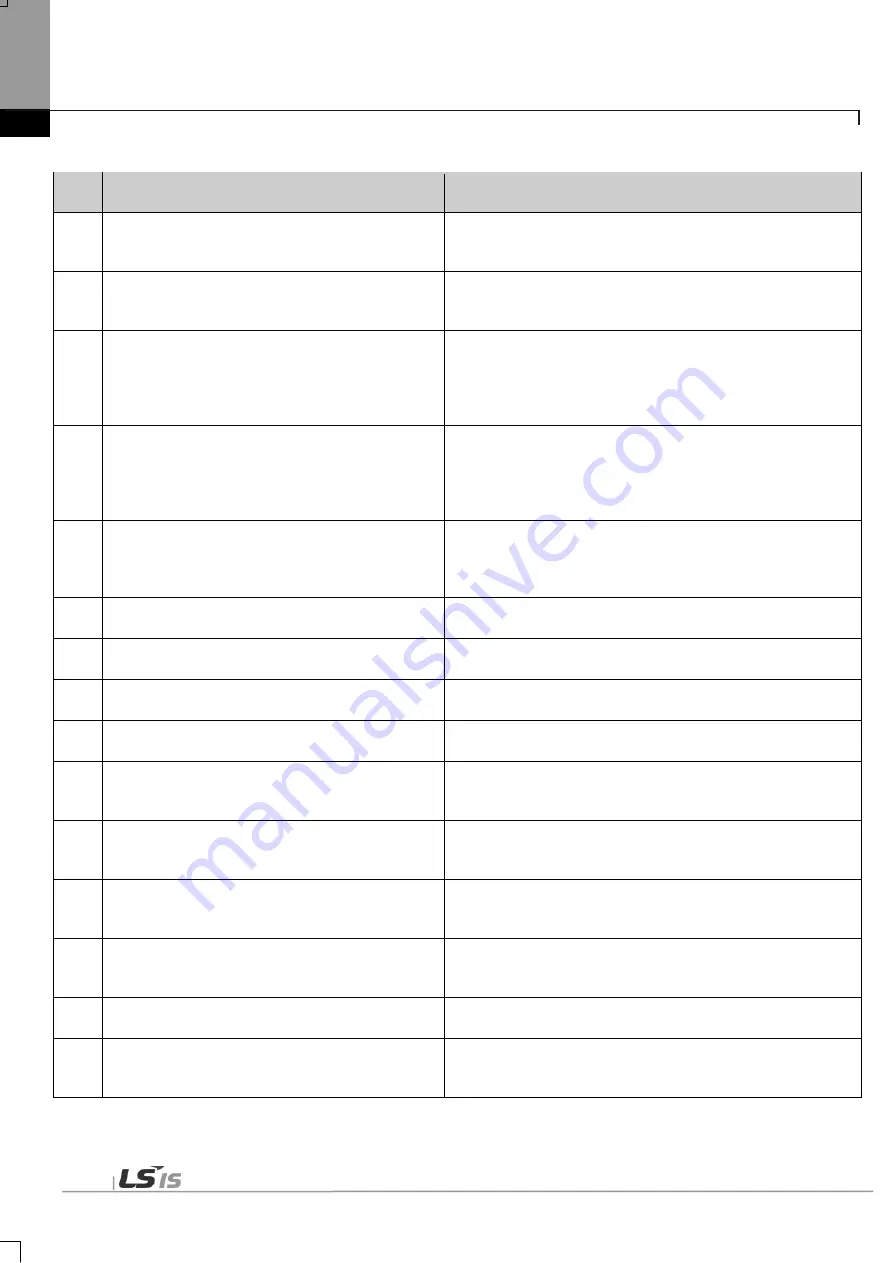
Po
sit
io
n
in
g
Chapter 9 Positioning Error Information & Solutions
9-6
Error
Code
Error Description
Solutions
275
Not possible to carry circular interpolation start in the
state that M Code signal of main axis of circular
interpolation is ON.
Check if M Code signal of main axis is ON when circular
interpolation command is executed. Available to make M Code
OFF by XMOF command.
276
Not possible to carry circular interpolation start in the
state that M Code signal of subordinate axis of circular
interpolation is ON.
Check if M Code signal of subordinate axis is ON when circular
interpolation command is executed. Available to make M Code
OFF by XMOF command.
277
Not possible to carry positioning operation of absolute
coordinate in the state that main axis of circular
interpolation is origin unsettled.
Not available to carry out absolute coordinate operation in the origin
unsettled state. Check the coordinate of step to operate and the
current origin determination state. Available to carry out absolute
coordinate operation after origin determination by Homing
command or floating origin setting command.
278
Not possible to carry positioning operation of absolute
coordinate in the state that subordinate axis of circular
interpolation is origin unsettled
Not available to carry out absolute coordinate operation in the origin
unsettled state. Check the coordinate of step to operate and the
current origin determination state. Available to carry out absolute
coordinate operation after origin determination by Homing
command or floating origin setting command.
279
Incorrect setting of main axis from circular
Interpolation. (Either, unset main axis,
incorrect helical interpolation axis, exceeding
number of current possible operating axis)
Execute circular interpolation after 1.Set one
more operational axis from circular interpolation
data except main axis 2. Set one more operate
able axis from helical interpolation.
280
Not possible to carry out the operation as Drive Ready
is OFF in main axis of circular interpolation.
Check if Driver Ready signal of main axis is OFF when circular
interpolation command is executed.
281
Not possible to carry out the operation as Drive Ready
is OFF in subordinate axis of circular interpolation.
Check if Driver Ready signal of subordinate axis 1 is OFF when
circular interpolation command is executed.
282
Not possible to carry out degree operation in circular
interpolation.
Check if the unit of Basic Parameter of main axis of circular
interpolation command is set as degree.
283
Not possible to carry out degree operation in circular
interpolation.
Check if the unit of Basic Parameter of subordinate axis of circular
interpolation command is set as degree.
284
Not possible to carry out the operation if start point
=center point (middle point) or center point (middle
point) =end point in circular interpolation.
Check if the center point or middle point is set as the same point as
start point or end point in circular interpolation.
285
The start point and end point is Not possible to be
same in the middle point mode of circular interpolation.
Check if circular interpolation method of
Common parameter is set as middle point and
if the position of start point is not the same as end point..
286
Radius setting error in circular interpolation.
The radius of the circle to carry out circular interpolation operation is
up to 2,147,483,647pulse. Check if it is set in order to carry out the
circular interpolation more than the size
287
Not possible to carry out the operation as linear profile
comes out of circular
interpolation.
Check if circular interpolation method of Common parameter is set
as Middle point and the middle point is set to be aligned with start
point and end point.
290
Since angular velocity is greater than 90°,
correct circle cannot be drawn.
Set operation speed lower than 90° for circular
Interpolation angular velocity.
291
Not possible to carry out Synchronous Start command
in the state of in operation.
Check if the Error occurred axis is included in Synchronous Start
command and if there is no axis in operation when the command is
executed.
Содержание XBE-DC08A
Страница 124: ...Main Chapter 1 Configuration and Operation Mode of Programs 1 27 1 Memory block diagram ...
Страница 155: ...Main Chapter 2 CPU Function 2 29 Notice For more details on the monitor refer to the XG5000 manual ...
Страница 504: ...Position Chap 6 Commands 6 61 6 11 Function blocks related to Servo Drive ...
Страница 512: ...Positioning Chapter 7 Program 7 8 manual operation 7 1 4 Parameter and Operation Data Setting 1 Parameter Setting ...
Страница 644: ...Positioning Chapter 8 Functions 8 91 ...
Страница 727: ...Positioning Chapter 9 Positioning Error Information Solutions 9 13 ...
Страница 861: ...Special Chapter 1 Embedded Analog 1 39 5 Select View Variables Comments Variables and comments are both displayed ...
Страница 1206: ...Appendix 2 Dimension App2 1 Appendix 2 Dimension Unit mm 1 CPU Type XEC DN32U 2 Positioning Type XEC DN32UP ...
Страница 1207: ...Appendix 2 Dimension App2 2 2 Analog Type XEC DN32UA ...
Страница 1209: ...Appendix 2 Dimension App2 4 XBE DC08A XBE DC16A XBE TN08A XBE TN16A XBE DR16A XBE RY08A ...
Страница 1210: ...Appendix 2 Dimension App2 5 4 Extension Cnet I F Module XBL C41A XBL C21A ...