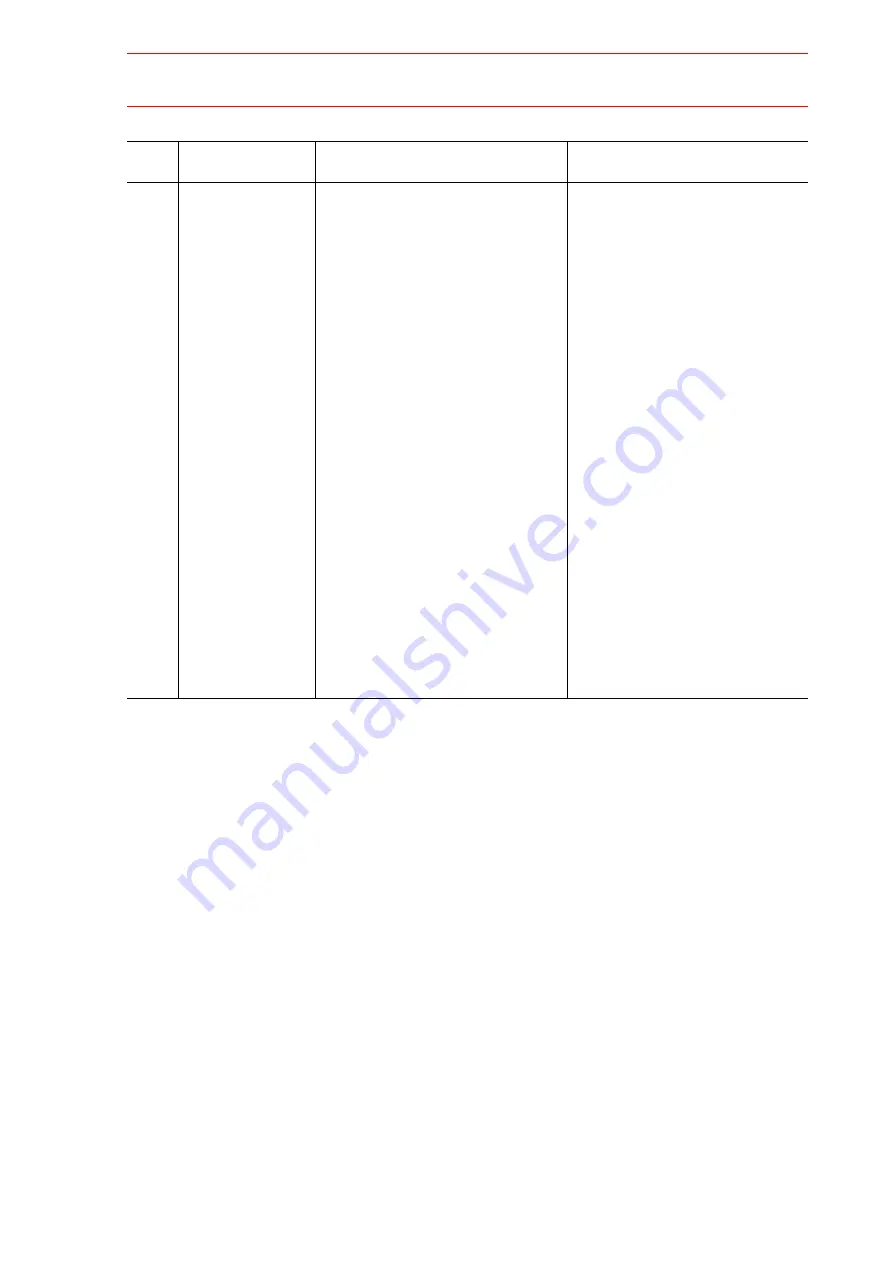
10.3 Alarm Message List
10-19
1309
OVERLOAD
(CONTINU
Robot/Statio
[Axis Data]
The motor torque displayed by axis data
exceeded rated torque for a long time (a fe
seconds - a few minutes). It may have
burned the motor.
• The wrong wiring, the breaking of the
UVW wire for the motor
• The type of motor was not correct.
• The motor was moved by external power.
• It interfered with an outside equipment.
• Defective WRCA01, WRCF01 circuit board
• Defective amplifier
• Defective motor (encoder)
• Check whether the robot interferes with
the outside equipment. If the robot inter
feres, remove the cause.
• Check the connection of UVW wire of
motor again. And check the breaking of
the wire.
• There is a possibility the robot moves by
extra load. Check the motion status of
robot again and reduce the teaching
speed. Then confirm the reoccurrence.
<Error in robot axis>
Check that the type of motor is the same
as the one described in the manual. If
the type is not correct, replace it with the
correct motor.
<Error in external axis>
Check that the type of motor set by sys-
tem configuration is the same as the
actual installed one. If set data by sys-
tem configuration is correct, replace
installed motor with correct one. If set
data by system configuration is not cor
rect, set the correct system configura-
tion.
• If the error occurs again, replace
WRCA01 and/or WRCF01 circuit board.
• Replace the amplifier, motor for axis
where the error occurred.
Alarm Message List
Alarm
Number
Message
Cause
Remedy
Summary of Contents for SK300X
Page 2: ......
Page 4: ...SK300X Manipulator Manual XRC 2001 ii MOTOMAN NOTES...
Page 7: ...INTRODUCTION MOTOMAN 1 3 SK300X Manipulator Manual XRC 2001 NOTES...
Page 21: ...viii...
Page 25: ...xii...
Page 41: ...1 7 Notes on MOTOMAN Disposal 1 16...
Page 59: ...4 3 Connection Methods 4 12...
Page 67: ...6 1 Movement of the Axes 6 4...
Page 73: ...8 2...
Page 74: ......
Page 93: ...3 3 Location 3 6...
Page 99: ...4 2 Cable Connection 4 6...
Page 103: ...5 4 Dimensions and Working Range 5 4 Fig 10 b Dimesions and Working Range YR SK300 J1...
Page 104: ...5 4 Dimensions and Working Range 5 5 Fig 10 c Dimesions and Working Range YR SK300 J2...
Page 109: ...6 2 Wrist Flange 6 4...
Page 133: ...9 2 Notes on Maintenance Procedures 9 18...
Page 136: ...11 1 S Axis Driving Unit 11 1 11 Parts List 11 1 S Axis Driving Unit...
Page 138: ...11 2 L U Axis Driving Unit 1 11 3 11 2 L U Axis Driving Unit 1...
Page 140: ...11 3 L U Axis Driving Unit 2 11 5 11 3 L U Axis Driving Unit 2...
Page 234: ...2 8 General I O Signal Assignment 2 72...
Page 270: ...4 4 Recommended Spare Parts 4 30...
Page 285: ...xiv...
Page 286: ...Setup Diagnosis...
Page 287: ......
Page 289: ...1 2...
Page 297: ...2 1 Protection Through Security Mode Settings 2 8...
Page 395: ...3 17 File Initialize 3 98...
Page 417: ...4 2 Addition of Base and Station Axis 4 22...
Page 435: ...5 6 Position Data When Power is Turned ON OFF 5 18...
Page 436: ...Hardware...
Page 437: ......
Page 447: ...6 4 Equipment Configuration 6 10...
Page 456: ...8 8 Open Phase Check 8 8...
Page 476: ...9 4 Recommended Spare Parts 9 20...
Page 477: ...Alarm Error...
Page 478: ......
Page 523: ......
Page 524: ......
Page 525: ......
Page 526: ......
Page 527: ......
Page 528: ......
Page 529: ......
Page 530: ......
Page 531: ......
Page 532: ......
Page 533: ......
Page 534: ......
Page 535: ......
Page 536: ......
Page 537: ......
Page 538: ......
Page 539: ......
Page 540: ......
Page 541: ......
Page 542: ......
Page 543: ......
Page 544: ......
Page 545: ......
Page 546: ......
Page 547: ......
Page 548: ......
Page 549: ......
Page 550: ......
Page 551: ......
Page 552: ......
Page 553: ......