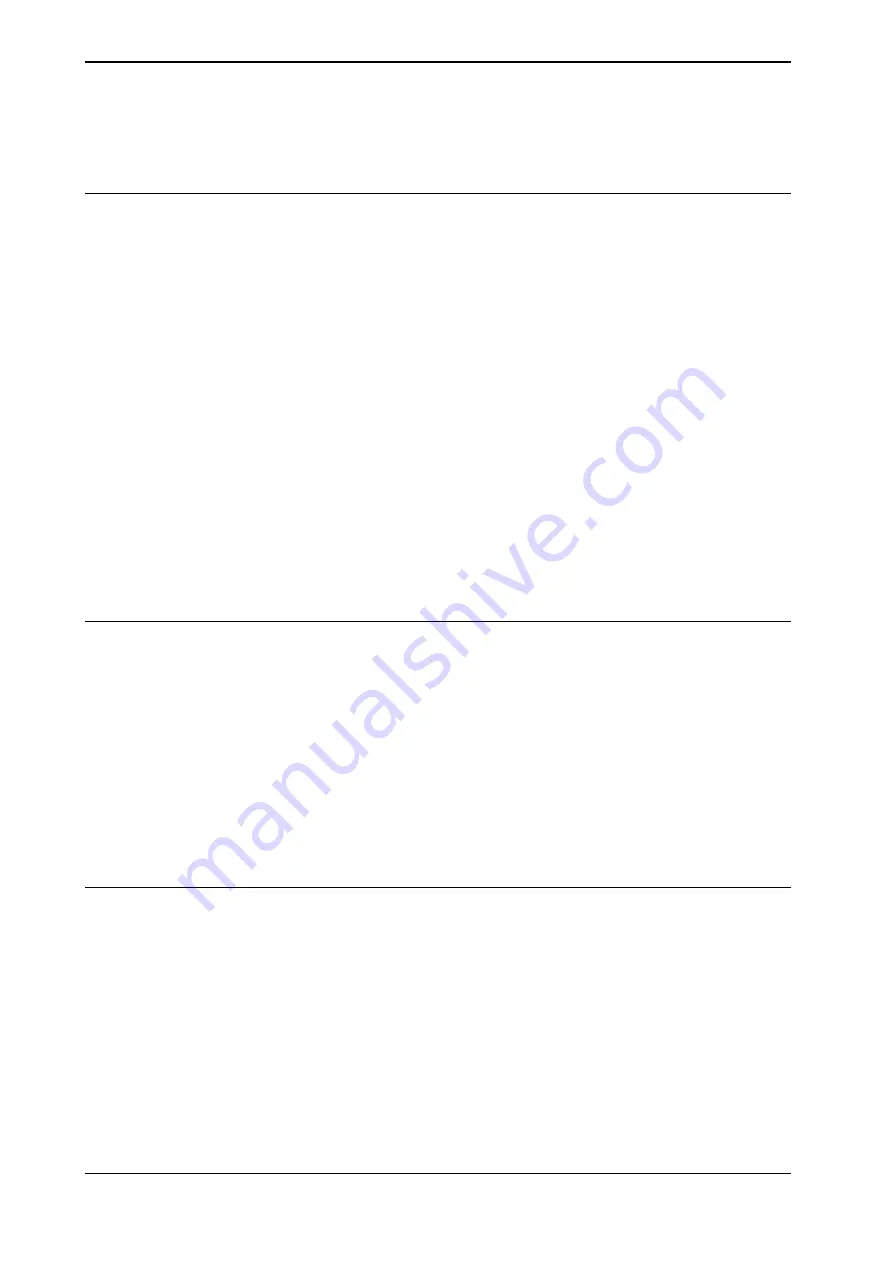
10.5.2 Use cases
Use case 1: Import of nominal safety related geometry information
If the planning and geometry layout is created in a tool other than RobotStudio and
Visual SafeMove, the file can be used to transfer the safety-related geometry
information to RobotStudio and Visual SafeMove.
The safety configuration must be completed in Visual SafeMove by adding
non-geometry related safety configuration, for example brake check and activation
signals, before writing it to a real controller on the shop floor.
Procedure:
1 Create the cell layout in the external planning tool.
2 Create the safety geometry in the external planning tool, for example safety
zones, tool encapsulation, and speed supervision points.
3 Export the safety related geometries from the external planning tool to a
SafeMove geometry configuration file.
4 Import the SafeMove geometry configuration file into Visual SafeMove in
RobotStudio.
5 Complete the safety configuration by adding remaining non-geometry related
safety configurations, for example brake check and activation signals.
6 Load the safety configuration to the safety controller.
Use case 2: Import of calibrated safety related geometry information
This use case is very similar to use case 1, the difference being that the
safety-related geometries are adjusted with respect to measurement data of the
robot cell.
Steps 3A to 3C are added to the procedure in use case 1:
A Import the SafeMove geometry configuration file into a second tool that can
adjust zones based on measurement data from the real robot cell.
B Adjust the zones relative to the offsets of the corresponding real objects in
the robot cell, for example robot base frame, fixtures, tip dressers, material
supply units, etc.
C Export the adjusted zones to a new SafeMove geometry configuration file.
Use case 3: Export of real safety related geometry information
In this use case, the actual zones and related geometry information of the real
controller are exported to a SafeMove geometry configuration file using Visual
SafeMove in RobotStudio. The purpose may be to update the nominal robot cell
in the external planning tool.
Procedure:
1 Connect RobotStudio to the robot controller.
2 Use Visual SafeMove to read the safety configuration from the robot controller.
3 Export the configuration to a SafeMove geometry configuration file.
Continues on next page
214
Application manual - Functional safety and SafeMove2
3HAC052610-001 Revision: P
© Copyright 2016-2020 ABB. All rights reserved.
10 Reference information
10.5.2 Use cases
Содержание SafeMove2
Страница 1: ...ROBOTICS Application manual Functional safety and SafeMove2 ...
Страница 2: ...Trace back information Workspace 20C version a3 Checked in 2020 09 14 Skribenta version 5 3 075 ...
Страница 8: ...This page is intentionally left blank ...
Страница 16: ...This page is intentionally left blank ...
Страница 34: ...This page is intentionally left blank ...
Страница 56: ...This page is intentionally left blank ...
Страница 72: ...This page is intentionally left blank ...
Страница 112: ...This page is intentionally left blank ...
Страница 194: ...This page is intentionally left blank ...
Страница 196: ...This page is intentionally left blank ...
Страница 234: ...This page is intentionally left blank ...
Страница 237: ......