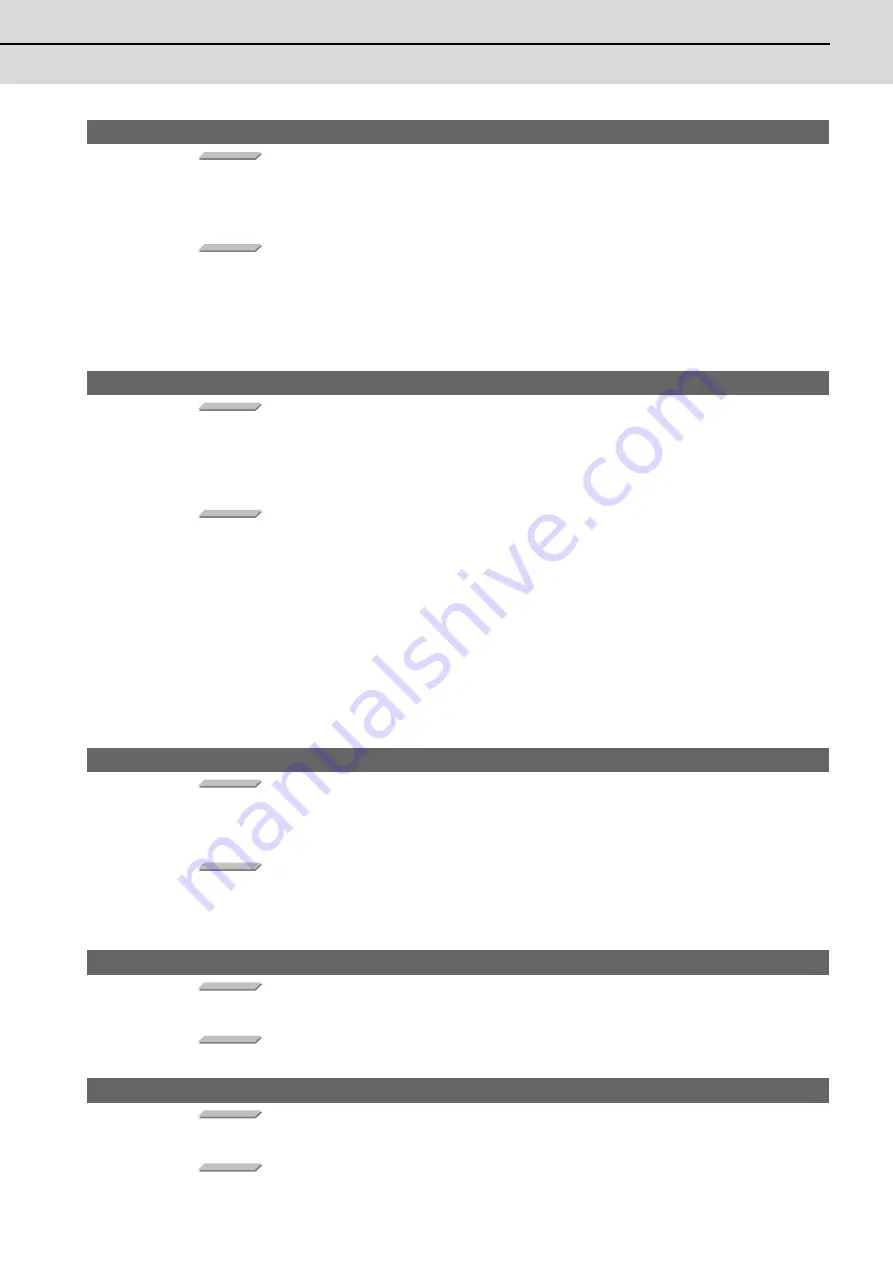
E70 Series Instruction Manual
Appendix 6.4 MCP Alarms (Y)
IV - 85
Y08 Too many drive units connected 00xy
Details
The number of drive units connected to each channel exceeds 8.
The exceeded number of drive units per channel is displayed as alarm No.
x: Exceeded number of drive units at drive unit interface channel 2 (0 to F)
y: Exceeded number of drive units at drive unit interface channel 1 (0 to F)
Remedy
Remove drive units from the channel whose alarm No. is other than "0" for the number displayed as
the alarm No. Keep the number of connected drive units to 8 or less.
(Note 1) The drive unit is not counted when all the axes connected to it are invalid.
(Note 2) If this alarm occurs, the alarm "Y03 Message: Drive unit unequipped" will not occur.
(Note 3) The alarm "Y07 Too many axes connected" and "Y09 Too many axisno connected" are
displayed taking precedence over this alarm.
Y09 Too many axisno connected 00xy
Details
The No. of the axis (drive unit's rotary switch No.) connected to each channel is bigger than the No.
allowed.
If the axis No. of each channel is bigger than the No. allowed, "1" is displayed for the alarm No.
x: "1" when the axis No. at drive unit interface channel 2 is too big
y: "1" when the axis No. at drive unit interface channel 1 is too big
Remedy
For the channel whose alarm No. is "1", keep the axis No. (drive unit's rotary switch No.) not bigger
than the No. allowed.
(Note 1) The axis No. is limited per each drive unit interface channel.
(Note 2) The biggest allowed connected axis No. differs depending on whether or not an expansion
unit is available or the setting of "#11012 16 axes for 1ch (Connecting 16 axes for 1ch)". The
biggest connectable axis No. is as shown below.
With the expansion unit, axes No. '0' to '7' can be connected.
Without the expansion unit, axes No. '0' to '7' are allowed when '#11012 16 axes for 1ch
(Connecting 16 axes for 1ch)' is set to '0', axes No. '0' to 'F' when set to '1'.
(Note 3) If this alarm occurs, the alarm "Y03 Message: Drive unit unequipped" will not occur.
(Note 4) This alarm is displayed taking precedence over the alarm "Y08 Too many drive units
connected".
(Note 5) The alarm "Y07 Too many axes connected" is displayed taking precedence over this alarm.
Y11 Node Detect Err 8002-8300 xy00
Details
Drive unit does not respond to the request from NC when the NC is turned ON.
Error No. shows the No. of communication phase at which the response stopped.
x: Channel No. (0 or later)
y: Station No. with the error (0 or later)
Remedy
The communication error may be caused by the drive unit software version that does not correspond to
the NC software version. Check the drive unit software version.
This alarm is canceled after the NC restarts.
When the alarm is not canceled, write down the alarm No. and contact service center.
Y12 No commu. with axis drv unit
Details
Although the high-speed synchronous tapping option is valid, the connected drive unit doesn't support
the option.
Remedy
Replace the drive unit with that supports the option.
Y13 No commu. with sp drv unit
Details
Although the high-speed synchronous tapping option is valid, the connected drive unit doesn't support
the option.
Remedy
Replace the drive unit with that supports the option.
Содержание E70 Series
Страница 1: ......
Страница 3: ......
Страница 9: ......
Страница 11: ......
Страница 13: ......
Страница 15: ......
Страница 24: ...I SCREEN OPERATIONS ...
Страница 25: ......
Страница 26: ...I 1 1 Operating the Setting and Display Unit ...
Страница 57: ...1 Operating the Setting and Display Unit MITSUBISHI CNC I 32 ...
Страница 58: ...I 33 2 Monitor Screens ...
Страница 139: ...2 Monitor Screens MITSUBISHI CNC I 114 ...
Страница 140: ...I 115 3 Setup Screens ...
Страница 232: ...I 207 4 Edit Screens ...
Страница 286: ...E70 Series Instruction Manual 4 4 Program Input Output I 261 During file transmission During file setting 1 2 4 3 5 6 7 ...
Страница 314: ...I 289 5 Diagnosis Screens ...
Страница 355: ...5 Diagnosis Screens MITSUBISHI CNC I 330 ...
Страница 356: ...I 331 6 Maintenance Screens ...
Страница 436: ...II MACHINE OPERATIONS ...
Страница 437: ......
Страница 439: ...MITSUBISHI CNC II 2 ...
Страница 440: ...II 3 1 Operation State ...
Страница 444: ...II 7 2 Indicator Lamps ...
Страница 446: ...II 9 3 Reset Switch and Emergency Stop Button ...
Страница 448: ...II 11 4 Operation Mode ...
Страница 456: ...II 19 5 Operation Panel Switches in Operation Mode ...
Страница 460: ...II 23 6 Operation Panel Switch Functions ...
Страница 495: ...6 Operation Panel Switch Functions MITSUBISHI CNC II 58 ...
Страница 496: ...II 59 7 Other Functions ...
Страница 509: ...7 Other Functions MITSUBISHI CNC II 72 ...
Страница 510: ...III MAINTENANCE ...
Страница 511: ......
Страница 512: ...III 1 1 Daily Maintenance and Periodic Inspection and Maintenance ...
Страница 515: ...1 Daily Maintenance and Periodic Inspection and Maintenance MITSUBISHI CNC III 4 ...
Страница 516: ...III 5 2 Hardware Replacement Methods ...
Страница 531: ...2 Hardware Replacement Methods MITSUBISHI CNC III 20 ...
Страница 532: ...IV APPENDIXES ...
Страница 533: ......
Страница 534: ...IV 1 Appendix 1 List of Function Codes ...
Страница 536: ...IV 3 Appendix 2 Table of Command Value Ranges ...
Страница 543: ...Appendix 2 Table of Command Value Ranges MITSUBISHI CNC IV 10 ...
Страница 544: ...IV 11 Appendix 3 Circular Cutting Radius Error ...
Страница 546: ...IV 13 Appendix 4 Registering Editing the Fixed Cycle Program ...
Страница 561: ...Appendix 4 Registering Editing the Fixed Cycle Program MITSUBISHI CNC IV 28 ...
Страница 562: ...IV 29 Appendix 5 RS 232C I O Device Parameter Setting Examples ...
Страница 564: ...IV 31 Appendix 6 Explanation of Alarms ...
Страница 678: ...IV 145 Appendix 7 Operation Messages ...
Страница 699: ...Appendix 7 Operation Messages MITSUBISHI CNC IV 166 ...
Страница 700: ...IV 167 Appendix 8 User Parameters ...
Страница 777: ...Appendix 8 User Parameters MITSUBISHI CNC IV 244 ...
Страница 782: ......