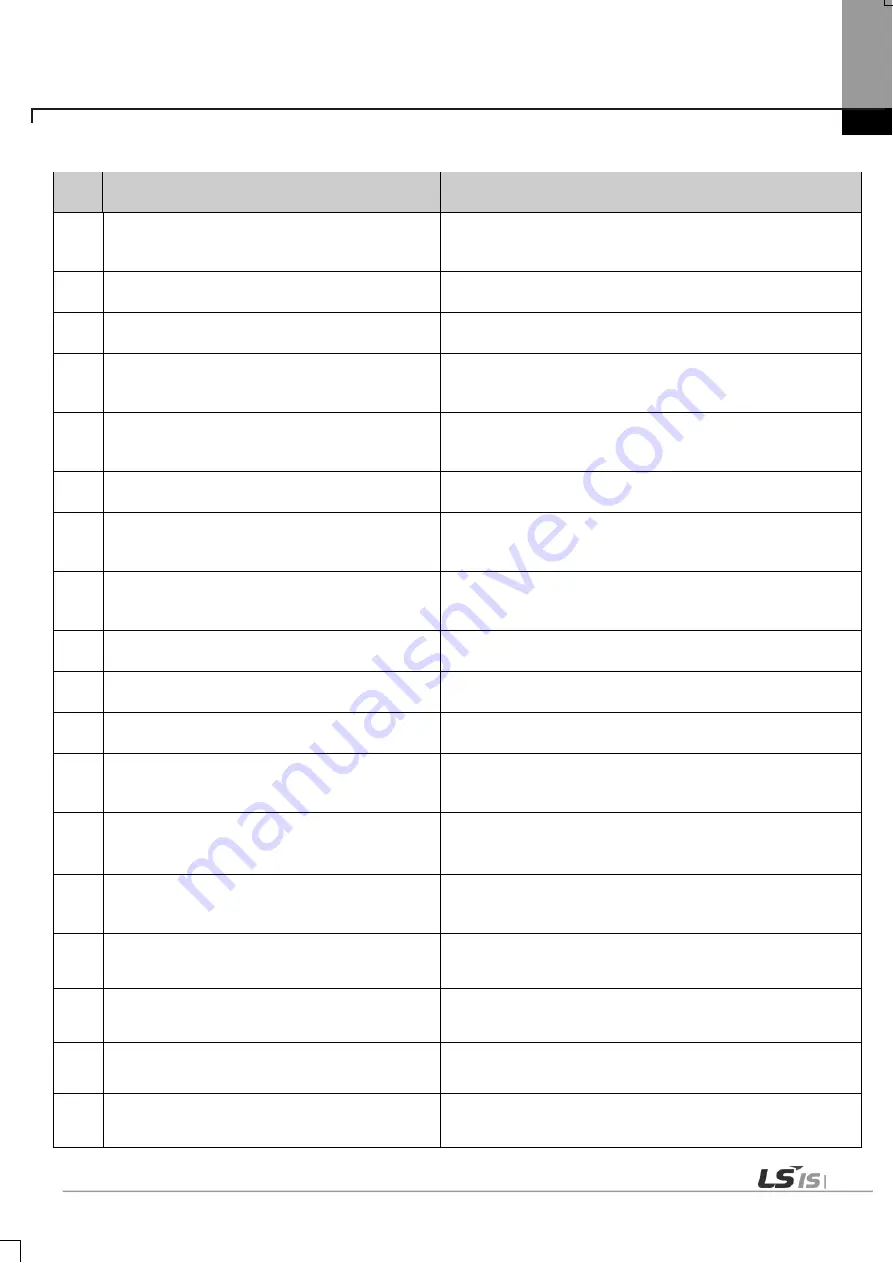
Po
sit
io
n
in
g
Chapter 9 Positioning Error Information & Solutions
9-
15
Error
Code
Error Description
Solutions
554
Radius setting error from Ellipse interpolation.
The range of possible execution for Ellipse Interpolation is between
0 and 2147483647. Set radius of circle from its range, smaller than
2147483647pulse.
555
Exact circle cannot be draw because of degree
of Ellipse interpolation is bigger than 90
°
Set lower for operation speed so that degree
of Ellipse interpolation is smaller than 90
°
556
Continuous operation cannot be done for
Ellipse interpolation.
Execute Ellipse interpolation after terminate
operation step of circular interpolation.
557
Ellipse interpolation only can be operated
when control setting is circular interpolation.
Execute Ellipse interpolation after change
control setting for drive step of Ellipse
interpolation to circular interpolation.
558
Operation cannot be executed when beginning
point and end point of ellipse interpolation are
not same.
Execute Ellipse interpolation after set the goal
Position of ellipse interpolation operating step
Same as current position.
559
Operation cannot be executed when operating
degree of ellipse interpolation is “0.”
Set the value of operating degree for ellipse
interpolation, larger than “0.”(1~65535)
571
Operation cannot be executed because of error from
sub-coordinate axis of main axis by current axis.
Check the error from subordinate axis of main
axis by current axis whether it is occurred
during the operation of current axis.
572
Operation cannot be executed because of error
from sub coordinate axis of main axis by
interpolated axis.
Check the error from subordinate axis of main
axis by current axis whether it is occurred
during the operation of interpolated axis.
701
Not possible to carry out CAM command in the
state of in operation.
Execute CAM command when main axis is not
operating.
702
Not possible to carry out CAM command in the
state of M Code ON
Execute CAM command after set M Code OFF
from commanding axis with XMOF.
703
Not possible to carry out CAM command in the
state that Drive Ready is OFF.
Execute CAM command when Drive Ready is
“ON.”
704
Error of setting main/subordinate axis from
CAM command.
Set main axis for CAM command as other axis
besides its command axis from connecting axis.
Set parameters are 1axis through 4axis.
705
CAM command of main axis cannot be
executed during the operation.
Execute CAM command when the main axis
setting of CAM command is not operating.
706
Error of CAM block setting from CAM
command.
Execute CAM command after set a CAM block
from CAM command as bigger than 1 and
smaller than 8.
707
Error for CAM data of appointed block from
CAM command.
Execute CAM command after set right data for
appointed block from CAM command.
708
The speed of subordinate axis from CAM
command cannot exceed its speed limit.
Set lower speed for main axis so that speed of subordinate axis
from CAM data which is calculated by subordinate position would
not exceed its speed limit.
709
For CAM command, in case main axis is encoder,
main axis unit if CAM data should be pulse.
When you set the main axis of CAM data as encoder, set the unit of
main axis of CAM block as pulse.
710
The speed of the master axis of cam command is so
high that moving position per control period exceeds
the master axis scope.
After slow down the speed of the master axis then operate the axis.
Содержание XBE-DC08A
Страница 124: ...Main Chapter 1 Configuration and Operation Mode of Programs 1 27 1 Memory block diagram ...
Страница 155: ...Main Chapter 2 CPU Function 2 29 Notice For more details on the monitor refer to the XG5000 manual ...
Страница 504: ...Position Chap 6 Commands 6 61 6 11 Function blocks related to Servo Drive ...
Страница 512: ...Positioning Chapter 7 Program 7 8 manual operation 7 1 4 Parameter and Operation Data Setting 1 Parameter Setting ...
Страница 644: ...Positioning Chapter 8 Functions 8 91 ...
Страница 727: ...Positioning Chapter 9 Positioning Error Information Solutions 9 13 ...
Страница 861: ...Special Chapter 1 Embedded Analog 1 39 5 Select View Variables Comments Variables and comments are both displayed ...
Страница 1206: ...Appendix 2 Dimension App2 1 Appendix 2 Dimension Unit mm 1 CPU Type XEC DN32U 2 Positioning Type XEC DN32UP ...
Страница 1207: ...Appendix 2 Dimension App2 2 2 Analog Type XEC DN32UA ...
Страница 1209: ...Appendix 2 Dimension App2 4 XBE DC08A XBE DC16A XBE TN08A XBE TN16A XBE DR16A XBE RY08A ...
Страница 1210: ...Appendix 2 Dimension App2 5 4 Extension Cnet I F Module XBL C41A XBL C21A ...