other than
"0" before issuing G12.1/G16.
P486 Milling error
Details
- The milling command was issued during the mirror image (when parameter or external input is
turned ON).
- Polar coordinate interpolation, cylindrical interpolation or milling interpolation was commanded
during mirror image for facing tool posts.
- The start command of the cylindrical interpolation or polar coordinate interpolation was issued during
the normal line control.
Remedy
- Correct the program.
P501 Cross (G110) impossible
Details
Mixed control (cross axis control) command (G110) was issued in the following modes.
- During nose R compensation mode
- During pole coordinate interpolation mode
- During cylindrical interpolation mode
- During balance cut mode
- During fixed cycle machining mode
- During facing turret mirror image
- During constant surface speed control mode
- During hobbing mode
- During axis name switch
Remedy
- Correct the program.
Содержание E70 Series
Страница 1: ......
Страница 3: ......
Страница 9: ......
Страница 11: ......
Страница 13: ......
Страница 15: ......
Страница 24: ...I SCREEN OPERATIONS ...
Страница 25: ......
Страница 26: ...I 1 1 Operating the Setting and Display Unit ...
Страница 57: ...1 Operating the Setting and Display Unit MITSUBISHI CNC I 32 ...
Страница 58: ...I 33 2 Monitor Screens ...
Страница 139: ...2 Monitor Screens MITSUBISHI CNC I 114 ...
Страница 140: ...I 115 3 Setup Screens ...
Страница 232: ...I 207 4 Edit Screens ...
Страница 286: ...E70 Series Instruction Manual 4 4 Program Input Output I 261 During file transmission During file setting 1 2 4 3 5 6 7 ...
Страница 314: ...I 289 5 Diagnosis Screens ...
Страница 355: ...5 Diagnosis Screens MITSUBISHI CNC I 330 ...
Страница 356: ...I 331 6 Maintenance Screens ...
Страница 436: ...II MACHINE OPERATIONS ...
Страница 437: ......
Страница 439: ...MITSUBISHI CNC II 2 ...
Страница 440: ...II 3 1 Operation State ...
Страница 444: ...II 7 2 Indicator Lamps ...
Страница 446: ...II 9 3 Reset Switch and Emergency Stop Button ...
Страница 448: ...II 11 4 Operation Mode ...
Страница 456: ...II 19 5 Operation Panel Switches in Operation Mode ...
Страница 460: ...II 23 6 Operation Panel Switch Functions ...
Страница 495: ...6 Operation Panel Switch Functions MITSUBISHI CNC II 58 ...
Страница 496: ...II 59 7 Other Functions ...
Страница 509: ...7 Other Functions MITSUBISHI CNC II 72 ...
Страница 510: ...III MAINTENANCE ...
Страница 511: ......
Страница 512: ...III 1 1 Daily Maintenance and Periodic Inspection and Maintenance ...
Страница 515: ...1 Daily Maintenance and Periodic Inspection and Maintenance MITSUBISHI CNC III 4 ...
Страница 516: ...III 5 2 Hardware Replacement Methods ...
Страница 531: ...2 Hardware Replacement Methods MITSUBISHI CNC III 20 ...
Страница 532: ...IV APPENDIXES ...
Страница 533: ......
Страница 534: ...IV 1 Appendix 1 List of Function Codes ...
Страница 536: ...IV 3 Appendix 2 Table of Command Value Ranges ...
Страница 543: ...Appendix 2 Table of Command Value Ranges MITSUBISHI CNC IV 10 ...
Страница 544: ...IV 11 Appendix 3 Circular Cutting Radius Error ...
Страница 546: ...IV 13 Appendix 4 Registering Editing the Fixed Cycle Program ...
Страница 561: ...Appendix 4 Registering Editing the Fixed Cycle Program MITSUBISHI CNC IV 28 ...
Страница 562: ...IV 29 Appendix 5 RS 232C I O Device Parameter Setting Examples ...
Страница 564: ...IV 31 Appendix 6 Explanation of Alarms ...
Страница 678: ...IV 145 Appendix 7 Operation Messages ...
Страница 699: ...Appendix 7 Operation Messages MITSUBISHI CNC IV 166 ...
Страница 700: ...IV 167 Appendix 8 User Parameters ...
Страница 777: ...Appendix 8 User Parameters MITSUBISHI CNC IV 244 ...
Страница 782: ......