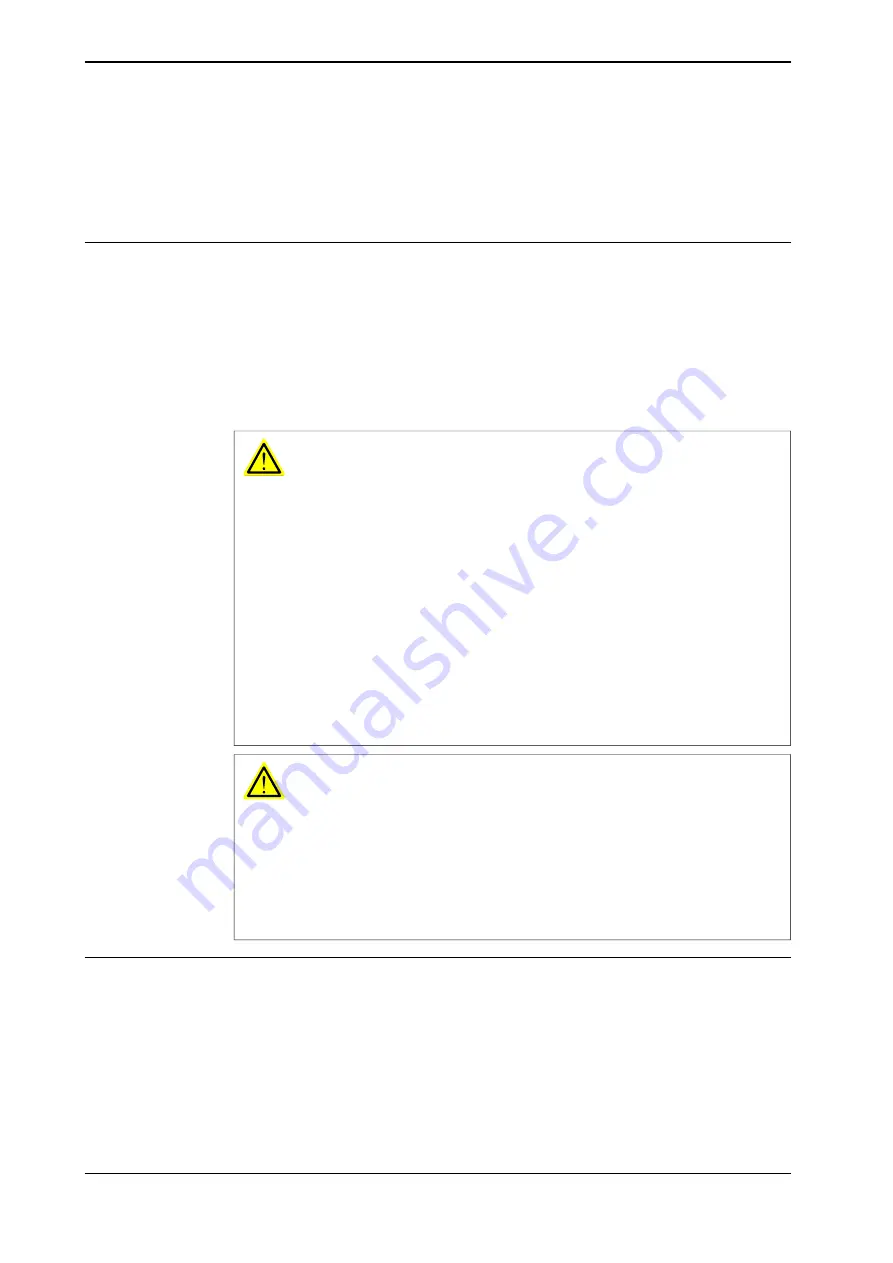
3.4 Remote control of operating mode
3.4.1 Overview
Introduction
The functionality
remote control of operating mode
enables the support for
controlling the operating mode from a PLC via system inputs. All mode changes
are approved by the safety controller.
It can for example be used where there is a PLC connected to several robots in a
cell. When service has been completed and production is started, all robots in the
cell can be changed to automatic mode by the PLC.
For system inputs and outputs, see
System inputs and outputs on page 71
WARNING
Note that using remote control of operating mode will be contrary to the
regulations in the safety standard ISO 10218-1 chapter
5.3.5 Single point of
control
with following text:
"The robot control system shall be designed and constructed so that when the
robot is placed under local pendant control or other teaching device control,
initiation of robot motion or change of local control selection from any other
source shall be prevented."
Thus it is absolutely necessary to use other means of safety to maintain the
requirements of the standard and the machinery directive and also to make a
risk assessment of the completed cell. Such additional arrangements and risk
assessment is the responsibility of the system integrator and the system must
not be put into service until these actions have been completed.
DANGER
A recommendation is to control the remote control enable signal,
RemoteOpModeEnable
, from a lockable switch outside the cell together with the
auto stop signal.
A service engineer entering the cell can then by locking the switch be ensured
of single point of control, and mode changes from the PLC will only be allowed
when the cell door is closed.
Prerequisites
The following options are needed for remote control of operating mode:
•
[996-1]
Safety module (DSQC1015)
•
[735-7]
Keyless Mode Selector, 3 modes
or [735-8]
Keyless Mode Selector, 2 modes
•
The robot system must be installed with the base RobotWare option
Auto
Acknowledge Input
enabled in Installation Manager.
68
Application manual - Functional safety and SafeMove2
3HAC052610-001 Revision: P
© Copyright 2016-2020 ABB. All rights reserved.
3 Installation
3.4.1 Overview
Содержание SafeMove2
Страница 1: ...ROBOTICS Application manual Functional safety and SafeMove2 ...
Страница 2: ...Trace back information Workspace 20C version a3 Checked in 2020 09 14 Skribenta version 5 3 075 ...
Страница 8: ...This page is intentionally left blank ...
Страница 16: ...This page is intentionally left blank ...
Страница 34: ...This page is intentionally left blank ...
Страница 56: ...This page is intentionally left blank ...
Страница 72: ...This page is intentionally left blank ...
Страница 112: ...This page is intentionally left blank ...
Страница 194: ...This page is intentionally left blank ...
Страница 196: ...This page is intentionally left blank ...
Страница 234: ...This page is intentionally left blank ...
Страница 237: ......