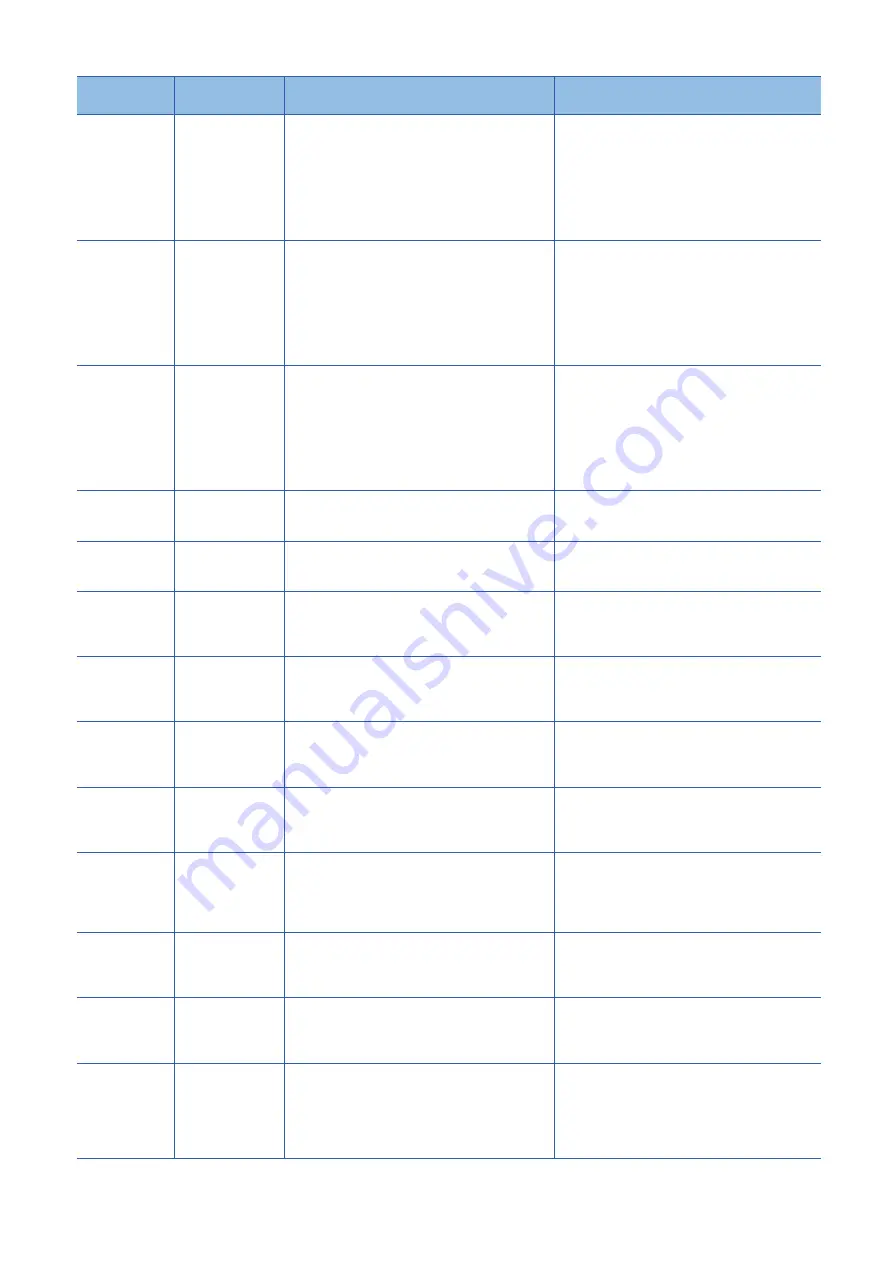
592
14 TROUBLESHOOTING
14.5 List of Error Codes
1905H
Hardware stroke limit
(+)
The hardware stroke limit (upper limit signal FLS) is
turned OFF during operation.
[Operation status at error occurrence]
The system stops with the setting (deceleration stop/
sudden stop) of the detailed parameter 2 Sudden stop
selection (stop group 1).
(Note that the deceleration stop only occurs during the
manual pulse generator operation.)
After making an axis error reset, perform manual
control operation to move the axis to the other position
in order that the upper limit signal (FLS) will not turn
OFF.
1906H
Hardware stroke limit
(-)
Start is requested when the hardware stroke limit (lower
limit signal RLS) is turned OFF.
[Operation status at error occurrence]
The system does not start.
• Check the wiring of lower limit signal RLS.
• Check if the specification of the limit switch and the
setting of the "[Pr.22] Input signal logic selection"
match.
• If hardware stroke limit (limit switch) is unnecessary
system for installation, wire to always turn ON the
lower limit signal (RLS) input of the Simple Motion
module.
1907H
Hardware stroke limit
(-)
The hardware stroke limit (lower limit signal RLS) is
turned OFF during operation.
[Operation status at error occurrence]
The system stops with the setting (deceleration stop/
sudden stop) of the detailed parameter 2 Sudden stop
selection (stop group 1).
(Note that the deceleration stop only occurs during the
manual pulse generator operation.)
After making an axis error reset, perform manual
control operation to move the axis to the other position
in order that the lower limit signal (RLS) will not turn
OFF.
1908H
Stop signal ON at
start
Start is requested when a stop signal is turned ON.
[Operation status at error occurrence]
The system does not start.
After clearing the stop command status, then review
the timing of start.
1909H
Stop signal ON at
start
Start is requested when an external stop is turned ON.
[Operation status at error occurrence]
The system does not start.
After clearing the external stop signal, then review the
timing of start.
190AH
READY OFF
ON
during BUSY
The PLC READY signal is turned from OFF to ON when
BUSY signal is turned ON.
[Operation status at error occurrence]
The READY signal [X0] is not turned ON.
Turn ON the PLC READY signal [Y0] with the BUSY
signals of all axes OFF.
190BH
Unsupported servo
amplifier connection
A servo amplifier/driver which is not supported is
connected.
[Operation status at error occurrence]
The target axis is not connected to the servo amplifier.
Connect supported servo amplifier/driver.
1920H
Start not possible
Start is requested when start is not possible in the axis
operation state.
[Operation status at error occurrence]
The system does not start positioning.
Do not request the start when the axis operation state
is other than "0: Standby", "1: Stopped", and "-2: Step
standby".
1921H
Start not possible
Start is requested when the "[Md.26] Axis operation
status" is "-1: Error".
[Operation status at error occurrence]
The system does not start positioning.
Do not request the start when the axis operation state
is other than "0: Standby", "1: Stopped", and "-2: Step
standby".
1922H
Start not possible
Start is requested when the "[Md.26] Axis operation
status" is "20: Servo amplifier has not been connected/
servo amplifier power OFF".
[Operation status at error occurrence]
The system does not start positioning.
Do not request the start when the axis operation state
is other than "0: Standby", "1: Stopped", and "-2: Step
standby".
1923H
Start not possible
Start is requested when the "[Md.26] Axis operation
status" is "21: Servo OFF".
[Operation status at error occurrence]
The system does not start positioning.
Do not request the start when the axis operation state
is other than "0: Standby", "1: Stopped", and "-2: Step
standby".
1924H
Start not possible
Start is requested when communication with servo
amplifier is error.
[Operation status at error occurrence]
The system does not start positioning.
Check the wiring with the servo amplifier and
connection of connectors.
1925H
Start not possible
Start is requested when the "[Md.26] Axis operation
status" in the axis to be interpolated is "-1: Error", "20:
Servo amplifier has not been connected/servo amplifier
power OFF", and "21: Servo OFF".
[Operation status at error occurrence]
The system does not start positioning.
Do not request the start when the "[Md.26] Axis
operation status" in the axis to be interpolated is other
than "0: Standby", "1: Stopped", and "-2: Step standby".
Error code
(Hexadecimal)
Error name
Error details and causes
Remedy
Summary of Contents for RD77MS16
Page 1: ...MELSEC iQ R Simple Motion Module User s Manual Application RD77MS2 RD77MS4 RD77MS8 RD77MS16 ...
Page 2: ......
Page 316: ...314 9 COMMON FUNCTIONS 9 4 External Input Signal Select Function Program example ...
Page 317: ...9 COMMON FUNCTIONS 9 4 External Input Signal Select Function 315 9 ...
Page 575: ...13 PROGRAMMING 13 4 Positioning Program Examples 573 13 Error reset program Axis stop program ...
Page 643: ......