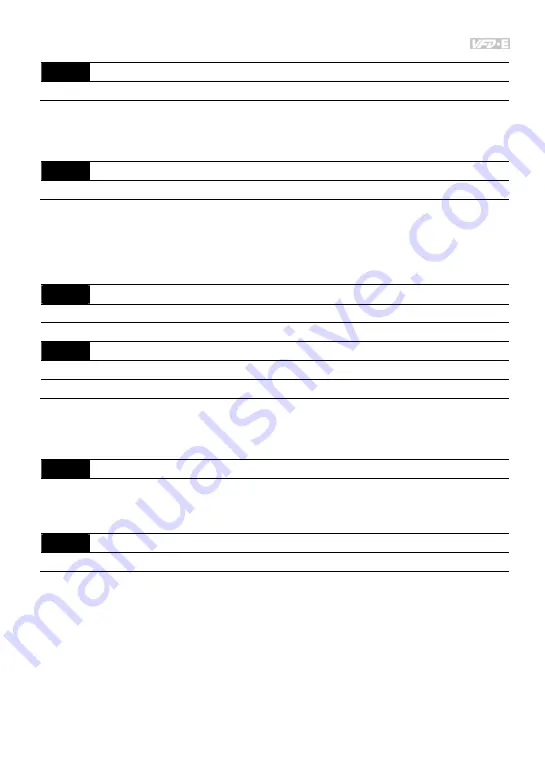
Chapter 4 Parameters
4-119
07.08
Torque Compensation Time Constant
Unit: second
Settings
0.01 ~10.00 sec
Factory Setting: 0.30
It is usually applied in those heavy load applications which the motor current is changed
frequently. The current is changed for the current compensation to increase the output torque.
Because the frequent current change will cause the machine vibration, it can increase Pr.07.08
setting to solve this problem at this moment.
07.09
Slip Compensation Time Constant
Unit: second
Settings
0.05 ~10.00 sec
Factory Setting: 0.20
It is usually applied in those heavy load applications which the motor speed is changed
frequently. The speed is changed for the speed compensation to reach the synchronous speed.
Because the frequent speed change will cause the machine vibration, it can increase Pr.07.09
setting to solve this problem at this moment..
Too long time constants (set Pr.07.08 and Pr.07.09 to 10) give slow response; too short values
can give unstable operation. Please set by your applications.
07.10
Accumulative Motor Operation Time (Min.)
Settings
0
Factory Display: ##
Displays
0~1439
07.11
Accumulative Motor Operation Time (Day)
Settings
0
Factory Display: ##
Displays
0
~65535
Pr.07.10 and Pr.07.11 are used to record the motor operation time. They can be cleared by
setting to 0 and time is less than 1 minute is not recorded.
When setting Pr.07.11 to 0, it will reset the accumulative motor operation time and the record
will be reset to 0.
07.12
Motor PTC Overheat Protection
Factory Setting: 0
Settings
0
Disable
1
Enable
07.14
Motor PTC Overheat Protection Level
Unit: V
Settings
0.1~10.0V
Factory Setting: 2.4
When the motor is running at low frequency for a long time, the cooling function of the motor
fan will be lower. To prevent overheating, it needs to have a Positive Temperature Coefficient
thermoistor on the motor and connect its output signal to the drive’s corresponding control
terminals.
When the source of first/second frequency command is set to AVI (02.00=1/02.09=1), it will
disable the function of motor PTC overheat protection (i.e. Pr.07.12 cannot be set to 1). Only
one of the source of first master frequency command and second master frequency command
can be enable at one time.