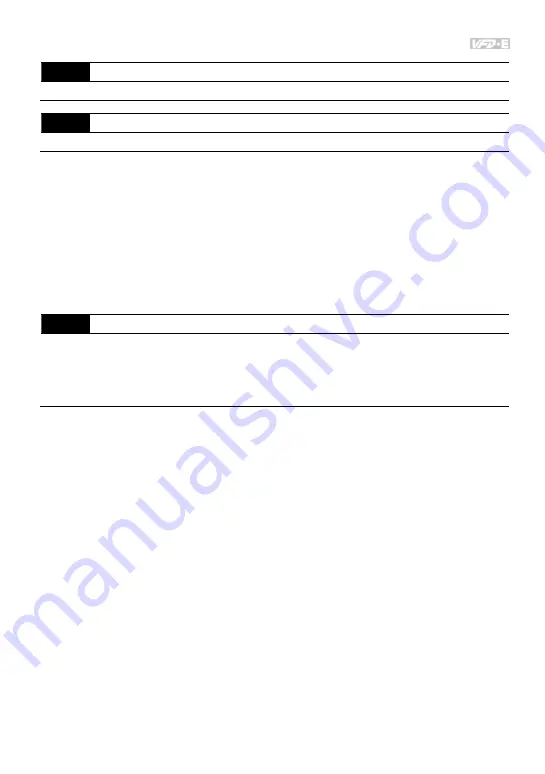
Chapter 4 Parameters
4-111
06.04
Over-Torque Detection Level (OL2)
Unit: %
Settings
10 to 200%
Factory Setting: 150
06.05
Over-Torque Detection Time (OL2)
Unit: second
Settings
0.1 to 60.0 sec
Factory Setting: 0.1
Pr.06.04 is proportional to the Rated Output Current of the drive.
Pr.06.05 sets the time for how long over-torque must be detected before “OL2” is displayed.
The method to detect over-torque is shown as follows:
1. when output current exceeds over-torque detection level (Pr.06.04)
2. when over-torque time exceeds over torque detection time (Pr.06.05)
If a Multi-function Output Terminal is set to over-torque detection (Pr.03.00~03.01=04), the
output is on. Please refer to Pr.03.00~03.01 for details.
For general motor, the output torque and output current of the AC motor drive will in proportion
in V/f control. Thus, it can use the output current of the AC motor drive to limit the output
torque of motor.
Related parameters: Pr.03.00(Multi-function Output Relay (RA1, RB1, RC1)) and
Pr.03.01(Multi-function Output Terminal MO1)
06.06
Electronic Thermal Overload Relay Selection (OL1)
Factory Setting: 2
Settings
0
Operate with a Standard Motor (self-cooled by fan)
1
Operate with a Special Motor (forced external cooling)
2
Operation
disabled
This parameter is used to set the operation selection of the electronic thermal overload relay.
This function is used to protect the motor from overloading or overheating. When the motor
(self-cooled by fan) operates in low frequency, overload is seldom happened. Refer to the
following figure for the application.
When the rated current of motor is less than drive’s or bad design of the motor heat dissipation,
it can use this parameter to limit the output current of the AC motor drive to prevent motor from
overheating or damage.
Setting 0: the electronic thermal relay is used for standard motor(heatsink is fixed on rotor
shaft). When operating in low speed, the motor heat dissipation function will be bad. Thus, it
needs to decrease the action time of the electronic thermal relay to ensure the motor life.
Setting 1: the electron thermal relay is used for special motor(heatsink uses independent
power). The heat dissipation function has no direction relation with rotation speed. Thus, the
electronic thermal relay is still held in low speed to ensure the motor load ability in low speed.
In the frequent power ON/OFF applications, it can’t use this parameter (even set to 0 or 1) for
protection due to this function will be reset once the power is OFF. Thus, it needs to add the
thermal relay on each motor when an AC motor drive is connected with several motors.
Setting 0 or 1: when the electronic thermal relay protection is enabled in low speed operation,
the AC motor drive will display “OL1” and free run to stop. It needs to press “RESET” to clear
the warning message.
Related
parameter:
Pr.06.07(Electronic Thermal Characteristic)