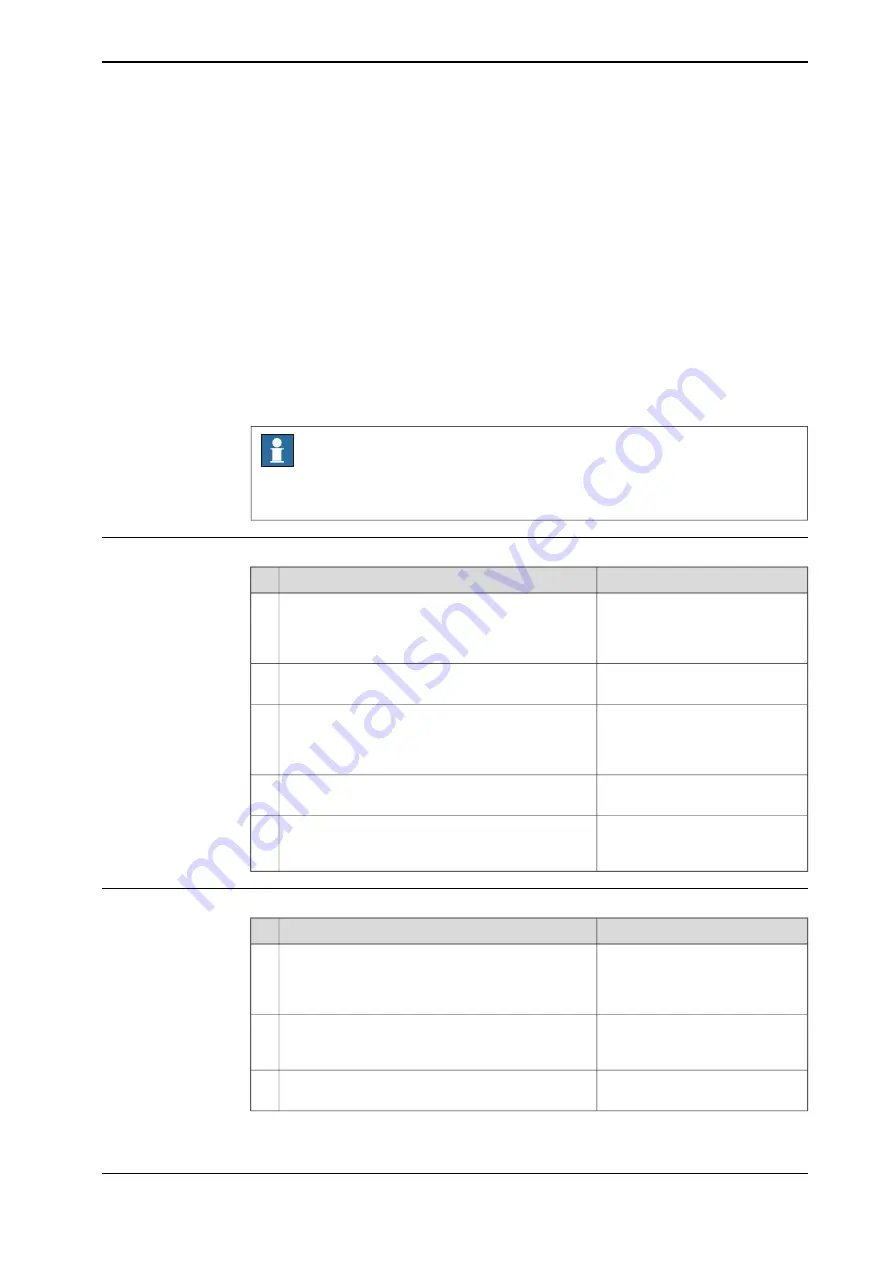
Validate the TCP position
For each tool, validate the TCP position if possible. It is possible to validate the
TCP position with the following zone supervision functions:
•
If a tool does not have speed supervision points surrounding the TCP, it is
possible to validate the TCP position using Tool Speed Supervision. See
Tool Speed Supervision validation on page 180
.
•
Tool Orientation Supervision can be used to validate the TCP position. See
Validate zone using Tool Orientation Supervision on page 177
•
Contact Application Tolerance can be used to validate the TCP position. See
Validate zone using Contact Application Tolerance on page 178
If none of these criteria is met for a tool, the TCP position cannot be validated for
that tool, but then it is not necessary to validate it.
Note
The TCP for the SafeMove tool must correspond with the TCP of the active tool
for jogging and RAPID instructions.
Tool Position Supervision validation
Expected result
Action
If not permanently active, activate the activation in-
put signal for the Tool Position Supervision set you
want to validate. Deactivate all other supervision
functions that are signal activated.
1
Status signal is 1.
If used, verify that the corresponding function active
status signal is set.
2
Tool Position Supervision will
trigger.
Move the robot so that the configured geometry
surrounding the tool crosses the border of the con-
figured zone. Verify that Tool Position Supervision
triggers when the border is crossed.
3
Repeat this for at least two points on each side of
the zone, including top and bottom.
4
If the system is equipped with a track motion, check
that the tool zone border is in correct position for
different positions of the track motion.
5
Tool Orientation Supervision validation
Expected result
Action
If not permanently active, activate the activation in-
put signal for the Tool Orientation Supervision set
you want to validate. Deactivate all other supervision
functions that are signal activated.
1
If applicable, make sure the TCP is inside the Tool
Orientation Supervision zone or all axes inside the
range.
2
Status signal is 1.
If used, verify that the corresponding function active
status signal is set.
3
Continues on next page
Application manual - Functional safety and SafeMove2
179
3HAC052610-001 Revision: P
© Copyright 2016-2020 ABB. All rights reserved.
6 Configuring SafeMove
6.20 Validate the configuration
Continued
Содержание SafeMove2
Страница 1: ...ROBOTICS Application manual Functional safety and SafeMove2 ...
Страница 2: ...Trace back information Workspace 20C version a3 Checked in 2020 09 14 Skribenta version 5 3 075 ...
Страница 8: ...This page is intentionally left blank ...
Страница 16: ...This page is intentionally left blank ...
Страница 34: ...This page is intentionally left blank ...
Страница 56: ...This page is intentionally left blank ...
Страница 72: ...This page is intentionally left blank ...
Страница 112: ...This page is intentionally left blank ...
Страница 194: ...This page is intentionally left blank ...
Страница 196: ...This page is intentionally left blank ...
Страница 234: ...This page is intentionally left blank ...
Страница 237: ......