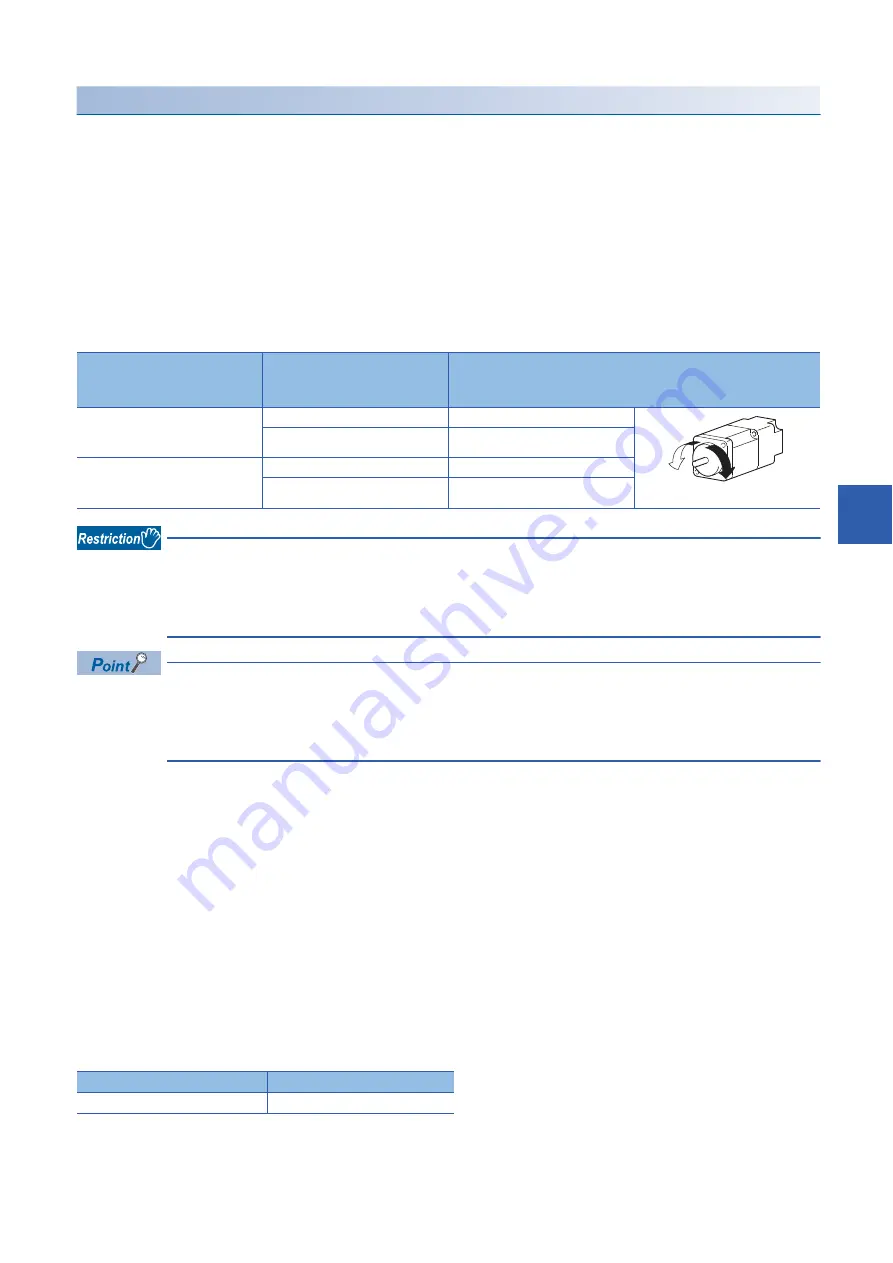
7 EXPANSION CONTROL
7.1 Speed-torque Control
211
7
Continuous operation to torque control mode
■
Operation for continuous operation to torque control mode
In continuous operation to torque control, the torque control can be executed without stopping the operation during the
positioning in position control mode or speed command in speed control mode.
During the continuous operation to torque control mode, the torque control is executed at the command torque set in
"[Cd.150] Target torque at continuous operation to torque control mode" while executing acceleration/deceleration to reach
the speed set in "[Cd.147] Speed limit value at continuous operation to torque control mode".
"[Cd.147] Speed limit value at continuous operation to torque control mode" and "[Cd.150] Target torque at continuous
operation to torque control mode" can be changed any time during the continuous operation to torque control mode. The
relation between the setting value of command torque and the torque generation direction of servomotor is fixed regardless of
the setting of servo parameters "Rotation direction selection/travel direction selection (PA14)" and "Function selection C-B
POL reflection selection at torque control (PC29)".
Regardless of the setting in "Rotation direction selection/travel direction selection (PA14)", set a positive value
when torque command is in CCW direction of servomotor and a negative value when torque command is in
CW direction of servomotor in "[Cd.150] Target torque at continuous operation to torque control mode".
If the setting is incorrect, the motor may rotate in an opposite direction.
• The motor rotates in a direction according to the setting in "[Cd.150] Target torque at continuous operation
to torque control mode". Set the value corresponding to the motor rotation direction in "[Cd.147] Speed limit
value at continuous operation to torque control mode".
• Speed is not limited for reverse torque generation direction.
■
Torque command setting method
During the continuous operation to torque control mode, set time for the command torque to increase from 0% to "[Pr.17]
Torque limit setting value" in "[Cd.151] Torque time constant at continuous operation to torque control mode (Forward
direction)" and for the command torque to decrease from "[Pr.17] Torque limit setting value" to 0% in "[Cd.152] Torque time
constant at continuous operation to torque control mode (Negative direction)". The value at continuous operation to torque
control mode switching request is valid for "[Cd.151]" and "[Cd.152]".
The command torque during the continuous operation to torque control mode is limited with "[Pr.17] Torque limit setting
value".
If torque exceeding the torque limit setting value is commanded, the warning "Torque limit value over" (warning code: 09E4H)
occurs, and the operation is controlled with the torque limit setting value.
Confirm the command torque to servo amplifier with "[Md.123] Torque during command".
During the continuous operation to torque control mode, "Torque limit" ("[Md.108] Servo status1": b13) does not turn ON.
Confirm the current torque value in "[Md.104] Motor current value".
n: Axis No. - 1
"Rotation direction selection/
travel direction selection
(PA14)"
"[Cd.150] Target torque at
continuous operation to
torque control mode"
Torque generation direction of servo motor
0: Forward rotation (CCW) with the
increase of the positioning
address
Positive value (Forward direction)
CCW direction
Negative value (Reverse direction)
CW direction
1: Reverse rotation (CW) with the
increase of the positioning
address
Positive value (Forward direction)
CCW direction
Negative value (Reverse direction)
CW direction
Monitor item
Buffer memory address
[Md.108] Servo status1: b13
2477+100n
CW direction
CCW
direction
Summary of Contents for RD77MS16
Page 1: ...MELSEC iQ R Simple Motion Module User s Manual Application RD77MS2 RD77MS4 RD77MS8 RD77MS16 ...
Page 2: ......
Page 316: ...314 9 COMMON FUNCTIONS 9 4 External Input Signal Select Function Program example ...
Page 317: ...9 COMMON FUNCTIONS 9 4 External Input Signal Select Function 315 9 ...
Page 575: ...13 PROGRAMMING 13 4 Positioning Program Examples 573 13 Error reset program Axis stop program ...
Page 643: ......