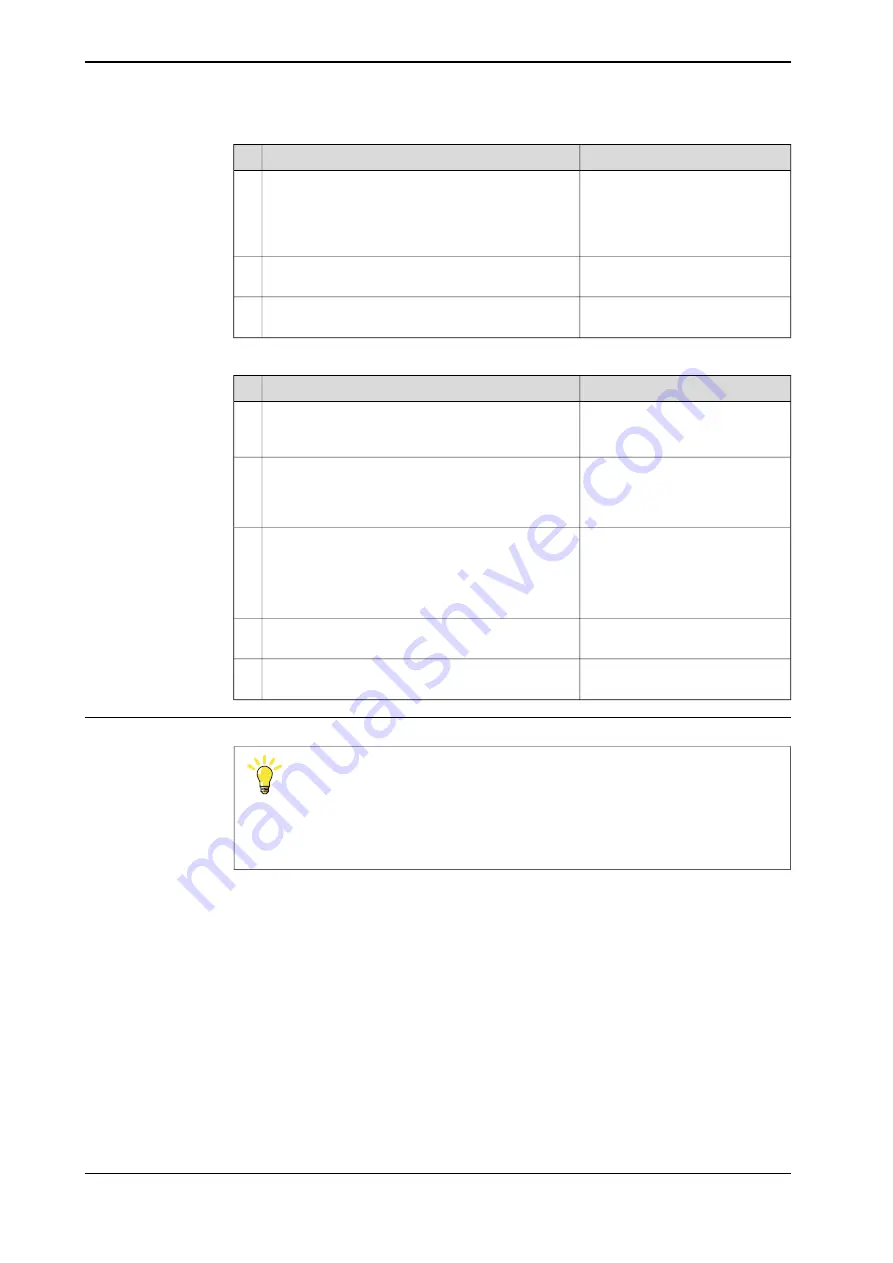
Expected result
Action
Tool Speed Supervision will trig-
ger when the tested axis reach its
range limit.
Run a RAPID program that moves the tool at a
speed that is allowed outside the range but not al-
lowed inside the range. At the same time the pro-
gram shall test one axis at a time by moving it from
outside the range to inside the range.
2
Repeat this for both lower and upper limit of the
axis range.
3
Repeat this for all axes configured in the range, in-
cluding additional axes.
4
Validate range using Contact Application Tolerance
Expected result
Action
Make sure that Soft Servo is active and set the
stiffness to a value that is allowed outside the range
but not allowed inside the range.
1
If not permanently active, activate the activation in-
put signal for Contact Application Tolerance for the
range. Deactivate all other supervision functions
that are signal activated.
2
Control Error Supervision will
trigger when the tested axis reach
its range limit.
Run a RAPID program moving the TCP with maxim-
um speed allowed (e.g.
vmax
).
At the same time the program shall test one axis at
a time by moving it from outside the range to inside
the range.
3
Repeat this for both lower and upper limit of the
axis range.
4
Repeat this for all axes configured in the range, in-
cluding additional axes.
5
Validate zone limits
Tip
To validate that the zones have enough margins, let the robot move with maximum
allowed speed when reaching the zone limits. Verify that the limits are set with
enough margin with respect to the breaking distance.
Validate the zone limits for all configured zones. It is enough to validate the limits
of each zone for one function and one tool, since the zone limits are treated equally
for all functions and tools in the zone. Perform the zone limits validation using one
of the following functions (preferably Tool Position Supervision).
Validate zone using Tool Position Supervision
If a zone has a Tool Position Supervision function, perform the validation for that
function. See
Tool Position Supervision validation on page 179
Continues on next page
176
Application manual - Functional safety and SafeMove2
3HAC052610-001 Revision: P
© Copyright 2016-2020 ABB. All rights reserved.
6 Configuring SafeMove
6.20 Validate the configuration
Continued
Содержание SafeMove2
Страница 1: ...ROBOTICS Application manual Functional safety and SafeMove2 ...
Страница 2: ...Trace back information Workspace 20C version a3 Checked in 2020 09 14 Skribenta version 5 3 075 ...
Страница 8: ...This page is intentionally left blank ...
Страница 16: ...This page is intentionally left blank ...
Страница 34: ...This page is intentionally left blank ...
Страница 56: ...This page is intentionally left blank ...
Страница 72: ...This page is intentionally left blank ...
Страница 112: ...This page is intentionally left blank ...
Страница 194: ...This page is intentionally left blank ...
Страница 196: ...This page is intentionally left blank ...
Страница 234: ...This page is intentionally left blank ...
Страница 237: ......