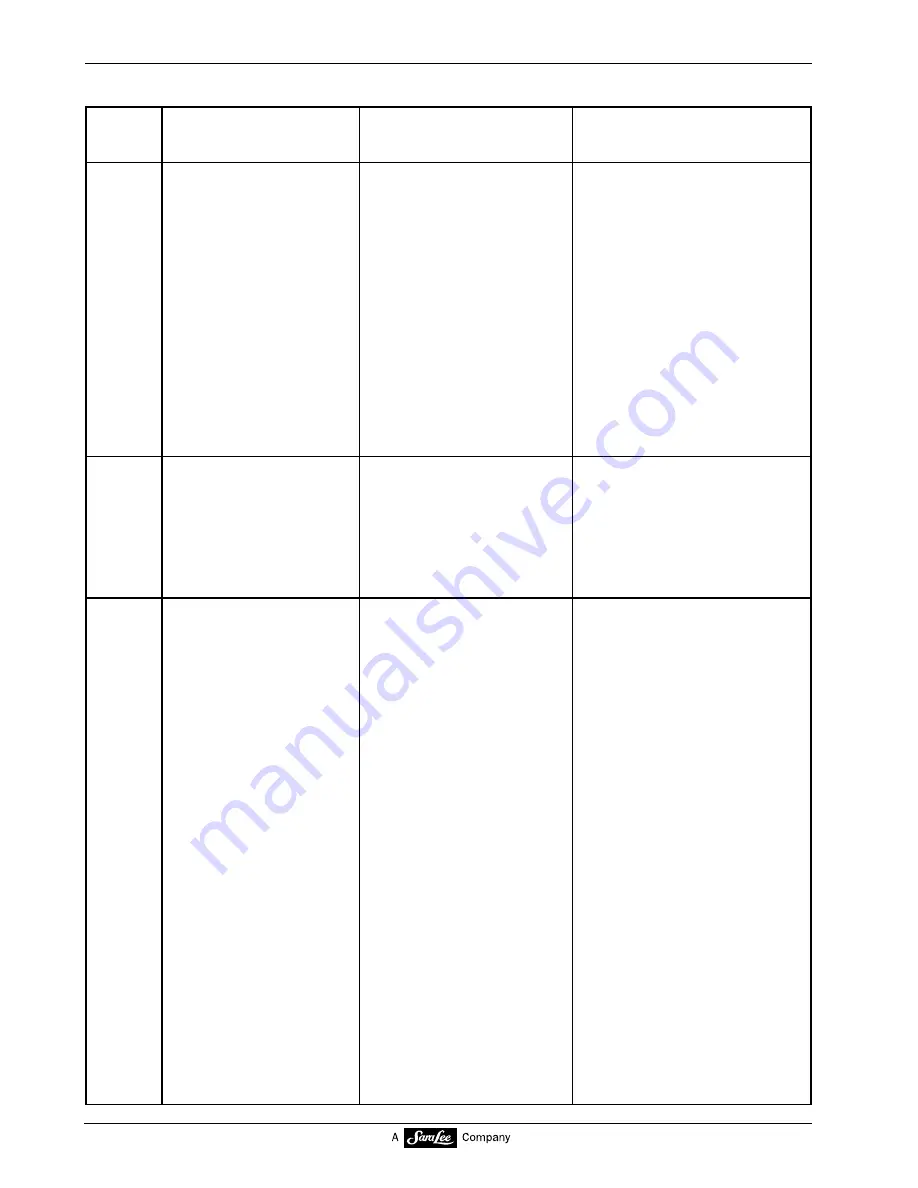
January 2001
3 - 8
Trouble Shooting, Error Codes and Fault Diagnosis
Service Manual Cafitesse 500
Display
Malfunction
Cause
Remedy
1. Check the wires, replace
them if necessary.
2. Replace the board of the
service panel
(see pg. 5.K-8)
3. Replace the interconnection
board (see pg. 5K-9)
4. Replace control board box
(see pg. 5K-4)
Reset program to factory
default and reprogram
1. Clean combi-trough and
replace it if required
(see pg. 5.C-7)
2. Check motor and wires
(BU21), replace them if
necessary (see pg. 5.C-5)
3. Replace the sensor board or
check the wires (BU 23)
(see pg. 5.C-6)
Replace control board box if
necessary.
1. Wires PIN 13-16 (BU21-
I
2
C) between control
board box and inter-
connection board are
defective
2. Board of the service
panel is defective.
3. Interconnection board
defective
4. MCB or I
2
C bus driver
board defective
Coin module not used in
the U.S.
1. Auto-diaphragm moves
sluggishly
2. Motor for auto-diaphragm
or wires P18/2,4 (BU 21)
defective
3. Sensor board (2 Hall
sensors) or wires P18/5-
7, P20/3,4 (BU23)
defective
ERR13
Error in internal
communication.
"ON/OFF" LED flashes.
Dispenser remains on.
Cooling remains on.
ERR14
Error in Coin Interface
The LEDs for "EMPTY"
and "ON/OFF" are
flashing.
Dispenser is switched off.
Cooling remains on.
ERR15
Error auto-diaphragm
The LEDs for "EMPTY"
and "ON/OFF" are
flashing.
Dispenser is switched off.
Cooling remains on.
Movement of auto-
diaphragm incorrect.
Nominal position was not
reached after 3 tries.