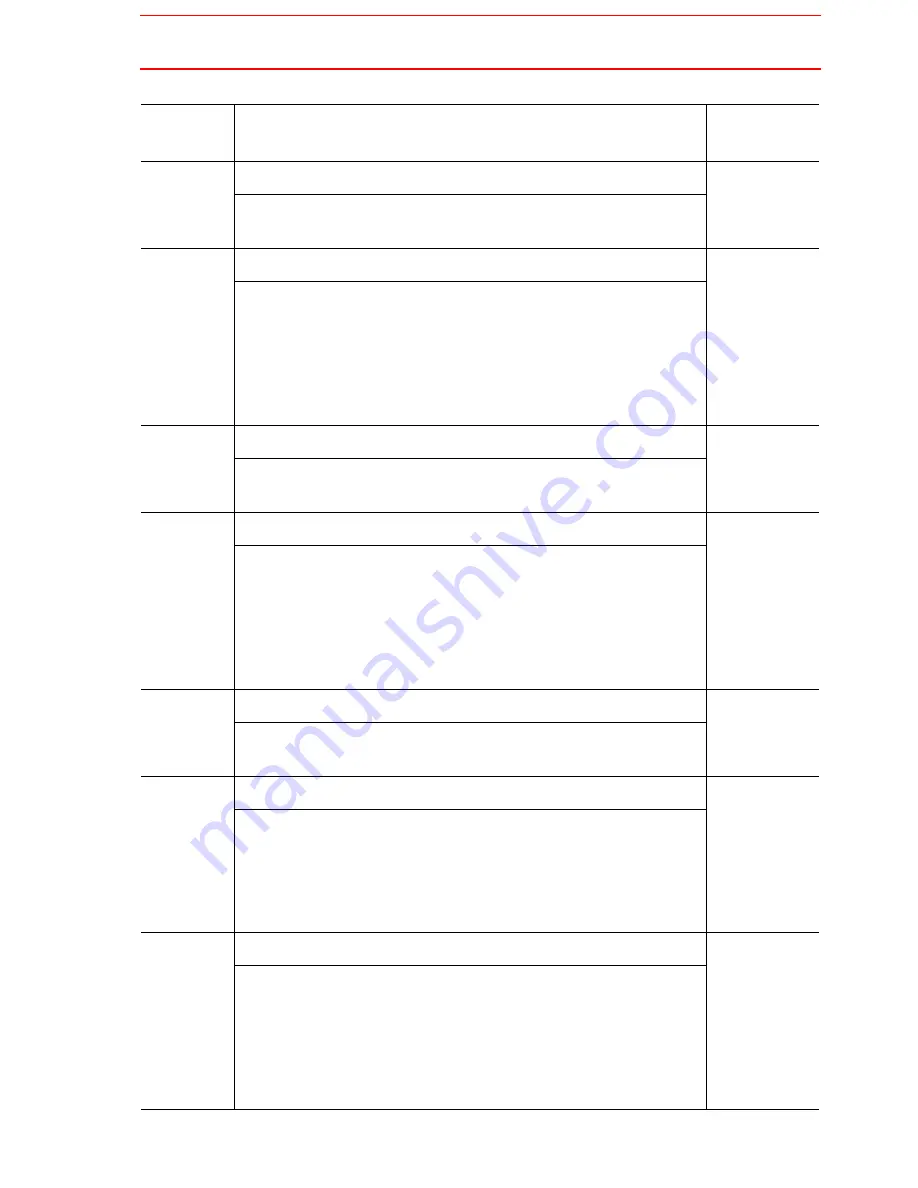
2.4 I/O Unit (JZRCR-XCO02B)
2-21
DIN
CN44 -7
-8
Direct-in 4
Open
Direct-in4 is for future use.
FORCE1
CN40 -1
-2
FORCE2
CN40 -3
-4
Forced reset input
Open
Do not use the “FORCE” (Forced release) input.
If the “FORCE” input should be used for an unavoidable reason, be
sure to use a switch with a key. The systems manager is responsible
for storage of the key.
When “FORCE” is input, all the deadman switches become invalid,
so handle with extreme care.
RDY
CN06-11
-12
Optional board Ready signal
Disabled by
Jumper lead
Use to add safety circuit conditions.
FST1
CN40 -5
-6
FST2
CN40 -7
-8
Full-speed test
Open
PLAY normal speed is selected in PLAY mode, and TEACH normal
speed is selected in TEACH mode.
S-SP1
CN40 -9
-10
Switches Valid/Invalid of HSW/DSW.
Open
When open, DSW valid
When short-circuited, HSW valid
S-SP2
CN40-11
-12
Switches between 1st Safety Speed and 2nd Safety Speed.
Open
1st Safety Speed: the speed is limited to 16 % of PLAY maximum
speed.
2nd Safety Speed: the speed is limited to 2 % of PLAY maximum
speed.
When open, 1st Safety Speed is selected
Whe short-circuited, 2nd Safety Speed is selected.
HSW1
CN40-13
-14
HSW2
CN40-15
-16
Hanger switch
Open
Validates the hanger switch with S-SP1 short-circuited.
When open, a normal speed
When short-circuited, a safety speed (according to the setting of S-
SP2)
Specific Input List (XCO02B)
Terminal
Input Name / Function
Factory
Setting
Summary of Contents for SK300X
Page 2: ......
Page 4: ...SK300X Manipulator Manual XRC 2001 ii MOTOMAN NOTES...
Page 7: ...INTRODUCTION MOTOMAN 1 3 SK300X Manipulator Manual XRC 2001 NOTES...
Page 21: ...viii...
Page 25: ...xii...
Page 41: ...1 7 Notes on MOTOMAN Disposal 1 16...
Page 59: ...4 3 Connection Methods 4 12...
Page 67: ...6 1 Movement of the Axes 6 4...
Page 73: ...8 2...
Page 74: ......
Page 93: ...3 3 Location 3 6...
Page 99: ...4 2 Cable Connection 4 6...
Page 103: ...5 4 Dimensions and Working Range 5 4 Fig 10 b Dimesions and Working Range YR SK300 J1...
Page 104: ...5 4 Dimensions and Working Range 5 5 Fig 10 c Dimesions and Working Range YR SK300 J2...
Page 109: ...6 2 Wrist Flange 6 4...
Page 133: ...9 2 Notes on Maintenance Procedures 9 18...
Page 136: ...11 1 S Axis Driving Unit 11 1 11 Parts List 11 1 S Axis Driving Unit...
Page 138: ...11 2 L U Axis Driving Unit 1 11 3 11 2 L U Axis Driving Unit 1...
Page 140: ...11 3 L U Axis Driving Unit 2 11 5 11 3 L U Axis Driving Unit 2...
Page 234: ...2 8 General I O Signal Assignment 2 72...
Page 270: ...4 4 Recommended Spare Parts 4 30...
Page 285: ...xiv...
Page 286: ...Setup Diagnosis...
Page 287: ......
Page 289: ...1 2...
Page 297: ...2 1 Protection Through Security Mode Settings 2 8...
Page 395: ...3 17 File Initialize 3 98...
Page 417: ...4 2 Addition of Base and Station Axis 4 22...
Page 435: ...5 6 Position Data When Power is Turned ON OFF 5 18...
Page 436: ...Hardware...
Page 437: ......
Page 447: ...6 4 Equipment Configuration 6 10...
Page 456: ...8 8 Open Phase Check 8 8...
Page 476: ...9 4 Recommended Spare Parts 9 20...
Page 477: ...Alarm Error...
Page 478: ......
Page 523: ......
Page 524: ......
Page 525: ......
Page 526: ......
Page 527: ......
Page 528: ......
Page 529: ......
Page 530: ......
Page 531: ......
Page 532: ......
Page 533: ......
Page 534: ......
Page 535: ......
Page 536: ......
Page 537: ......
Page 538: ......
Page 539: ......
Page 540: ......
Page 541: ......
Page 542: ......
Page 543: ......
Page 544: ......
Page 545: ......
Page 546: ......
Page 547: ......
Page 548: ......
Page 549: ......
Page 550: ......
Page 551: ......
Page 552: ......
Page 553: ......