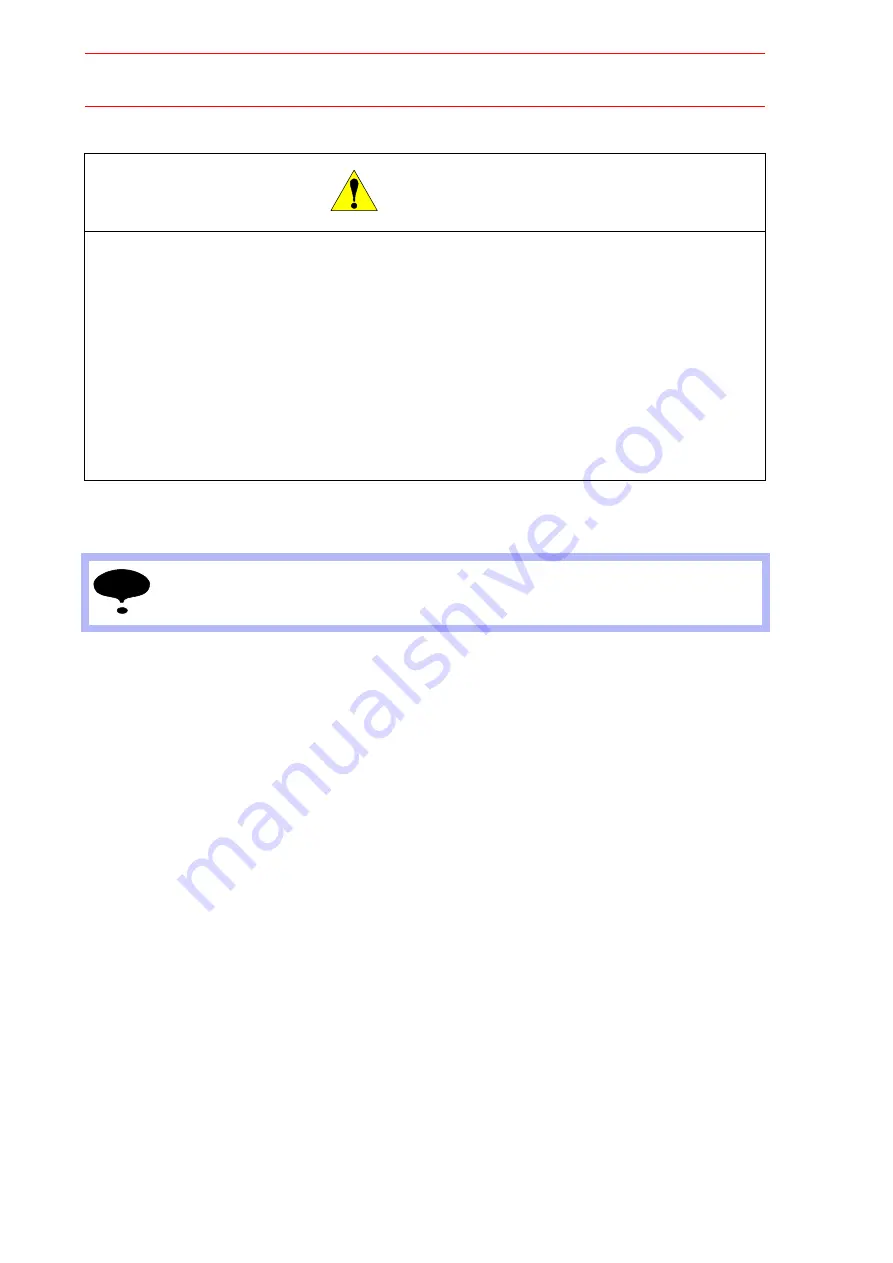
3.1 Home Position Calibration
3-2
3.1.1
Home Position Calibration
Home position calibration is an operation in which the home position and encoder zero posi-
tion coincide. Although this operation is performed prior to shipment at the factory, the follow-
ing cases require this operation to be performed again.
• Change in the combination of the manipulator and XRC
• Replacement of the motor or encoder
• Clearing stored memory (by replacement of XCP01 board, weak battery, etc.)
• Home position deviation caused by hitting the manipulator against a workpiece, etc.
To calibrate the home position, move the manipulator to the home position using the axis
keys. There are two operations for home position calibration:
• All the axes can be moved at the same time
• Axes can be moved individually
If the absolute data of the home position is already known, set the absolute data again after
completing home position registration.
• Perform the following inspection procedures prior to teaching the
manipulator. If problems are found, correct them immediately, and be
sure that all other necessary tasks have been performed.
- Check for problems in manipulator movement.
- Check for damage to the insulation and sheathing of external wires.
- Always return the programming pendant to its hook on the XRC cabi-
net after use.
If the programming pendant is inadvertently left on the manipulator, a fixture, or on the
floor, the manipulator or a tool could collide with it during manipulator movement, possibly
causing injury or equipment damage.
Teaching and playback are not possible before home position calibration is complete.
In a system with two or more manipulators, the home position of all the manipulators must
be calibrated before starting teaching or playback.
C A U T I O N
N OT E
Summary of Contents for SK300X
Page 2: ......
Page 4: ...SK300X Manipulator Manual XRC 2001 ii MOTOMAN NOTES...
Page 7: ...INTRODUCTION MOTOMAN 1 3 SK300X Manipulator Manual XRC 2001 NOTES...
Page 21: ...viii...
Page 25: ...xii...
Page 41: ...1 7 Notes on MOTOMAN Disposal 1 16...
Page 59: ...4 3 Connection Methods 4 12...
Page 67: ...6 1 Movement of the Axes 6 4...
Page 73: ...8 2...
Page 74: ......
Page 93: ...3 3 Location 3 6...
Page 99: ...4 2 Cable Connection 4 6...
Page 103: ...5 4 Dimensions and Working Range 5 4 Fig 10 b Dimesions and Working Range YR SK300 J1...
Page 104: ...5 4 Dimensions and Working Range 5 5 Fig 10 c Dimesions and Working Range YR SK300 J2...
Page 109: ...6 2 Wrist Flange 6 4...
Page 133: ...9 2 Notes on Maintenance Procedures 9 18...
Page 136: ...11 1 S Axis Driving Unit 11 1 11 Parts List 11 1 S Axis Driving Unit...
Page 138: ...11 2 L U Axis Driving Unit 1 11 3 11 2 L U Axis Driving Unit 1...
Page 140: ...11 3 L U Axis Driving Unit 2 11 5 11 3 L U Axis Driving Unit 2...
Page 234: ...2 8 General I O Signal Assignment 2 72...
Page 270: ...4 4 Recommended Spare Parts 4 30...
Page 285: ...xiv...
Page 286: ...Setup Diagnosis...
Page 287: ......
Page 289: ...1 2...
Page 297: ...2 1 Protection Through Security Mode Settings 2 8...
Page 395: ...3 17 File Initialize 3 98...
Page 417: ...4 2 Addition of Base and Station Axis 4 22...
Page 435: ...5 6 Position Data When Power is Turned ON OFF 5 18...
Page 436: ...Hardware...
Page 437: ......
Page 447: ...6 4 Equipment Configuration 6 10...
Page 456: ...8 8 Open Phase Check 8 8...
Page 476: ...9 4 Recommended Spare Parts 9 20...
Page 477: ...Alarm Error...
Page 478: ......
Page 523: ......
Page 524: ......
Page 525: ......
Page 526: ......
Page 527: ......
Page 528: ......
Page 529: ......
Page 530: ......
Page 531: ......
Page 532: ......
Page 533: ......
Page 534: ......
Page 535: ......
Page 536: ......
Page 537: ......
Page 538: ......
Page 539: ......
Page 540: ......
Page 541: ......
Page 542: ......
Page 543: ......
Page 544: ......
Page 545: ......
Page 546: ......
Page 547: ......
Page 548: ......
Page 549: ......
Page 550: ......
Page 551: ......
Page 552: ......
Page 553: ......