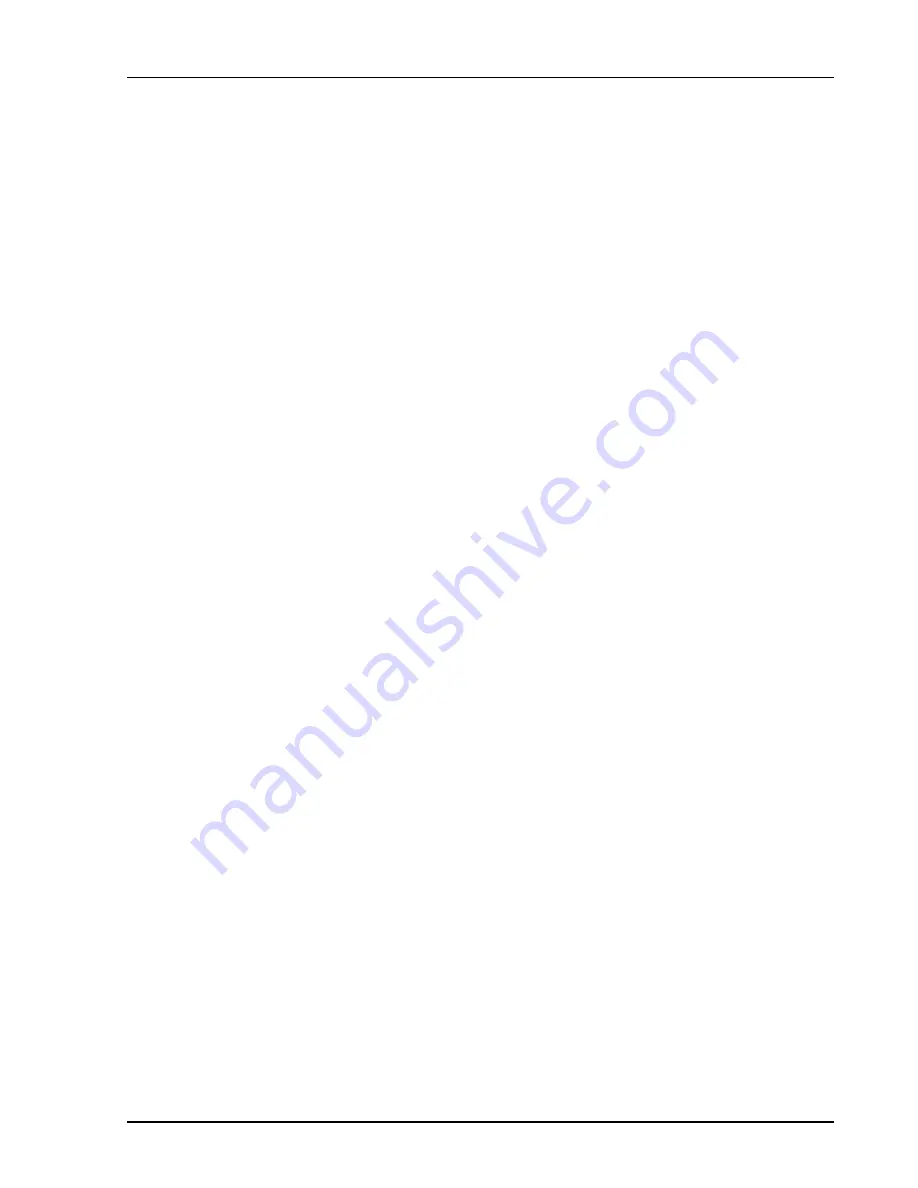
Appendix A
SRS Residual Gas Analyzer
9
At 2:40, the load lock is opened to the main chamber causing a jump in pressure. The
rise in oxygen and oil pressure indicates that the procedure is operating poorly. Even
though the load lock was purged three times with 99.999% nitrogen, oxygen was still
introduced into the chamber. This was either caused by a small air leak into the load
lock, or permeation of oxygen out of the elastomer seals on the load lock. The rise in oil
partial pressure indicates that the trap on the mechanical pump is exhausted and has
allowed oil to backstream into the load lock.
At 3:09, the valve between the load lock and main chamber is closed, and the pressures
begins to return towards their base values. Oxygen is pumped out of the chamber.
Hydrogen, water, and nitrogen recover their original values, but slowly. The oil is
alarming because it persists at a higher concentration. If this sequence occurred several
more times, the oil would continue to increase. The RGA allows it to be detected before
reaching undesirable levels.
Table Mode
The noise floor of the Faraday cup detector is about 10
-10
mbar. Since the maximum
operating pressure is 10
-4
mbar, the dynamic range of the RGA is 6 decades or 1 ppm.
The noise floor of the channel electron multiplier (CEM) is lower, but its maximum
operating pressure also decreases with the noise floor. The two pressure limits change
such that the dynamic range of the CEM is still 6 decades. By switching between the two
detectors, measurements covering more than 6 decades can be made. The table mode of
the SRS RGA software allows such a measurement to be made. The CEM status can be
set independently for each mass being monitored. Figure 5 shows a configuration where
the prevalent gases are detected with the FC and the low pressure gases are detected with
the CEM. A comparison of the value for nitrogen and “floor” show that the apparent
dynamic range is 8 decades or 10 ppb. The program will automatically sort the channels
so that all the measurements requiring the CEM are made as a group, which minimizes
the switching on and off of the detector. Without the ability to choose between FC and
CEM detector for each channel, the CEM would have to be used for all channels so that
the low pressure gases could be detected. Operation like this would cause the CEM
detector to saturate at the high pressure peaks. Saturation of the detector makes the value
useless, and also increases the physical wear on the CEM.
Summary of Contents for RGA100
Page 4: ...SRS Residual Gas Analyzer iv...
Page 18: ...xviii Command List SRS Residual Gas Analyzer...
Page 46: ...2 14 Residual Gas Analysis Basics SRS Residual Gas Analyzer...
Page 66: ......
Page 78: ...4 12 Mass Filter Power supply SRS Residual Gas Analyzer...
Page 104: ......
Page 107: ...Programming the RGA Head 6 3 SRS Residual Gas Analyzer Error Byte Definitions 6 69...
Page 216: ...8 26 Quadrupole filter cleaning SRS Residual Gas Analyzer...
Page 246: ...11 2 SRS Residual Gas Analyzer...
Page 247: ......
Page 248: ......
Page 268: ...Appendix B SRS Residual Gas Analyzer 7...
Page 312: ...Appendix D SRS Residual Gas Analyzer 27...