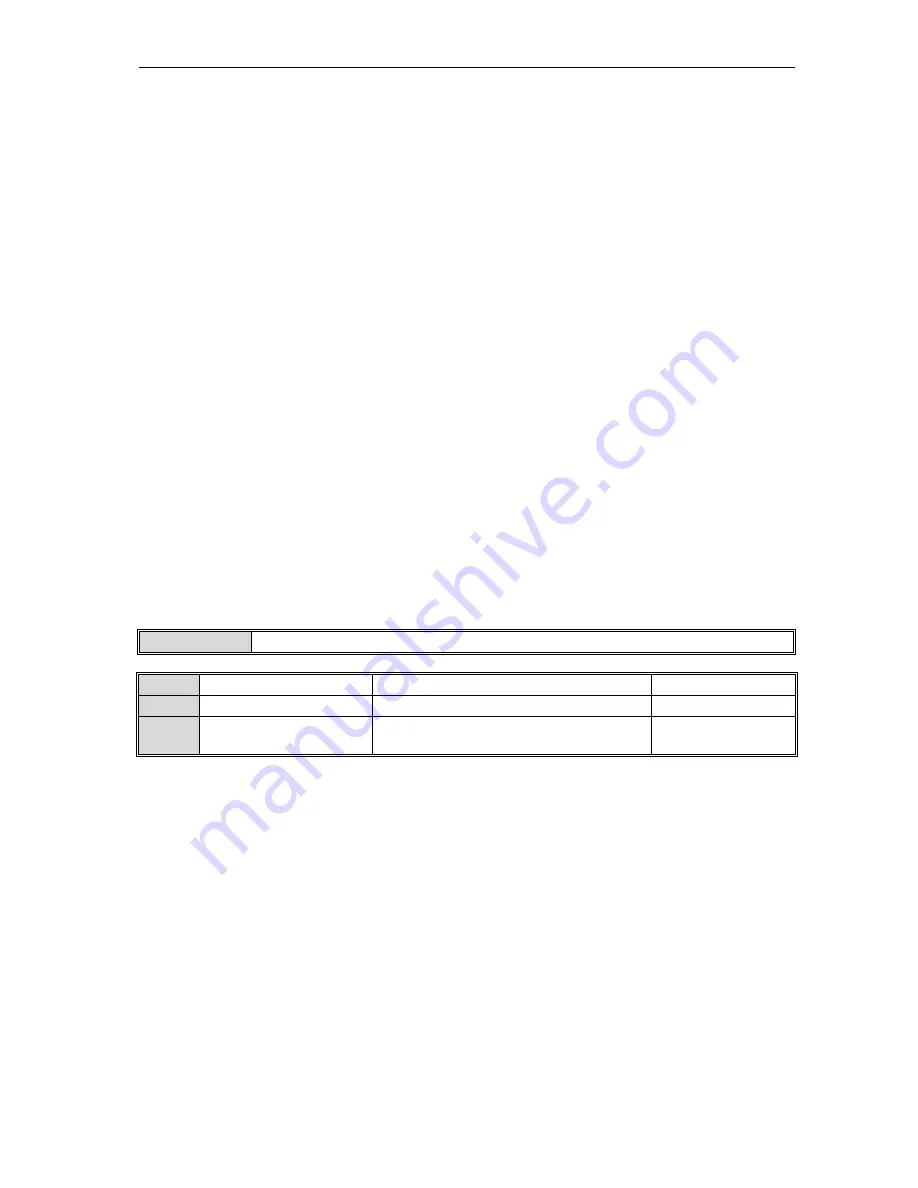
AC90 TENSION CONTROL FREQUENCY INVERTER MANUAL
Function Parameter specifications
104
0: No operation
Set as default without self study.
1: Rotary type self-study
Before self adjustment,
[F5.01-F5.06]
of asynchronic motor which is controlled must be set
as right value. While self adjustment, firstly, asynchronic motor at static state, it automatic detects motor stator
resistance, motor rotor resistance, motor stator&rotor inductance.Then the asynchronic motor at rotate state, it
automatic detectes motor no-load current, motor stator&rotor mutual inductance. All results will be auto writted in
[F5.08]
,
[F5.09]
,
[F5.10]
and
[F5.07]
,
[F5.11]
and renewed while adjustment is over. After parameter setting, press
FWD key to start self study, keyboard LED display “t-01”. Motor automatic stop while self adjustment is over.Inverter
reback to standby state.
2: Resting type self-study
Before self adjustment,
[F5.01-F5.06]
of motor which is controlled must be set as right
value. While self adjustment, motor at static state, it automatic detects motor stator resistance, motor rotor resistance,
motor stator&rotor inductance. All results will be auto writted in
[F5.08]
,
[F5.09]
,
[F5.10]
and renewed while adjustment
is over. After parameter setting, press FWD key to start self study, keyboard LED display “t-02”.FWD indicator is off
while self adjustment is over.Inverter reback to standby state.
Note: [F5.12] is automatic set as 0 after self adjustment.
Attention: 1. Before set ting [F5.12] as 1 –self study, unload the motor firstly.
2. In some occasions (such as can not unload), if it can not self study or it is not high control
accuracy required, static self study or no self study is ok. If no self study, please do set right
parameters [F5.01-F5.06]
3. If user know the right parameter. User can set [F5.01-F5.11] directly.
4. Ensure stop state before startting self study, otherwise, self study can not be normal.
5. While [F5.12] is 1, if there is over voltage or over current in self study process, ACC/DEC time
[F0.14, F0.15] can be prolonged.
6. If static self study is not successful, alarm E.tE1 fault. If rotary self study is not successful, alarm
E.tE2 fault.
F5.13-F5.14 Reserved
F5.15
PG selection
Setting range: 0000-1111 Factory
set: 0001
F5.16
PG pulse per loop
Setting range: 0-60000 Factory
set: 1024
F5.17
PG line-break inspection
time
Setting range: 0.100-60.000s
Factory set: 2.000s
PG selection:
LED “0” digit: Input phase
0: 1-phasee input
Only feedback one of A and B and inspect motor speed.Not identify direction.
1: 2-phase input
Feedback both A and B. Inspect both speed and direction.
LED “00” digit: input phase adjustment
While encoder A/B phase is converse, it can be adjusted by this parameter. No need to change the wire. Only valid
while both phase are valid.
0: same direction
Sensor phase is the same as motor phase, no meed adjust.
1: reverse direction
Sensor phase is reverse to motor phase, meed adjust.
LED “000” digit:
0: break inspection OFF
No line-break inspection.
1: break inspection ON
While feedback signal of sensor disappears and after
[F5.17]
delay time, still no feedback
signal is received. Inverter will alarm for PG line-break fault and stop output.Motor free stop.
LED “0000” digit: PG feedback channel