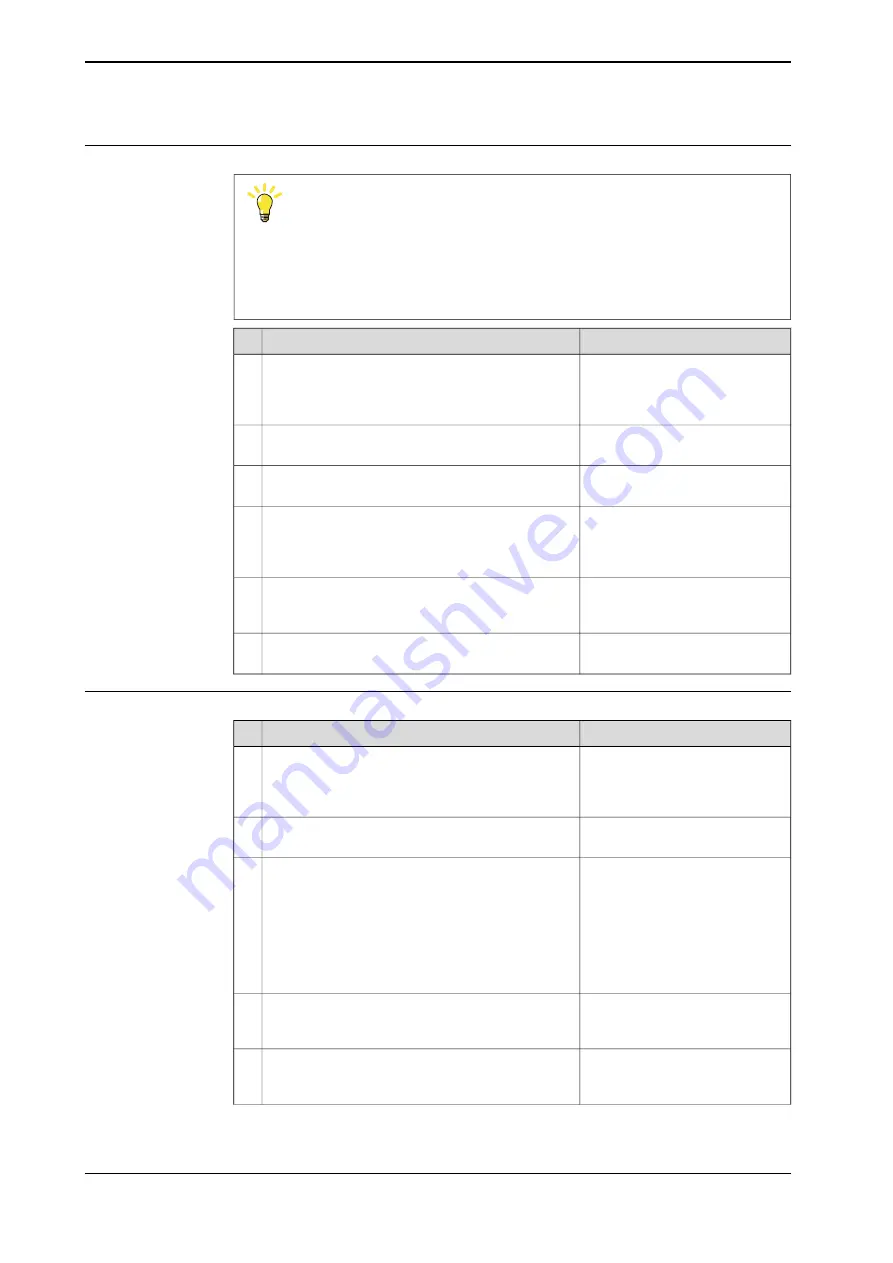
Axis Speed Supervision validation
Tip
To determine which
speeddata
settings to use for validation, use an
MoveAbsJ
instruction to move relevant axis and check the axis speed in signal analyzer in
RobotStudio. Change the speed of the
MoveAbsJ
instruction until the desired
axis speed is achieved.
Expected result
Action
If not permanently active, activate the activation in-
put signal for Axis Speed Supervision. Deactivate
all other supervision functions that are signal activ-
ated.
1
If applicable, make sure the TCP is inside the Axis
Speed Supervision zone or all axes inside the range.
2
Status signal is 1.
If used, verify that the corresponding function active
status signal is set.
3
No triggered function.
Create a RAPID program with a
MoveAbsJ
instruc-
tion moving the first configured axis with a speed
slower than the configured Max Speed for that axis.
Run the program in auto or manual full speed mode.
4
Axis Speed Supervision will trig-
ger.
Change the program so that the axis is moved with
a speed higher than the configured Max Speed. Run
the program in auto or manual full speed mode.
5
Repeat this for all axes configured for Axis Speed
Supervision.
6
Stand Still Supervision validation
Expected result
Action
If not permanently active, activate the activation in-
put signal for the Stand Still Supervision set you
want to validate. Deactivate all other supervision
functions that are signal activated.
1
Status signal is 1.
If used, verify that the corresponding function active
status signal is set.
2
Create a RAPID program with
MoveJ
instructions
that move one axis at a time at maximum allowed
speed. Let the program wait for user input between
each move instruction to let you validate each move
instruction.
3
If there are additional axes in the system, include
instructions that move these axes, one at a time,
as well.
Stand Still Supervision will trigger.
Run the program in auto or manual full speed mode
and verify that Stand Still Supervision triggers for
every move instruction.
4
If the Stand Still Supervision is configured to stop
at violation, determine that the movement until the
robot is stopped again is within a tolerable limit.
5
Continues on next page
182
Application manual - Functional safety and SafeMove2
3HAC052610-001 Revision: P
© Copyright 2016-2020 ABB. All rights reserved.
6 Configuring SafeMove
6.20 Validate the configuration
Continued
Содержание SafeMove2
Страница 1: ...ROBOTICS Application manual Functional safety and SafeMove2 ...
Страница 2: ...Trace back information Workspace 20C version a3 Checked in 2020 09 14 Skribenta version 5 3 075 ...
Страница 8: ...This page is intentionally left blank ...
Страница 16: ...This page is intentionally left blank ...
Страница 34: ...This page is intentionally left blank ...
Страница 56: ...This page is intentionally left blank ...
Страница 72: ...This page is intentionally left blank ...
Страница 112: ...This page is intentionally left blank ...
Страница 194: ...This page is intentionally left blank ...
Страница 196: ...This page is intentionally left blank ...
Страница 234: ...This page is intentionally left blank ...
Страница 237: ......