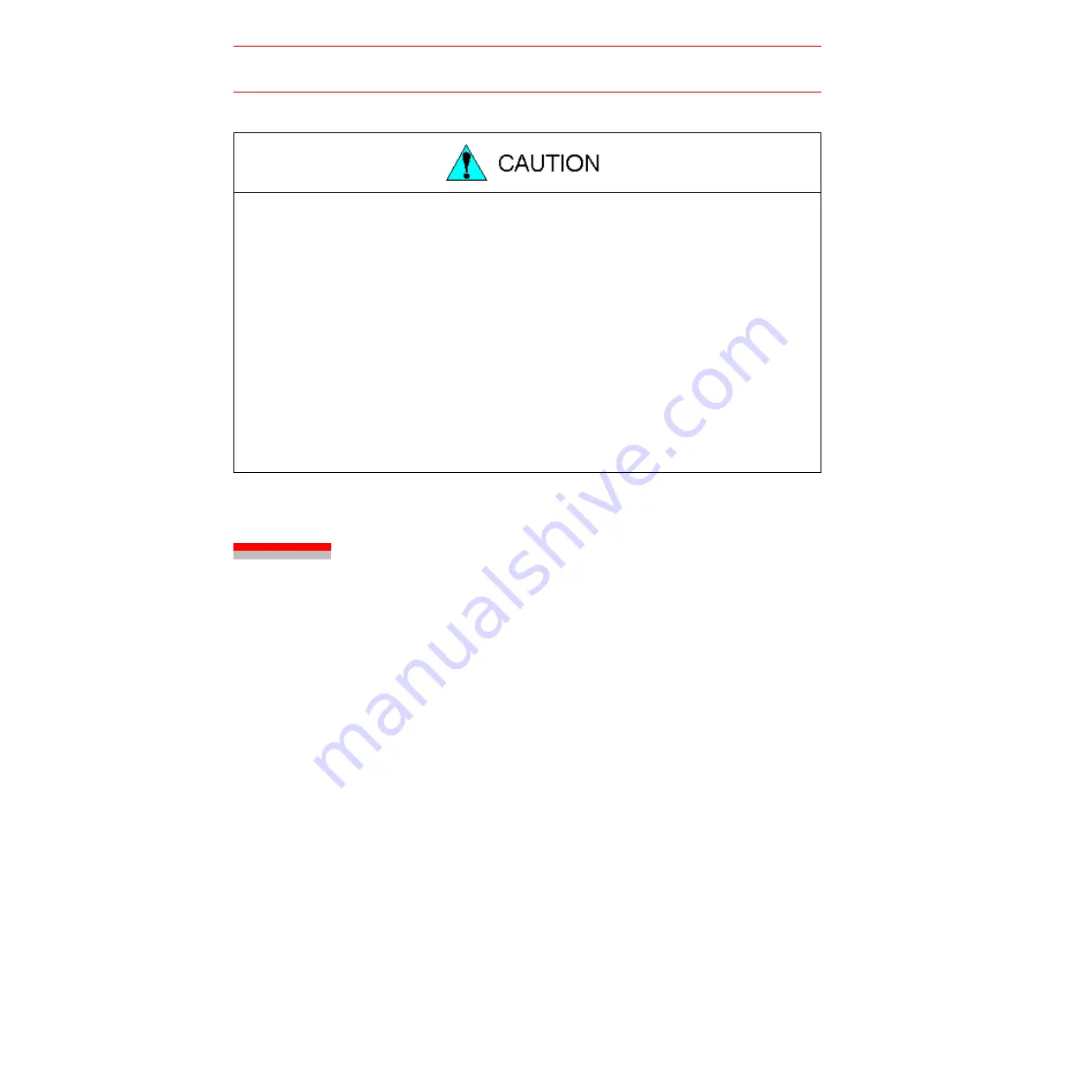
4.1 Notes on Cable Junctions
4-2
4.1
Notes on Cable Junctions
• The cables that connect the controller to peripheral equipment are low voltage circuits.
Keep controller signal cables away from the primary power circuit. High voltage power
lines should not be run in parallel to controller signal cables. If running parallel cables is
unavoidable, use metal ducts or conduit to isolate electrical signal interference. If cables
must be crossed, run the power cables perpendicular across the signal cables.
• Confirm the connector and cable numbers to prevent misconnection and equipment dam-
age. One connects the manipulator and XRC. Another connects the XRC and peripheral
equipment. A wrong connection can cause damage to electronic equipment.
• Clear the area of all unauthorized personnel while making cable connections. Place all
cables in a covered cable channel in the floor.
• Wiring must be performed only by authorized personnel.
Incorrect wiring may cause fire and electric shock.
• Perform wiring in accordance with the rated capacity as specified in
the Instructions.
Incorrect wiring may cause fire or mechanical breakdown.
• Be sure the power circuit screws are securely tightened.
Loose power circuit wires can cause fire and electric shock.
• Do not handle the circuit board directly by hand.
The IC board may malfunction due to static electricity.
Summary of Contents for SK300X
Page 2: ......
Page 4: ...SK300X Manipulator Manual XRC 2001 ii MOTOMAN NOTES...
Page 7: ...INTRODUCTION MOTOMAN 1 3 SK300X Manipulator Manual XRC 2001 NOTES...
Page 21: ...viii...
Page 25: ...xii...
Page 41: ...1 7 Notes on MOTOMAN Disposal 1 16...
Page 59: ...4 3 Connection Methods 4 12...
Page 67: ...6 1 Movement of the Axes 6 4...
Page 73: ...8 2...
Page 74: ......
Page 93: ...3 3 Location 3 6...
Page 99: ...4 2 Cable Connection 4 6...
Page 103: ...5 4 Dimensions and Working Range 5 4 Fig 10 b Dimesions and Working Range YR SK300 J1...
Page 104: ...5 4 Dimensions and Working Range 5 5 Fig 10 c Dimesions and Working Range YR SK300 J2...
Page 109: ...6 2 Wrist Flange 6 4...
Page 133: ...9 2 Notes on Maintenance Procedures 9 18...
Page 136: ...11 1 S Axis Driving Unit 11 1 11 Parts List 11 1 S Axis Driving Unit...
Page 138: ...11 2 L U Axis Driving Unit 1 11 3 11 2 L U Axis Driving Unit 1...
Page 140: ...11 3 L U Axis Driving Unit 2 11 5 11 3 L U Axis Driving Unit 2...
Page 234: ...2 8 General I O Signal Assignment 2 72...
Page 270: ...4 4 Recommended Spare Parts 4 30...
Page 285: ...xiv...
Page 286: ...Setup Diagnosis...
Page 287: ......
Page 289: ...1 2...
Page 297: ...2 1 Protection Through Security Mode Settings 2 8...
Page 395: ...3 17 File Initialize 3 98...
Page 417: ...4 2 Addition of Base and Station Axis 4 22...
Page 435: ...5 6 Position Data When Power is Turned ON OFF 5 18...
Page 436: ...Hardware...
Page 437: ......
Page 447: ...6 4 Equipment Configuration 6 10...
Page 456: ...8 8 Open Phase Check 8 8...
Page 476: ...9 4 Recommended Spare Parts 9 20...
Page 477: ...Alarm Error...
Page 478: ......
Page 523: ......
Page 524: ......
Page 525: ......
Page 526: ......
Page 527: ......
Page 528: ......
Page 529: ......
Page 530: ......
Page 531: ......
Page 532: ......
Page 533: ......
Page 534: ......
Page 535: ......
Page 536: ......
Page 537: ......
Page 538: ......
Page 539: ......
Page 540: ......
Page 541: ......
Page 542: ......
Page 543: ......
Page 544: ......
Page 545: ......
Page 546: ......
Page 547: ......
Page 548: ......
Page 549: ......
Page 550: ......
Page 551: ......
Page 552: ......
Page 553: ......