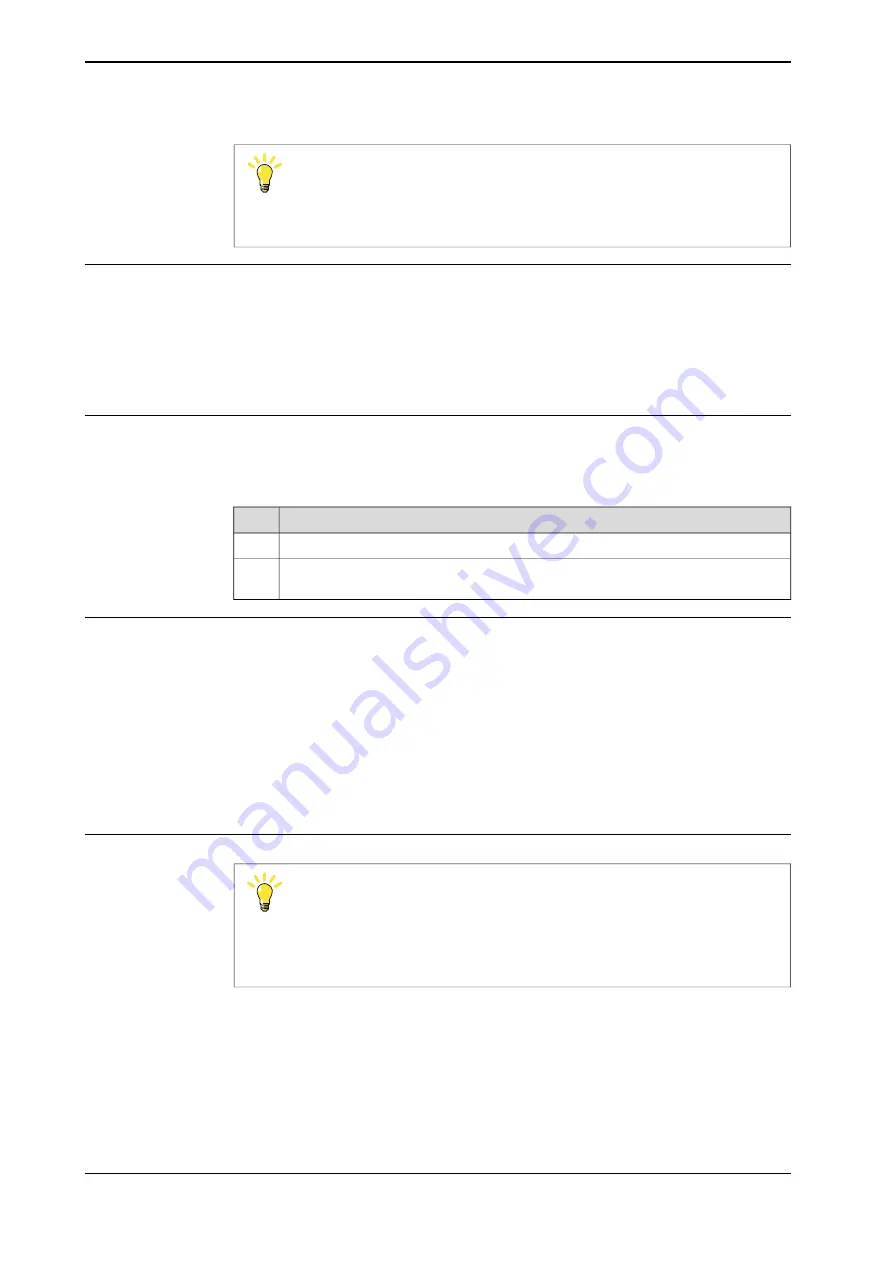
Tip
Use RAPID programs in order to perform testing faster and to be able to repeat
them.
ABB Safety Configuration Report
The validation of each function should be documented in the safety report by
signature of the validator.
The safety configuration report lists all parameters that are set for the installation.
The report also includes a visual representation of the installation, a floor plan.
This shows the robot and safety zones as seen from above.
Recovery after safety violation
The validation procedures test when the safety functions trigger. If the functions
Axis Position Supervision, Tool Position Supervision or Tool Orientation Supervision
triggers with a stop, recovery is achieved by performing the following:
Action
Select manual operating mode.
1
Press the enable device and jog the robot into a position in which the supervision
functions are not in violation.
2
Validate the safe fieldbus and signal configuration
Validate the safe fieldbus parameters, including I/O settings and signals used for
safety interlocking, by comparing the safety report with the configured values.
The user must visually verify that the data in the safety report is correct and that
it is the same as entered in the Visual SafeMove configuration GUI.
After controller restart the configuration is applied. The user must verify that no
safe fieldbus related event logs were generated, that the status of the connection
in the originator indicates "running", and that the connection to the intended adapter
device has been established.
Validate range limits
Tip
To validate that the ranges have enough margins, let the robot move with
maximum allowed speed when reaching the range limits. Verify that the limits
are set with enough margin with respect to the breaking distance.
Validate the range limits for all configured ranges. It is enough to validate the limits
of each range for one function, since the range limits are treated equally for all
Continues on next page
174
Application manual - Functional safety and SafeMove2
3HAC052610-001 Revision: P
© Copyright 2016-2020 ABB. All rights reserved.
6 Configuring SafeMove
6.20 Validate the configuration
Continued
Содержание SafeMove2
Страница 1: ...ROBOTICS Application manual Functional safety and SafeMove2 ...
Страница 2: ...Trace back information Workspace 20C version a3 Checked in 2020 09 14 Skribenta version 5 3 075 ...
Страница 8: ...This page is intentionally left blank ...
Страница 16: ...This page is intentionally left blank ...
Страница 34: ...This page is intentionally left blank ...
Страница 56: ...This page is intentionally left blank ...
Страница 72: ...This page is intentionally left blank ...
Страница 112: ...This page is intentionally left blank ...
Страница 194: ...This page is intentionally left blank ...
Страница 196: ...This page is intentionally left blank ...
Страница 234: ...This page is intentionally left blank ...
Страница 237: ......