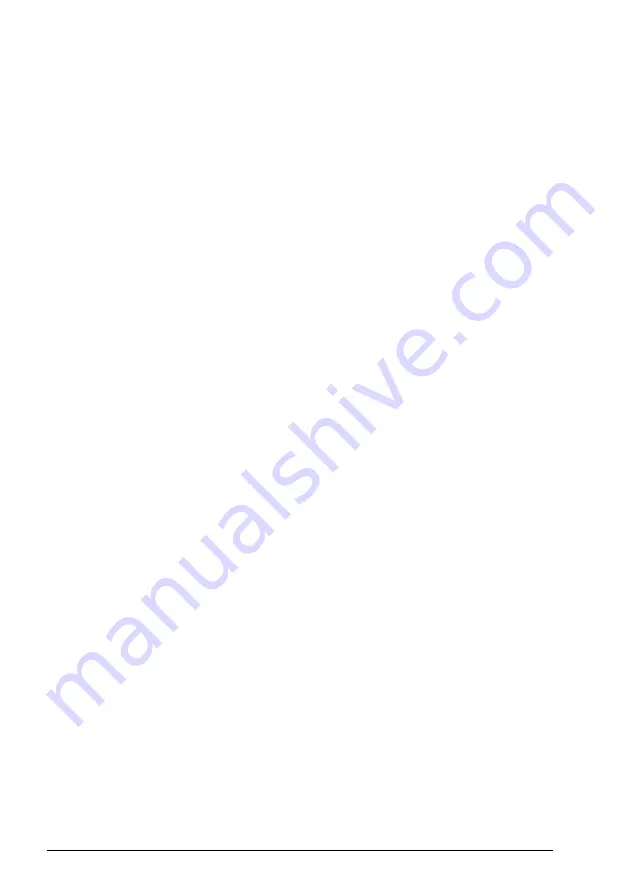
478 Verification and validation
3. Check from the safety PLC project that variable SLS scaling is set correctly.
Octet 3 for enabling the scaling:
•
bit 6 negative scaling
•
bit 7 positive scaling
Octets 4 and 5 for the variable SLS speed scaling value.
Test the variable SLS function as used in the application. Pay attention to the testing
of the relevant fault situations for the application, for example the tripping fault in the
drive, safety encoder fault, etc:
4. Start the drive with suitable speed reference. Activate the variable SLS function
via the safety bus.
5. Make sure that the variable SLS function limits the motor speed to the required
variable SLS limit by the application. Try to give a speed reference higher than the
limit. Make sure that the drive does not follow speed references higher that the
scaled SLS limit.
indicates safe speed when motor
speed is within the limits.
7. Scale down the variable SLS limit by various test scaling values.
8. Make sure that the deceleration ramp operates as required and no tripping fault
occurs during the deceleration and that the reference SLS4 limits (100% scaling)
are set according to the application requirements.
indicates safe speed when motor
speed is within the scaled variable SLS limits.
10. Deactivate variable SLS function. Make sure that the variable SLS indication goes
off, and the drive runs the motor according to the given user reference.
Note:
If the variable SLS function can be activated at a higher speed than the
variable SLS limit, validate the correct operation as follows:
11. Activate the variable SLS function at a motor speed above the variable SLS limit
(or scale down the variable SLS limit).
12. Activate the coast stop of the drive.
13. Make sure that the FSO module reacts according to your application
requirements, for example, it trips the drive with the STO.
14. Make sure that the following events occur only after the motor is in safe state:
•
SLS indication (
) goes on, if it is configured.
•
Acknowledgement of the stopping function (SSE or STO) is possible in case a
stopping function was triggered earlier. See step
Summary of Contents for FSO-21
Page 1: ... OPTIONS FOR ABB DRIVES FSO 21 safety functions module User s manual ...
Page 4: ......
Page 16: ...16 Safety instructions ...
Page 34: ...34 Safety information and considerations ...
Page 52: ...52 Overview ...
Page 236: ...236 PROFIsafe ...
Page 265: ...PROFIsafe 265 2 Select your CPU from the list 3 Install the FENA 21 GSDML file ...
Page 275: ...PROFIsafe 275 20 In ABB_Drive FB add blocks DPRD_DAT and DPWR_DAT 21 Insert values to blocks ...
Page 282: ...282 PROFIsafe 5 To read the diagnostic messages select the I O Device Diagnostics tab ...
Page 286: ...286 PROFIsafe ...
Page 304: ...304 Installation ...
Page 400: ...400 Configuration ...
Page 488: ...488 Verification and validation ...
Page 506: ...506 Fault tracing ...
Page 514: ...514 Maintenance ...
Page 536: ...536 Technical data ...