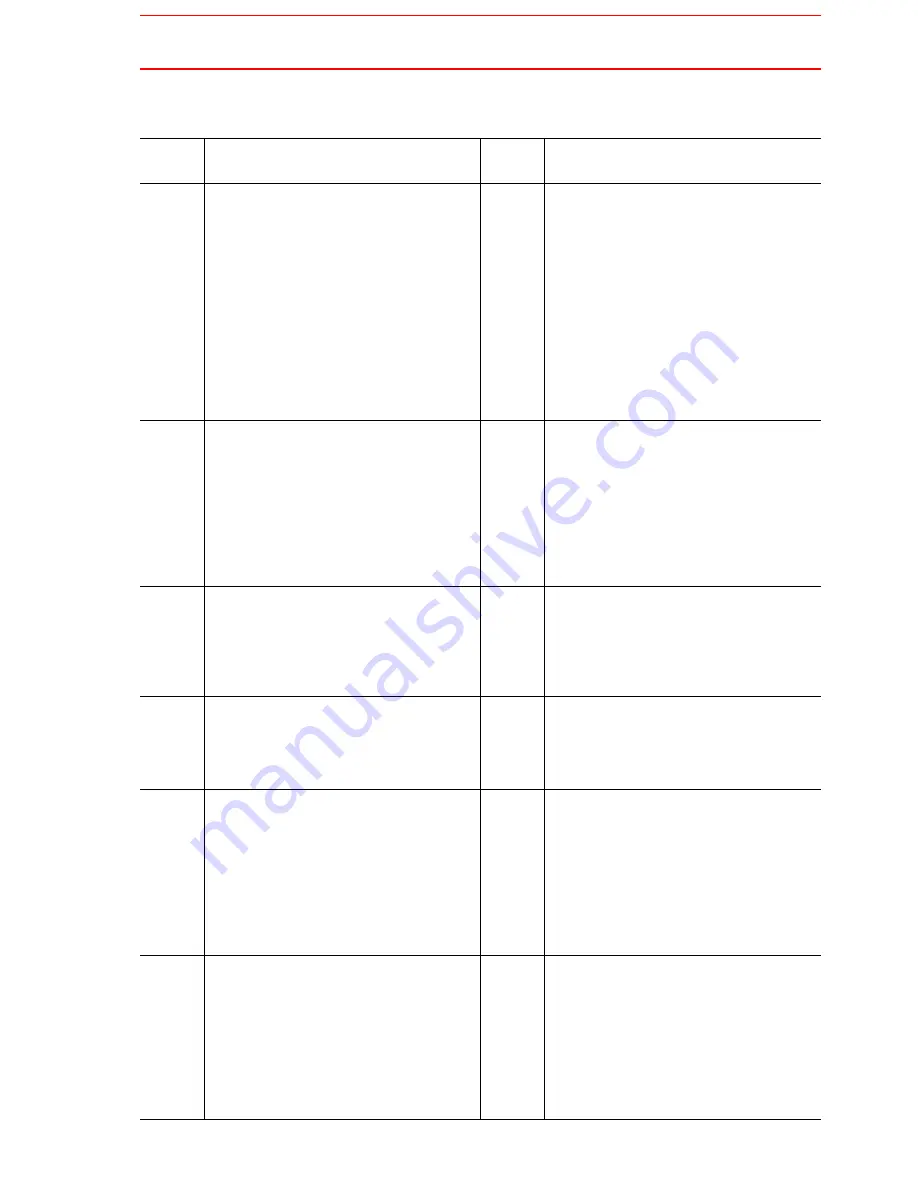
2.8 General I/O Signal Assignment
2-69
Specific Output List XCO02B (Spot Welding)
Logical
Number
Output Name / Function
Logical
Number
Output Name / Function
3010
RUNNING
This signal signifies that the job is run-
ning. (Signifies that the job is running,
system status is waiting reserved start,
or test run is running.) This signal status
is the same status as [START] in the
playback panel.
3023
INTERMEDIATE START OK (Sequence
continues)
This signal turns ON when the manipula-
tor operates. It turns OFF when the cur-
rently executed line is moved with the
cursor or when editing operation is car-
ried out after HOLD is applied during
operation. Therefore, this signal can be
used as a restart interlock after a HOLD
is applied. However, it also turns ON in
the TEACH mode and TEACH MODE
SELECTED signal must be referred
togather.
3011
SERVO IS O
This signal signifies that the servo power
is turned ON, internal processing such
as current position creation is complete,
and the system is able to receive the
START command. This signal turns OFF
when the servo power supply turns OFF.
It can be used for XRC status diagnosis
for an external start.
3024
IN CUBE 3
This signal turns ON when the current
tool center point lies inside a pre-defined
space (Cube 3). Use this signal to pre-
vent interference with other manipulators
and jigs.
3012
TOP MASTER JOB
This signal signifies that the execution
position is the top of the master job. This
signal can be used to confirm that the
master job has been called.
*2
3025
IN CUBE 4
This signal turns ON when the current
tool center point lies inside a pre-defined
space (Cube 4). Use this signal to pre-
vent interference with other manipulators
and jigs.
3013
ALARM/ERROR OCCURRING
This signal signifies that an alarm or an
error occurred. If a major error occurs,
this signal remains ON until the main
power is turned OFF.
3040
*4
WELD ON/OFF
Outputs a signal input from the interlock
panel, etc.considering the robot status.
3014
BATTERY ALARM
This signal turns ON to notify that the
battery requires replacing when the volt-
age drops from the battery for backup
memory of the encoder. Major problems
may result if memory data is lost
because of an expired battery. It is rec-
ommended to avoid these problems by
using this signal as a warning signal.
3041
*3
WELD ERROR RESET
This signal commands the reset error
status of the welder. This is operated
with the programing pendant operation.
3015 to
3017
REMOTE/PLAY/TEACH MODE
SELECTED
This signal notifies the current mode set-
ting. These signals are synchronized
with the lamps [REMOTE] and [MODE]
in the playback panel. The signal corre-
sponding to the selected mode turns ON.
3042 to
3045
*3
WELD CONDITION (Level signals)
1(1), 2(2), 4(3) , 8(4), 16(5), 32(6), 64(7),
128(8)
Sets the welding conditions for the
welder.
The output format can be selected as
binary or discrete (bit number). It can
handle up to 255 conditions. Most-signif-
icant bit is the parity bit (when specified).
Summary of Contents for SK300X
Page 2: ......
Page 4: ...SK300X Manipulator Manual XRC 2001 ii MOTOMAN NOTES...
Page 7: ...INTRODUCTION MOTOMAN 1 3 SK300X Manipulator Manual XRC 2001 NOTES...
Page 21: ...viii...
Page 25: ...xii...
Page 41: ...1 7 Notes on MOTOMAN Disposal 1 16...
Page 59: ...4 3 Connection Methods 4 12...
Page 67: ...6 1 Movement of the Axes 6 4...
Page 73: ...8 2...
Page 74: ......
Page 93: ...3 3 Location 3 6...
Page 99: ...4 2 Cable Connection 4 6...
Page 103: ...5 4 Dimensions and Working Range 5 4 Fig 10 b Dimesions and Working Range YR SK300 J1...
Page 104: ...5 4 Dimensions and Working Range 5 5 Fig 10 c Dimesions and Working Range YR SK300 J2...
Page 109: ...6 2 Wrist Flange 6 4...
Page 133: ...9 2 Notes on Maintenance Procedures 9 18...
Page 136: ...11 1 S Axis Driving Unit 11 1 11 Parts List 11 1 S Axis Driving Unit...
Page 138: ...11 2 L U Axis Driving Unit 1 11 3 11 2 L U Axis Driving Unit 1...
Page 140: ...11 3 L U Axis Driving Unit 2 11 5 11 3 L U Axis Driving Unit 2...
Page 234: ...2 8 General I O Signal Assignment 2 72...
Page 270: ...4 4 Recommended Spare Parts 4 30...
Page 285: ...xiv...
Page 286: ...Setup Diagnosis...
Page 287: ......
Page 289: ...1 2...
Page 297: ...2 1 Protection Through Security Mode Settings 2 8...
Page 395: ...3 17 File Initialize 3 98...
Page 417: ...4 2 Addition of Base and Station Axis 4 22...
Page 435: ...5 6 Position Data When Power is Turned ON OFF 5 18...
Page 436: ...Hardware...
Page 437: ......
Page 447: ...6 4 Equipment Configuration 6 10...
Page 456: ...8 8 Open Phase Check 8 8...
Page 476: ...9 4 Recommended Spare Parts 9 20...
Page 477: ...Alarm Error...
Page 478: ......
Page 523: ......
Page 524: ......
Page 525: ......
Page 526: ......
Page 527: ......
Page 528: ......
Page 529: ......
Page 530: ......
Page 531: ......
Page 532: ......
Page 533: ......
Page 534: ......
Page 535: ......
Page 536: ......
Page 537: ......
Page 538: ......
Page 539: ......
Page 540: ......
Page 541: ......
Page 542: ......
Page 543: ......
Page 544: ......
Page 545: ......
Page 546: ......
Page 547: ......
Page 548: ......
Page 549: ......
Page 550: ......
Page 551: ......
Page 552: ......
Page 553: ......