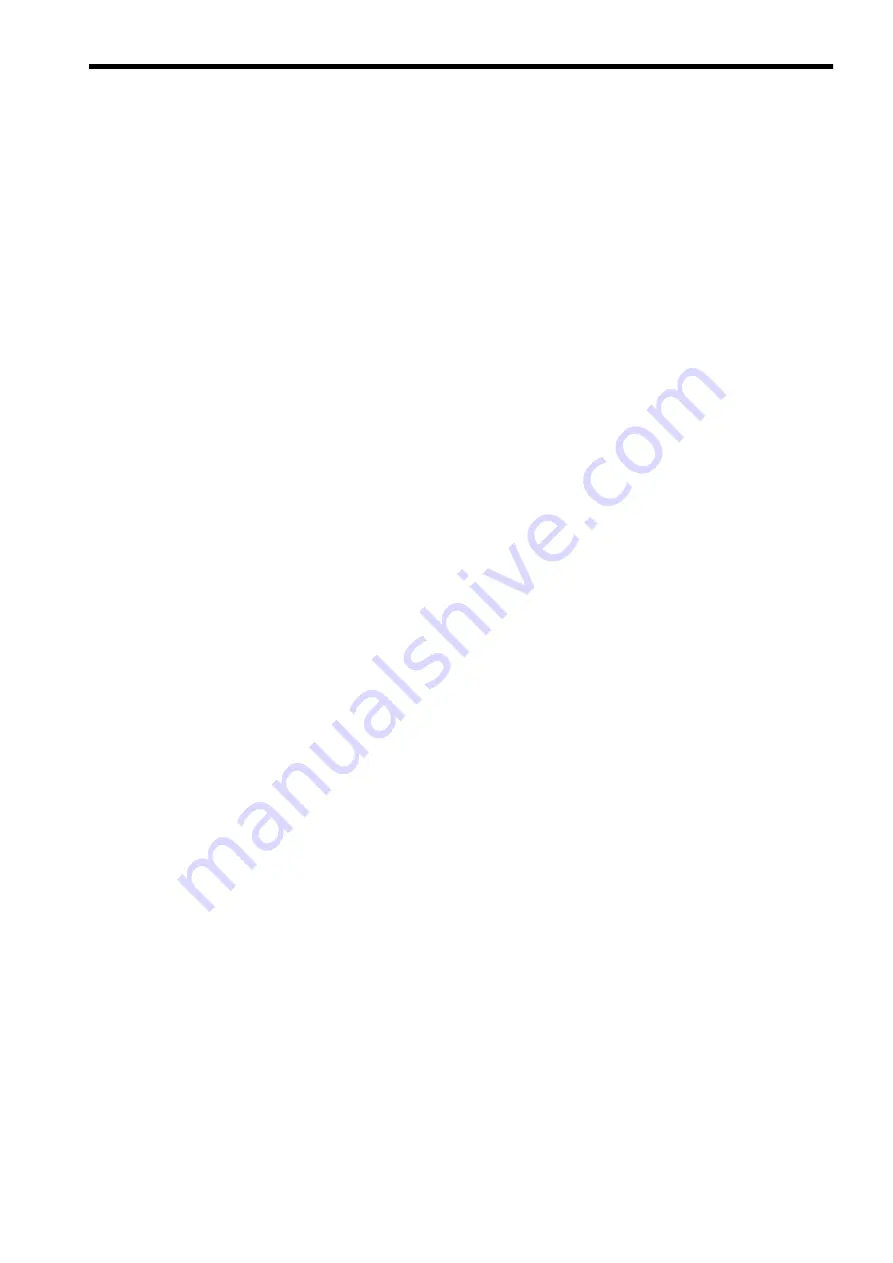
14.2 Servo control
14-43
14.2.6 Torque reference notch filter
To suppress stationary vibrations such as sympathetic axis vibration, created by Servo axis,
of 400 Hz or higher, use a torque reference notch filter. The following shows parameters
relating to the torque reference notch filter. For further information on the torque reference
notch filter, refer to a separate instruction manual.
• MD3358 digit 0 (Pn408 digit 0) SWITCH_NOTCH_FILTERS (For each axis)
Meaning:
1st-stage notch filter selection
Setting value: 0 --- Disabled
1 --- Enabled
• MD3358 digit 1 (Pn408 digit 1) SWITCH_NOTCH_FILTERS (For each axis)
Meaning:
2nd-stage notch filter selection
Setting value: 0 --- Disabled
1 --- Enabled
• MD3359 (Pn409) FREQUENCY_NOTCH_FILTERS_1 (For each axis)
Meaning:
1st-stage notch filter frequency
Setting value: [Hz]
• MD3360 (Pn40A) Q_VALUE_NOTCH_FILTERS_1 (For each axis)
Meaning:
1st-stage notch filter Q-value
Setting value: [0.01 times]
• MD3361 (Pn40B) FREQUENCY_NOTCH_FILTERS_2 (For each axis)
Meaning:
2nd-stage notch filter frequency
Setting value: [Hz]
• MD3362 (Pn40C) Q_VALUE_NOTCH_FILTERS_2 (For each axis)
Meaning:
2nd-stage notch filter Q-value
Setting value: [0.01 times]
Torque filters (3-stage) and notch filters (2-stage) can be used in any combinations. You can
select torque filters for up to 3 stages. (Notice that this specification differs from that of
J300/J100.)
Содержание CNC Series
Страница 1: ...Maintenance Manual Serviceman Handbook MANUAL No NCSIE SP02 19 Yaskawa Siemens CNC Series...
Страница 26: ...Part 1 Hardware...
Страница 38: ...System Configuration 1 2 3 Spindle motor designations 1 12...
Страница 58: ...Installing the control panels 2 3 5 Installing lightning surge absorbers 2 20...
Страница 62: ...Installing the motors 3 4...
Страница 84: ...Connection method 4 3 2 Setting the rotary switches on the inverters and servo units 4 22...
Страница 96: ...Part 2 Software...
Страница 102: ...Software configuration 6 6...
Страница 103: ...7 1 Chapter 7 Backup 7 1 How to archive 7 2 7 2 Network settings 7 7 7 2 1 YS 840DI settings 7 7 7 2 2 PC settings 7 14...
Страница 105: ...7 1 How to archive 7 3 3 Select the Workpieces folder 4 Click on Archive File which is one of the right side keys...
Страница 113: ...7 2 Network settings 7 11 8 Click on the radio button to the left of Specify an IP address...
Страница 121: ...7 2 Network settings 7 19...
Страница 122: ...Part 3 PLC...
Страница 154: ...Part 4 Setting up and maintenance...
Страница 160: ...Overview of System 10 1 2 Basic operation 10 6...
Страница 204: ...How to use Digital Operation 12 2 9 Setting the password setting for write prohibit 12 32...
Страница 327: ...Error and Troubleshooting 15 4...
Страница 328: ...15 1 Errors without Alarm Display and Troubleshooting 15 5...
Страница 329: ...Error and Troubleshooting 15 6...
Страница 343: ...Maintenance and Check 16 3 3 Setting up Initializing Absolute encoder 16 14...