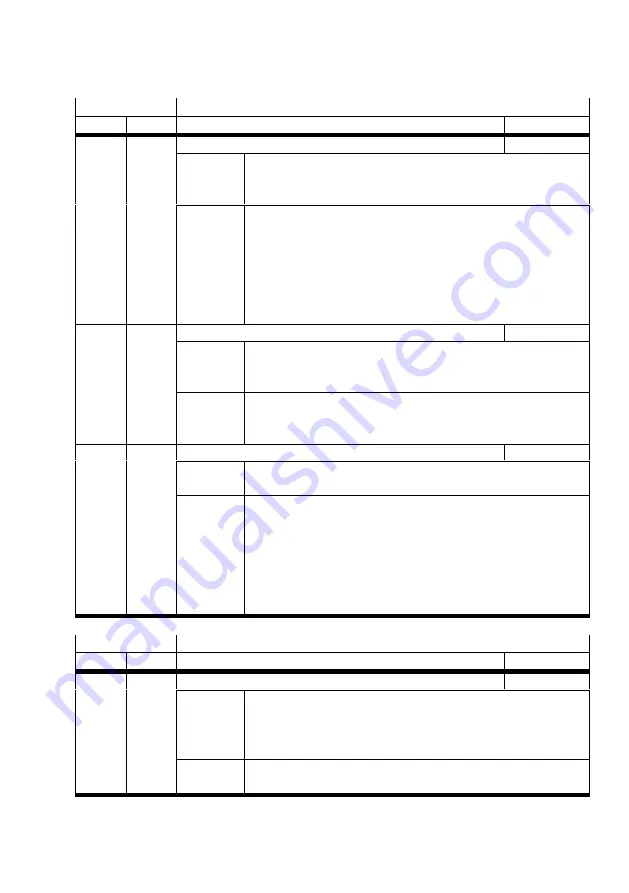
B
Diagnostic messages
Festo – GDCP-CMMP-M3/-M0-C-CO-EN – 1510b – English
265
Error group 57
Input/output error (only CMMP-AS-...-M3)
No.
Reaction
Message
Code
57-1
80E2h
Digital inputs - wrong signal level
configurable
Cause
Exceeding / violation of discrepancy time with multi-channel inputs
(DIN40 ... DIN43, two-handed control device, mode selector
switch).
Measure
Check the external active and passive sensors do they switch
on two channels and simultaneously (within the parameterised
discrepancy time).
Two-handed control device: Check how the device is operated
by the user are both pushbuttons pressed within the discrep
ancy time? Give training if necessary.
Check the set discrepancy times are they sufficient?
57-2
-
Digital inputs - missing test pulse
configurable
Cause
–
One or more inputs (DIN40 ... DIN49) were configured for the
evaluation of test pulses from the outputs (DOUT40 ... DOUT
42). The test pulses from DOUTx do not arrive at DIN4x.
Measure
Check the wiring (shorts after 0 V, 24 V, cross circuits).
Check the assignment correct output selected / configured
for test pulse?
57-6
-
Electronic temperature too high
configurable
Cause
–
The safety module's temperature monitor has been triggered;
the temperature of μC1 or μC2 was below -20° or above +75°C.
Measure
Check the operating conditions (ambient temperature, control
cabinet temperature, installation situation in the control cab
inet).
If the motor controller is experiencing high thermal load (high
control cabinet temperature, high power consumption / output
to motor, large number of occupied slots), a motor controller of
the next highest output level should be used.
Error group 58
Error during communication / parameterisation (only CMMP-AS-...-M3)
No.
Code
Message
Reaction
58-0
80E9h
Plausibility check parameters
configurable
Cause
The plausibility check in the safety module produced errors, e.g. an
invalid angle encoder configuration; the error is triggered when a
validation code is requested by the SafetyTool and when paramet
ers are backed up in the safety module.
Measure
Note instructions for SafetyTool for complete validation; critic
ally check parameterisation.