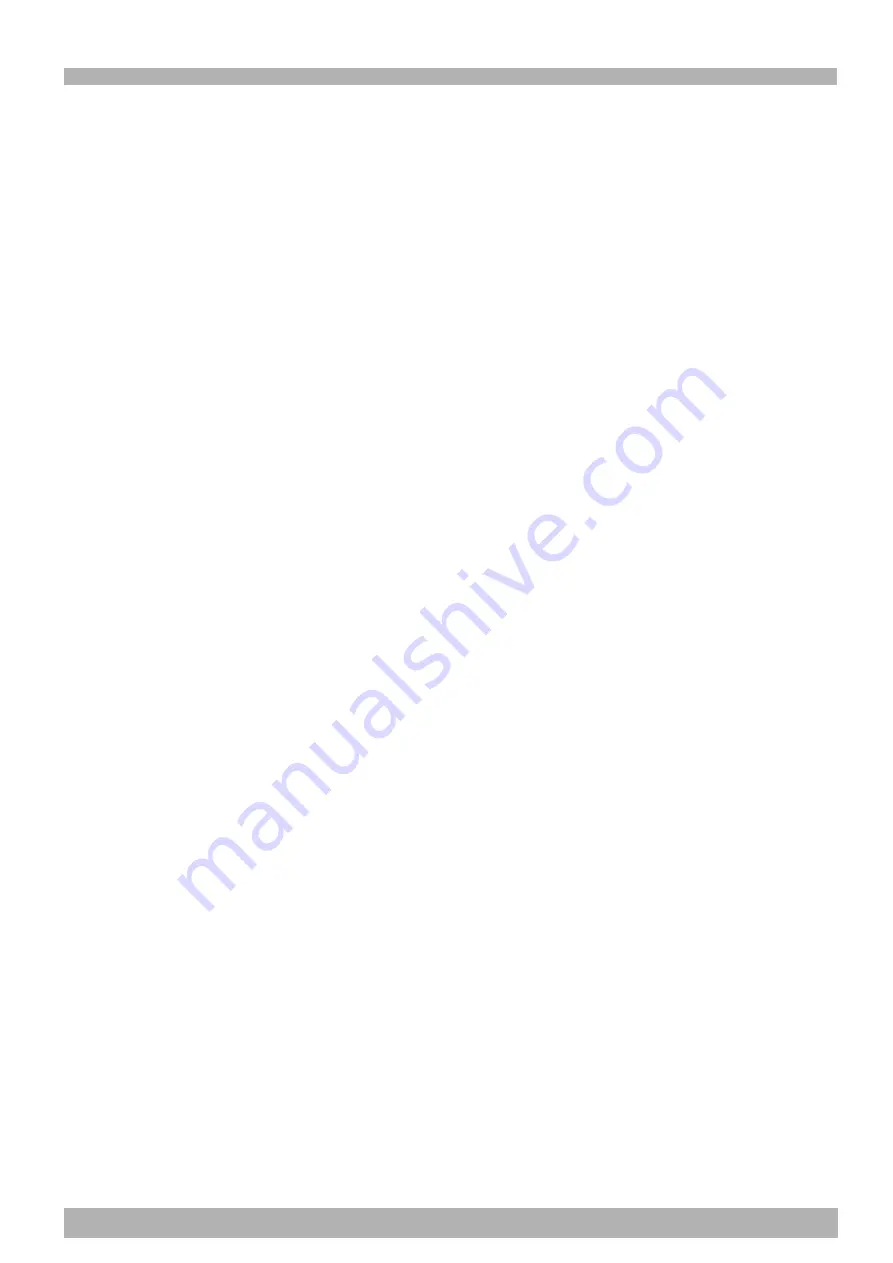
3
2
[System design safety points]
w
WARNING
• Refer to this manual for details on the operating status of the robot controller and
to related instruction manuals. Design and configure the system including the
robot controller so that it will always work safely.
• The robot controller has an emergency stop terminal to trigger emergency stop.
Using this terminal, prepare a physical interlock circuit so that the system
including the robot controller will work safely.
c
CAUTION
• Do not bundle control lines or communication cables together or in close contact with the
robot controller main circuit or power lines. As a general rule, separate them by at least
100mm. Noise in the main circuit or power lines may cause faulty operation or malfunctions.
• Data (programs, point data, etc.) stored in the robot controller is not guaranteed to be
unchanged, so be sure to back it up onto an external storage device.
[Installation safety points]
w
WARNING
• Securely install the connectors into the robot controller, and when wiring the
connectors, make the crimp, press-contact or solder connections correctly using
the tool specified by the manufacturer.
• Always shut off all phases of the power supply externally before starting
installation or wiring work. Failure to shut off all phases could lead to electrical
shocks or product damage.
c
CAUTION
• Use the robot controller within the environment specifications listed in this manual. Using the
controller in an environment outside the specification range could lead to electrical shocks,
fires, malfunctions, product damage or lower performance.
• Tighten the screws on the robot controller firmly to make secure connections.
• Never directly touch the conductive sections or electronic components other than the rotary
switches and DIP switches on the outside panel of the robot controller.
• Securely attach each connector cable connector into the receptacles or sockets. Poor
connections will cause faulty operation or malfunctions.
[Wiring safety points]
w
WARNING
• Always shut off all phases of the power supply externally before starting
installation or wiring work. Failure to shut off all phases could lead to electrical
shocks or product damage.
• Always attach the terminal cover (supplied) before turning on the power to the
robot controller after installation and wiring work are complete. Failure to attach
the terminal cover could lead to fire, electrical shock, product damage or
malfunctions.
c
CAUTION
• Tighten the terminal screws within the specified torque ranges. A loose terminal screw could
lead to short-circuit, faulty operation or malfunctions. However, if the terminal screw is too
tight, short-circuit, faulty operation or malfunctions could also occur due to screw damage.
• Make sure that no foreign matter such as cutting chips or wire scraps do not enter the robot
controller.
• Always store the cables connected to the robot controller in a conduit or clamp them securely
in place. If the cables are not stored in a conduit or properly clamped, excessive play or
movement or mistakenly pulling on the cable might damage the connector or cables, and poor
cable contact may lead to faulty operation or malfunctions.
• When disconnecting the cable, detach by gripping the connector itself and not by tugging on
the cable. Loosen the screws on the connector (if fastened with the screws), and then
disconnect the cable. Detaching by pulling on the cable itself may damage the connector or
cables, and poor cable contact may lead to faulty operation or malfunctions.
Summary of Contents for RCX141
Page 1: ...User s Manual ENGLISH E YAMAHA 4 AXIS ROBOT CONTROLLER E93 Ver 2 02 RCX141 ...
Page 2: ......
Page 16: ...viii MEMO ...
Page 18: ...MEMO ...
Page 24: ...1 6 MEMO ...
Page 26: ...MEMO ...
Page 34: ...2 8 MEMO ...
Page 36: ...MEMO ...
Page 54: ...3 18 MEMO ...
Page 290: ...4 232 MEMO ...
Page 292: ...MEMO ...
Page 316: ...5 24 MEMO ...
Page 318: ...MEMO ...
Page 326: ...6 8 MEMO ...
Page 328: ...MEMO ...
Page 338: ...7 10 MEMO ...
Page 340: ...MEMO ...
Page 346: ...MEMO ...
Page 401: ...MEMO ...