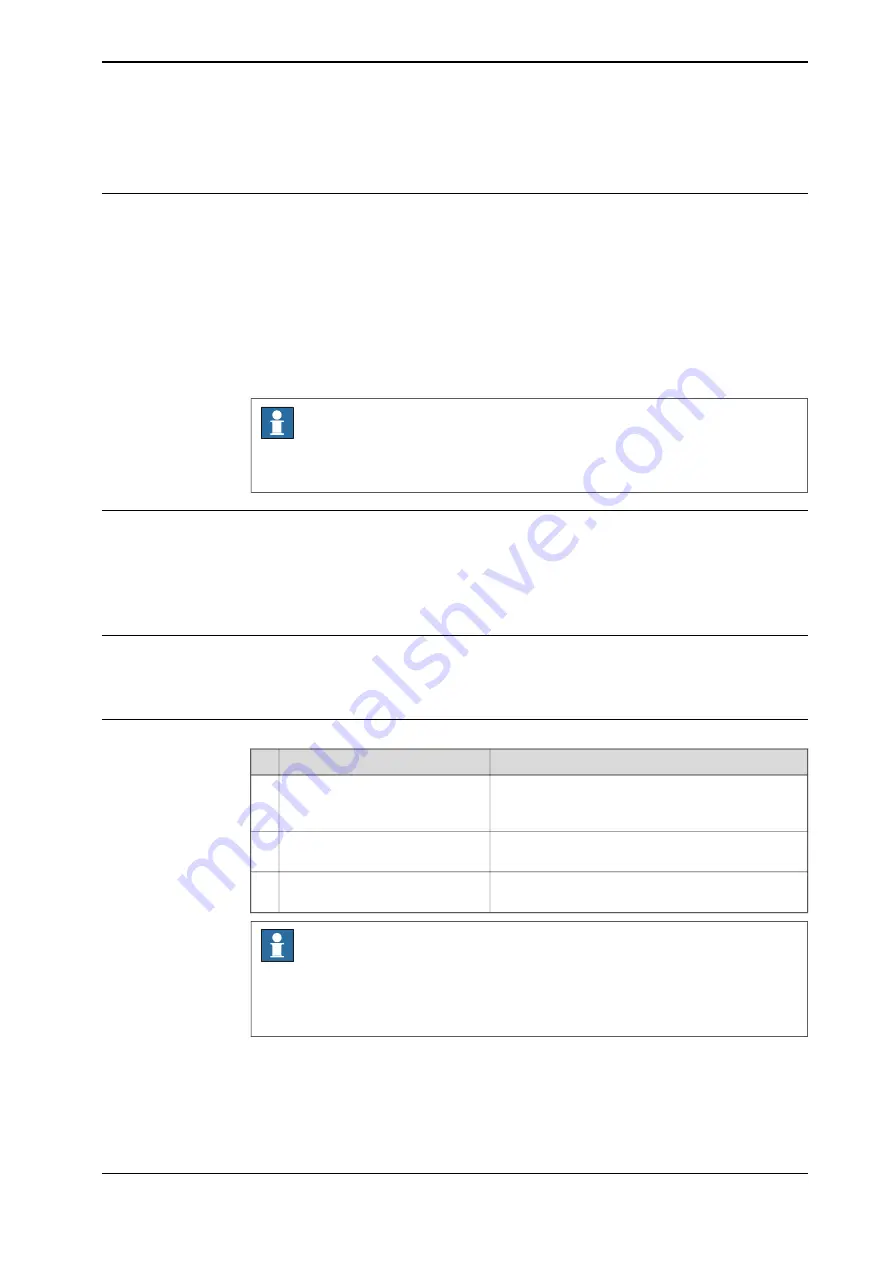
10.1.2 Hardware synchronization guidelines
Uniquely defined position
The robot position for the synchronization must be chosen so that the position of
the robot axes are unambiguously defined. One way to make sure the
synchronization position is well-defined for all axes is to use the instruction
MoveAbsJ
to move to the sync position. See
Technical reference manual - RAPID
Instructions, Functions and Data types
.
Note that the sync position should be allowed by all active functions. For example,
the robot must be inside the allowed zones for all active Tool Position Supervision
functions.
Note
Software synchronization is always available even if hardware synchronization
is configured.
Small sync switch surface
For hardware synchronization, the sync switch surface that the robot touches must
be small. The surface of the tool touching the sync switch must also be small. If
any robot axis moves one motor revolution, the robot must be out of reach for the
sync switch.
Always activate sync switch in the same way
For hardware synchronization, always use the same tool. The robot should always
touch the sync switch with the same point on the tool.
Performing a synchronization
Note
Action
This will make the controller responsive to the syn-
chronization input signal for 30 seconds.
Run a RAPID program with the
instruction
SafetyControllerSyncRequest
.
1
If an axis is in wrong position, the revolution coun-
ters are most likely incorrect.
Move the robot to a position close
to the sync switch.
2
If the approach is too fast, the accuracy of the robot
position may be too low.
Slowly press the sync switch from
the desired direction.
3
Note
If the RAPID instruction
SafetyControllerSyncRequest
is executed and no
sync signal is received within 30 seconds, the robot is stopped with an error
message and the safety controller becomes unsynchronized.
Application manual - Functional safety and SafeMove2
199
3HAC052610-001 Revision: P
© Copyright 2016-2020 ABB. All rights reserved.
10 Reference information
10.1.2 Hardware synchronization guidelines
Содержание SafeMove2
Страница 1: ...ROBOTICS Application manual Functional safety and SafeMove2 ...
Страница 2: ...Trace back information Workspace 20C version a3 Checked in 2020 09 14 Skribenta version 5 3 075 ...
Страница 8: ...This page is intentionally left blank ...
Страница 16: ...This page is intentionally left blank ...
Страница 34: ...This page is intentionally left blank ...
Страница 56: ...This page is intentionally left blank ...
Страница 72: ...This page is intentionally left blank ...
Страница 112: ...This page is intentionally left blank ...
Страница 194: ...This page is intentionally left blank ...
Страница 196: ...This page is intentionally left blank ...
Страница 234: ...This page is intentionally left blank ...
Страница 237: ......