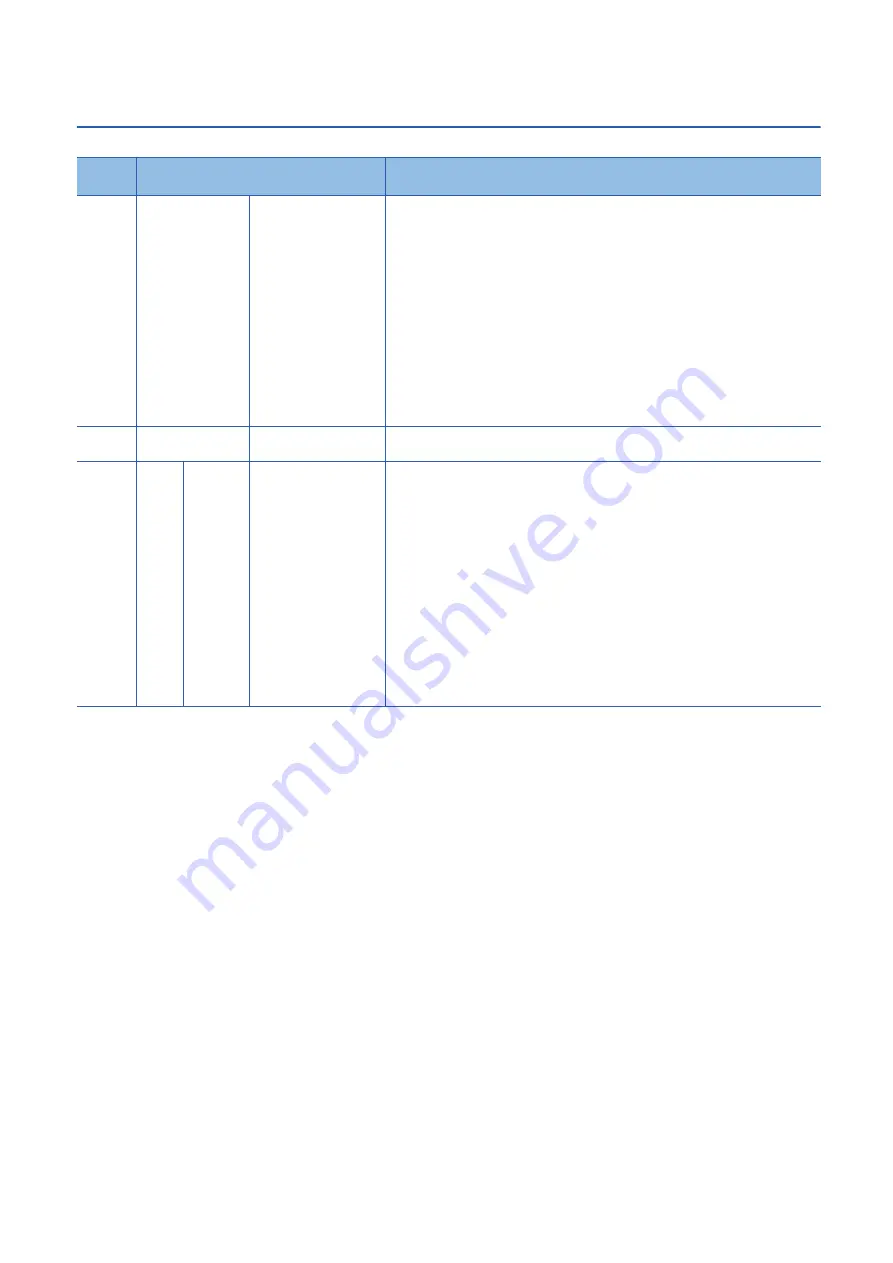
360
11 SPECIFICATIONS OF I/O SIGNALS WITH CPU MODULES
11.3 Details of Output Signals
11.3
Details of Output Signals
The ON/OFF timing and conditions of the output signals are shown below.
*1
The positioning signal, whose axis number exceeds the number of controlled axes, cannot be used.
Device
No.
Signal name
Details
Y0
PLC READY
OFF: PLC READY OFF
ON: PLC
READY
ON
(a) This signal notifies the Simple Motion module that the CPU module is normal.
• It is turned ON/OFF with the program.
(b) When the data (parameter, etc.) are changed, this signal is turned OFF depending on
the parameter. (
Page 542 Memory Configuration and Data Process)
(c)The following processes are carried out when this signal turns from OFF to ON.
• The parameter setting range is checked.
• The READY signal [X0] turns ON.
(d) The following processes are carried out when this signal turns from ON to OFF. In these
cases, the OFF time should be set to 100 ms or more.
• The READY signal [X0] turns OFF.
• The operating axis stops.
• The M code ON signal ([Md.31] Status: b12) for each axis turns OFF, and "0" is stored in
"[Md.25] Valid M code".
(e) When parameters or positioning data (No. 1 to 600) are written from the engineering tool
or CPU module to the flash ROM, this signal will turn OFF.
Y1
All axis servo ON
OFF: Servo OFF
ON: Servo
ON
• The servo for all the servo amplifiers connected to the Simple Motion module is turned
ON or OFF.
Y10
Y11
Y12
Y13
Y14
Y15
Y16
Y17
Y18
Y19
Y1A
Y1B
Y1C
Y1D
Y1E
Y1F
Axis 1
Axis 2
Axis 3
Axis 4
Axis 5
Axis 6
Axis 7
Axis 8
Axis 9
Axis 10
Axis 11
Axis 12
Axis 13
Axis 14
Axis 15
Axis 16
Positioning
start
OFF: Positioning start not
requested
ON: Positioning
start
requested
• Home position return operation or positioning operation is started.
• The positioning start signal is valid at the rising edge, and the operation is started.
• When this signal turns ON during BUSY, the warning "Start during operation" (warning
code: 0900H) will occur.
Summary of Contents for RD77MS16
Page 1: ...MELSEC iQ R Simple Motion Module User s Manual Application RD77MS2 RD77MS4 RD77MS8 RD77MS16 ...
Page 2: ......
Page 316: ...314 9 COMMON FUNCTIONS 9 4 External Input Signal Select Function Program example ...
Page 317: ...9 COMMON FUNCTIONS 9 4 External Input Signal Select Function 315 9 ...
Page 575: ...13 PROGRAMMING 13 4 Positioning Program Examples 573 13 Error reset program Axis stop program ...
Page 643: ......