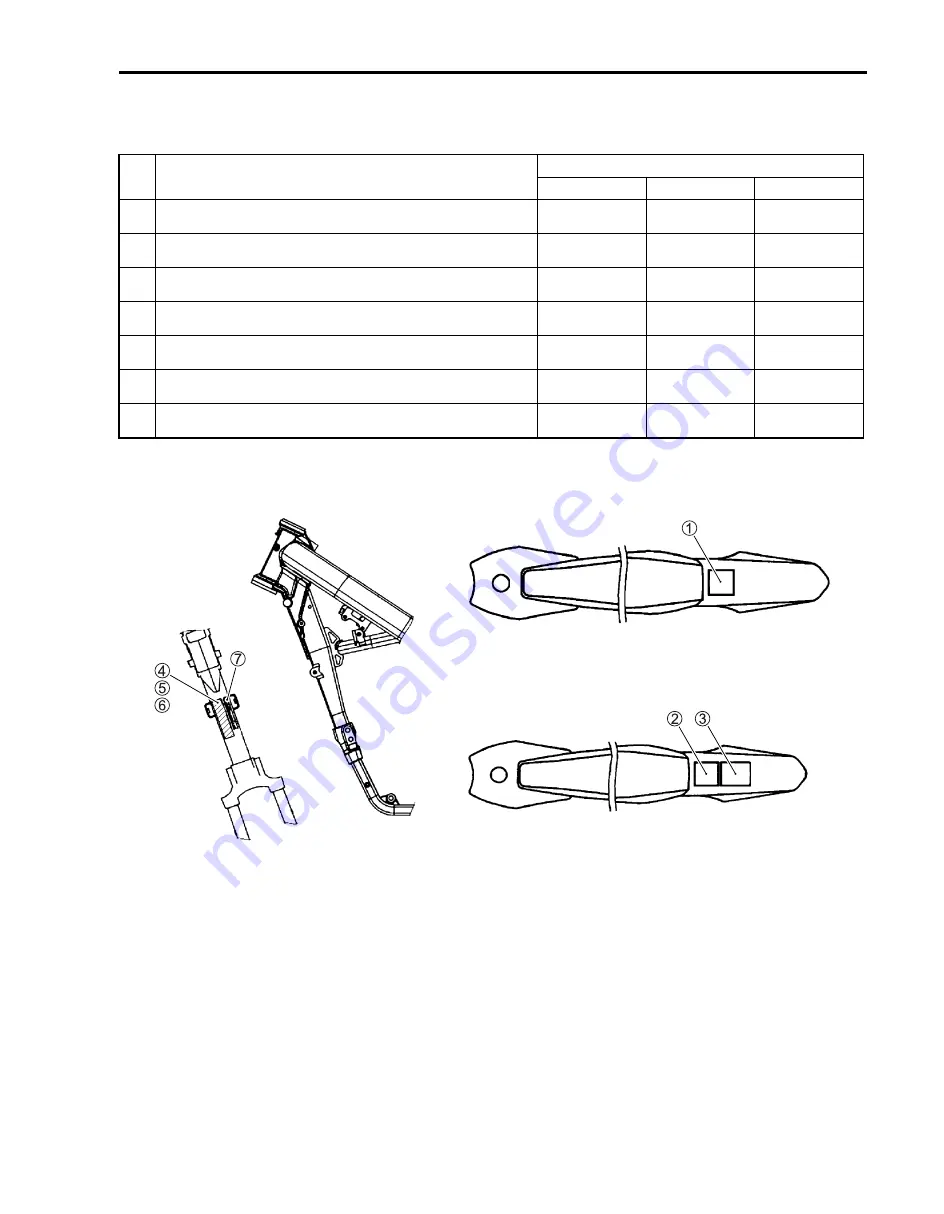
GENERAL INFORMATION 1-7
INFORMATION LABELS
E
: English
F
: French
A: Attached
No.
LABEL or PLATE NAME
APPLIED SPECIFICATION
E-03
E-19
E-28
1
General warning label
E
A
2
General warning label
E
A
A
3
General warning label
F
A
A
4
EC approval mark label
A
5
ICES Canada label
E
/
F
A
6
EPA plate
E
A
7
Manufacture label
E
A
A
A
For E-03
For E-19, 28