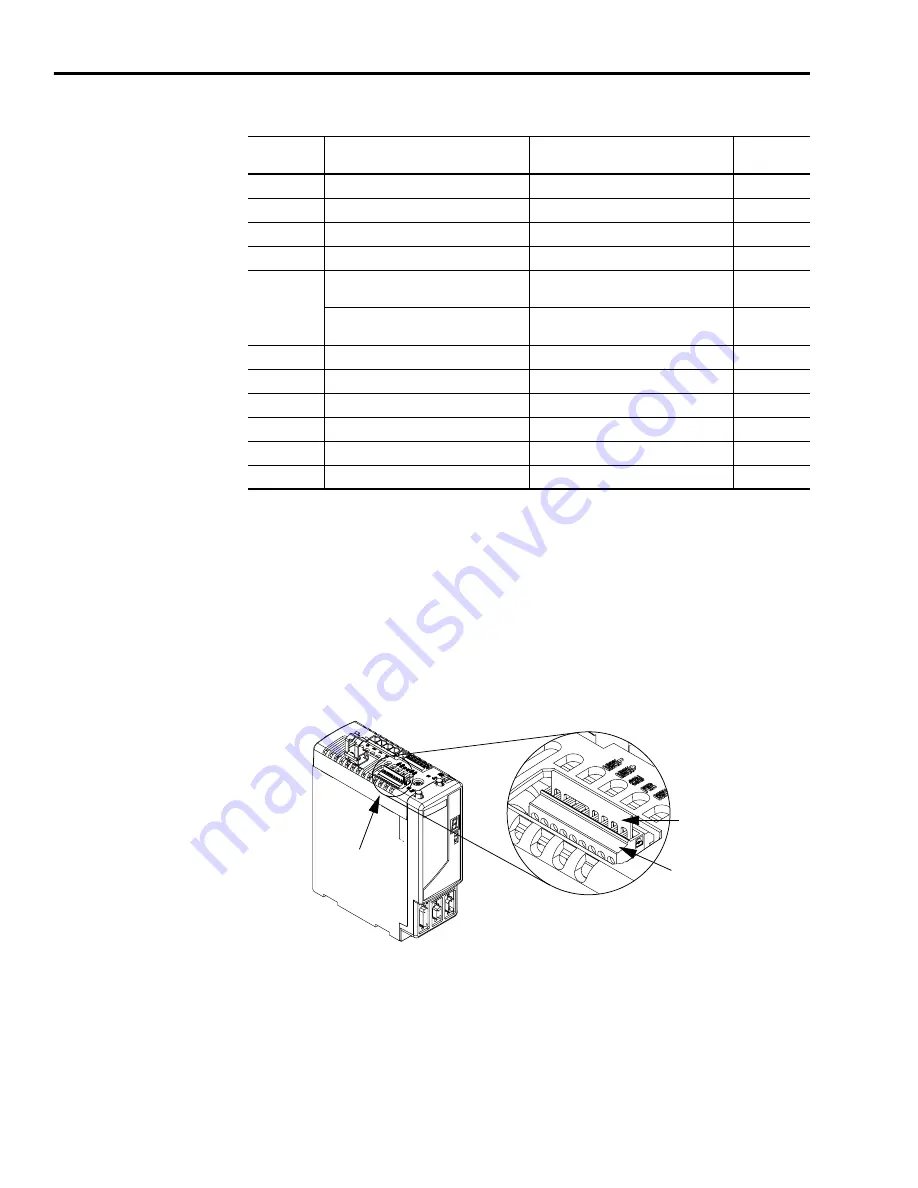
Publication 2094-UM001A-EN-P — September 2006
52
Kinetix 6000 Connector Data
Integrated Axis Module/Axis Module Connectors
Safe-off Connector Pinout
Each IAM (2094-
x
C
xx
-M
xx
-S) and AM (2094-
x
M
xx
-S) ships with the
(9-pin) wiring plug header and motion allowed jumper installed in the
safe-off (SO) connector. With the motion allowed jumper installed, the
safe-off feature is not used.
Motion Allowed Jumper
Designator
Description
Connector
Present on
IAM or AM
IOD
User I/O (drive)
26-pin high-density D-shell
IAM/AM
MF
Motor feedback
15-pin high-density D-shell (female)
IAM/AM
AF
Auxiliary feedback
15-pin high-density D-shell (male)
IAM/AM
CPD
Control input power (drive)
2-position plug/header
IAM
IPD
VAC Input Power (drive) 230V and
dc bus
6-position plug/header
IAM
VAC Input Power (drive) 460V and
dc bus
6-position plug/header
IAM
CED
Contactor enable
2-position plug/header
IAM
MP
Motor power
4-position plug/header
IAM/AM
BC
Dynamic/motor brake
6-position plug/header
IAM/AM
SO
Safe-off
9-position plug/header
IAM/AM
Tx and Rx
SERCOS transmit and receive
SERCOS fiber-optic (2)
IAM/AM
DPI
DPI
DPI
IAM
1 2
3 4
5 6
7 8
9
1
Motion Allowed Jumper
Wiring Plug Header
Kinetix 6000 IAM/AM
(Kinetix 6000 AM is shown)
Safe-off
(SO) Connector
Summary of Contents for Allen-Bradley Kinetix 6000
Page 8: ...Publication 2094 UM001A EN P September 2006 8 Table of Contents...
Page 18: ...Publication 2094 UM001A EN P September 2006 18 Start...
Page 118: ...Publication 2094 UM001A EN P September 2006 118 Connecting the Kinetix 6000 Drive System...
Page 190: ...Publication 2094 UM001A EN P September 2006 190 Specifications and Dimensions...
Page 265: ...Publication 2094 UM001A EN P September 2006 265 Notes...
Page 266: ...Publication 2094 UM001A EN P September 2006 266 Notes...
Page 267: ...Publication 2094 UM001A EN P September 2006 267 Notes...