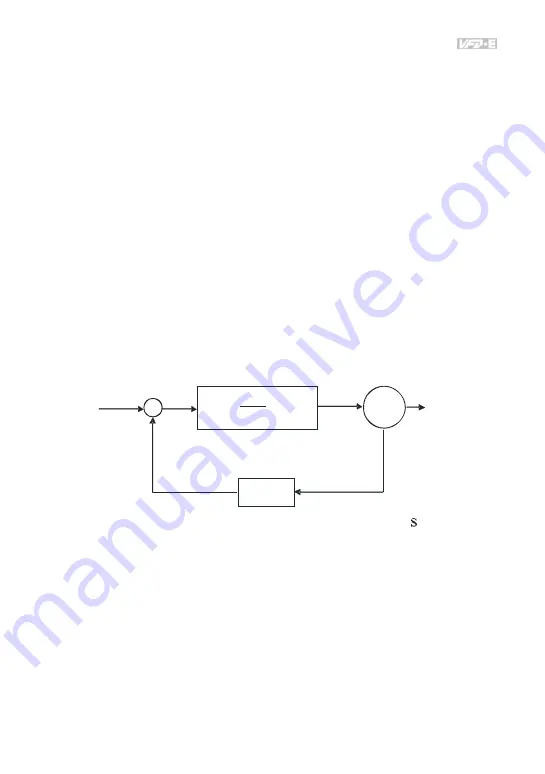
Chapter 4 Parameters
4-152
Group 10: PID Control
A. Common applications for PID control
1. Flow control: A flow sensor is used to feedback the flow data and perform accurate flow control.
2. Pressure control: A pressure sensor is used to feedback the pressure data and perform precise
pressure control.
3. Air volume control: An air volume sensor is used to feedback the air volume data to have excellent
air volume regulation.
4. Temperature control: A thermocouple or thermistor is used to feedback temperature data for
comfortable temperature control.
5. Speed control: A speed sensor or encoder is used to feedback motor shaft speed or input another
machines speed as a target value for closed loop speed control of master-slave operation.
Pr.10.00 sets the PID setpoint source (target value). PID control operates with the feedback signal as
set by Pr.10.01 either 0~+10V voltage or 4-20mA current.
B. PID control loop:
S)
T
S
T
1
(1
K
d
i
p
IM
+
-
Setpoint
drive ex ecute PID control output value
feedback s ignal
sensor
p
K
: Proportional gain(P)
i
T
: Integral time(I)
d
T
: Derivative control(D)
: Operator
C. Concept of PID control
1. Proportional gain(P): the output is proportional to input. With only proportional gain control, there
will always be a steady-state fault.
2. Integral time(I): the controller output is proportional to the integral of the controller input. To
eliminate the steady-state fault, an “integral part” needs to be added to the controller. The integral
time decides the relation between integral part and fault. The integral part will be increased by time
even if the fault is small. It gradually increases the controller output to eliminate the fault until it is 0. In