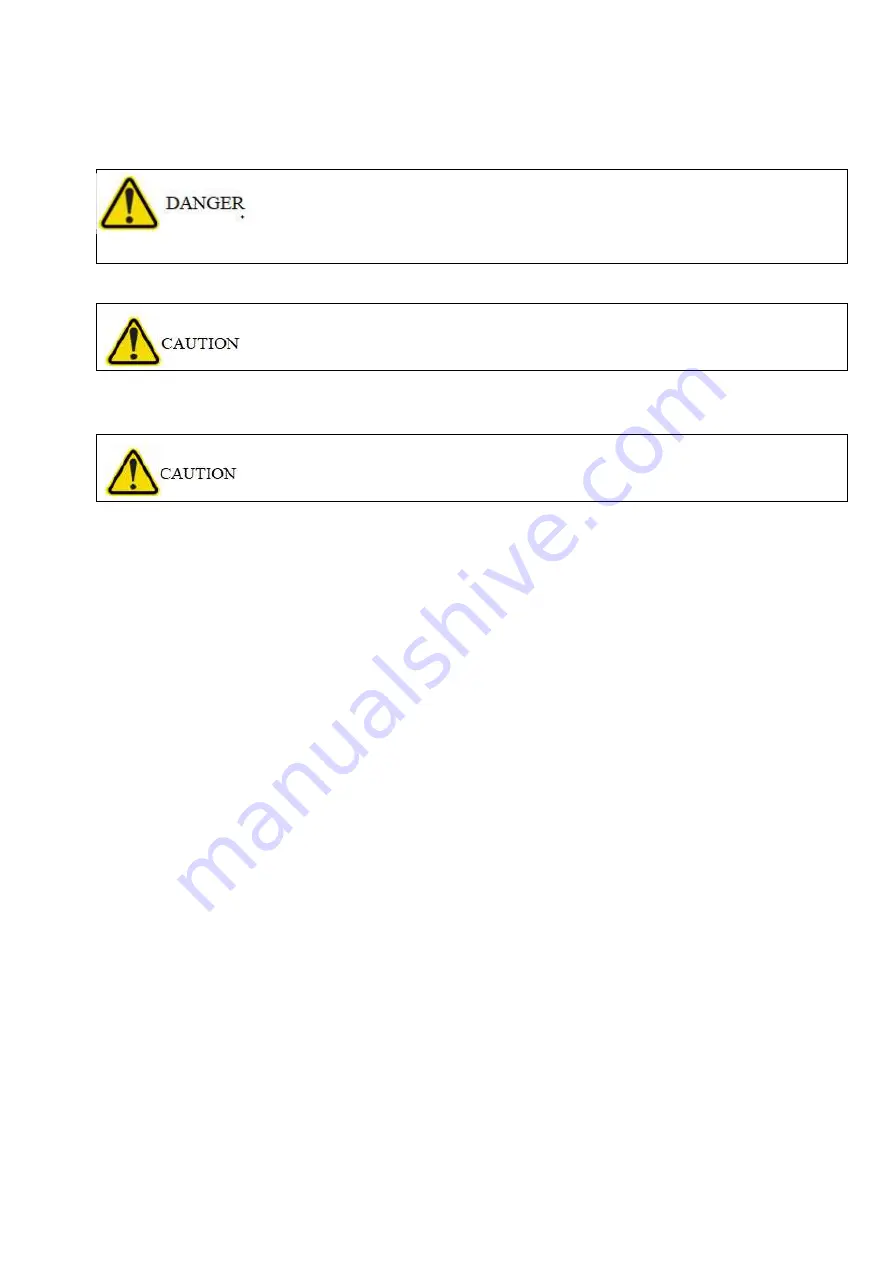
191
6.6 Other functions
●Before connecting to peripheral devices, turn off the power and wait for
20 minutes or more until the charge LED turns off, and check the
residual voltage by meter. Otherwise, an electric shock may occur.
●Please use designated products for peripheral devices to avoid fire or
malfunction.
6.6.1 Selection of regenerative resistor
●It’s forbidden to use regenerative resistor and servo drive except for
below specified combinations, otherwise, a fire disaster may occur.
If the torque direction of the motor is opposite to the rotation direction, the motor will switch to
a power generator, The energy will be transferred from the load to the inside of drive, which
will cause voltage excess of P-N terminal. To avoid module and capacitor damage, the
regenerative protection function should control the voltage within 370V/740V. The
regenerative protection function is mainly composed of IGBT and resistor. The regenerative
energy is consumed by the resistor, and its resistance need to be checked when using it. The
regenerative protection function is controlled by the regenerative transistor and you should
check if the regenerative resistor is normal before operation. If the regenerative transistor is
damaged, stop the motor urgently to avoid continuous energy regeneration which will damage
the drive.
The drive has a built-in regenerative resistor for users .If the regenerative energy is too large,
it is not recommended to use the built-in regenerative resistor, use an external regenerative
resistor instead to avoid overheating or damage the drive due to failing to consume energy.
User can use the external terminals of P,D,C to connect either external regenerative resistor
or built-in regenerative resistor. When built-in regenerative resistor is used, make sure P-D
terminals is short-circuited. When external regenerative resistor is used, make P-D open and
regenerative resistor is connected to P-C terminals.
The following tables shows the specification of built-in regenerative resistor for Shihlin servo
drive.
Содержание SDP Series
Страница 33: ...20 400V series DC 24V Power supply Note terminal P N cannot be grounded ...
Страница 42: ...29 2 CN1 connector male Front view Side view Rear view CN1 wiring terminal on the back of CN1 1 26 50 25 ...
Страница 45: ...32 4 The last step is to fasten the screw of housing ...
Страница 203: ...190 It is recommended that the user performs torque position mode switching after motor is stopped completely ...
Страница 385: ...372 ...
Страница 405: ...392 ...
Страница 499: ...486 SME L040 SME L075 SME L100 SME L150 ...
Страница 500: ...487 SME L200 SME L300 SME M100 SME M150 ...
Страница 509: ...496 When the load reaches 300 the operation time is 5 51 seconds ...
Страница 541: ...528 Middle inertia power cable Middle inertia 2KW 3KW 400V High inertia power cable 1 8KW 2 9KW 4 4KW 5 5KW 7 5KW ...
Страница 555: ...542 14 5 Manual version and revision history Manual version V1 00 Release month July 2022 ...