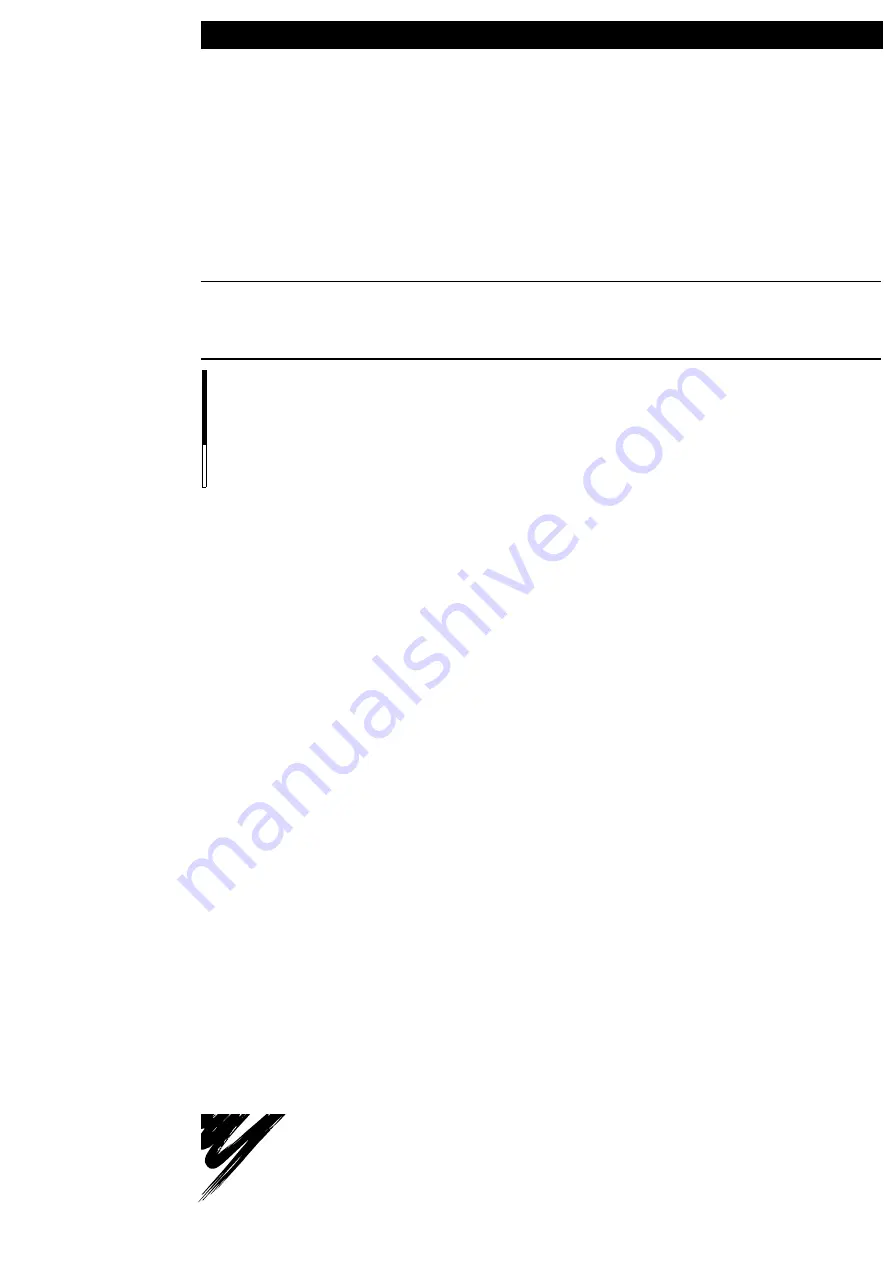
YASKAWA
YASKAWA
MANUAL NO. RE-CHO-A108
DX100
MAINTENANCE MANUAL
Upon receipt of the product and prior to initial operation, read these instructions thoroughly, and retain for
future reference.
MOTOMAN INSTRUCTIONS
MOTOMAN-
INSTRUCTIONS
DX100 INSTRUCTIONS
DX100 OPERATOR’S MANUAL
DX100 MAINTENANCE MANUAL
The DX100 operator’s manuals above correspond to specific usage.
Be sure to use the appropriate manual.
Part Number: 155492-1CD
Revision: 0