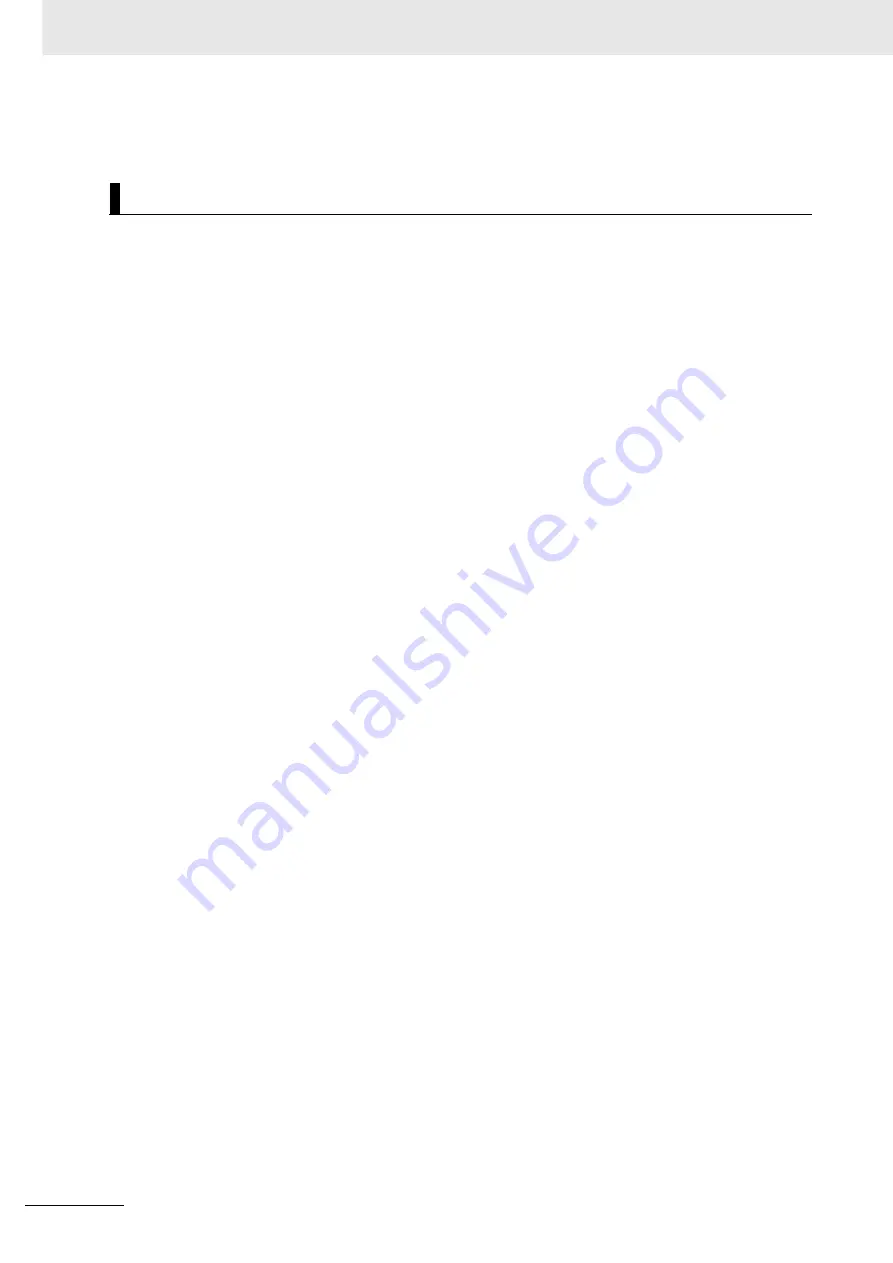
Precautions for Safe Use
24
NJ-series NJ Robotics CPU Unit User’s Manual (W539)
Refer to the
NJ/NX-series CPU Unit Built-in EtherCAT Port User's Manual
(Cat. No. W505) for
details.
• Confirm the axis number carefully before you perform an MC Test Run.
• The motor is stopped if communications are interrupted between the Sysmac Studio and the CPU
Unit during an MC Test Run. Connect the communications cable between the computer and CPU
Unit securely and confirm that the system will not be adversely affected before you perform an MC
Test Run.
• Always execute the Save Cam Table instruction if you change any of the cam data from the user pro-
gram in the CPU Unit or from the Sysmac Studio. If the cam data is not saved, the previous condition
will be restored when the power is turned ON again, possibly causing unexpected machine opera-
tion.
• The positive drive prohibit input (POT), negative drive prohibit input (NOT), and home proximity input
(DEC) of the Servo Drive are used by the MC Function Module as the positive limit input, negative
limit input, and home proximity input. Make sure that the signal widths for all of these input signals
are longer than the control period of the MC Function Module. If the input signal widths are shorter
than the control period, the MC Function Module may not be able to detect the input signals, resulting
in incorrect operation.
• During setting, ensure a correct relationship between the direction of commands issued by the Con-
troller and the motor rotation direction of the Servo Drive. Otherwise, a robot may operate unexpect-
edly.
• Select a correct combination of the kinematics type and workspace type for the MC_SetKinTransform
(Set Kinematics Transformation) instruction to ensure proper workspace check. Check that the work-
space check function is performed as intended.
• Adjust the home of the robot before you start robot operation.
• Do not operate the robot outside the workspace while the workspace check function is disabled. If
you do so, the robot may be damaged.
• Use the MC_SyncOut (End Synchronization) instruction to stop the operation caused by the
MC_SyncLinearConveyor (Start Conveyor Synchronization) instruction.
• If you set 0 for the MaxVelocity (Velocity Error Detection Value) or MaxAcceleration (Acceleration
Error Detection Value) parameter for input variables, or if you use the default (0) of these variables,
the velocity error check or acceleration error check is not performed. Properly set the MaxVelocity
(Velocity Error Detection Value) and MaxAcceleration (Acceleration Error Detection Value) to avoid
an unexpected velocity and acceleration.
• If a robot tool (ToolID: 1 to 16) other than TCP0 is selected, the system does not perform the
pre-check of the MaxVelocity (Velocity Error Detection Value) and MaxAcceleration (Acceleration
ErrorDetection Value) parameters in the robotics instruction.
• When using Cartesian 2D kinematics, configure Plane correctly. Otherwise, a robot may operate
unexpectedly.
• When Synchronized stop with Deceleration is selected in MC_SyncOut (End Synchronization)
instruction and Deceleration target time T5 is set to long time, it is possible to reach out of the work-
space during deceleration. Do not disable workspace check.
• Select
Immediate stop
or
Immediate stop and Servo OFF
when using Delta 3, Delta 3R, Delta 2, Car-
tesian 2D Gantry or Cartesian 3D Gantry robot.
• Set 0 for Maximum Deceleration which are linked mechanically, when using Delta 3, Delta 3R, Delta
2, Cartesian 2D Gantry or Cartesian 3D Gantry robot.
Motion Control
Summary of Contents for NJ501-4300
Page 13: ...11 CONTENTS NJ series NJ Robotics CPU Unit User s Manual W539 ...
Page 40: ...Revision History 38 NJ series NJ Robotics CPU Unit User s Manual W539 ...
Page 90: ...2 Features of NJ Robotics CPU Unit 2 40 NJ series NJ Robotics CPU Unit User s Manual W539 ...
Page 204: ...5 Vision Robot Integrated Simulation 5 6 NJ series NJ Robotics CPU Unit User s Manual W539 ...
Page 308: ...6 Troubleshooting 6 104 NJ series NJ Robotics CPU Unit User s Manual W539 ...
Page 333: ...I 1 I NJ series NJ Robotics CPU Unit User s Manual W539 Index ...
Page 335: ......