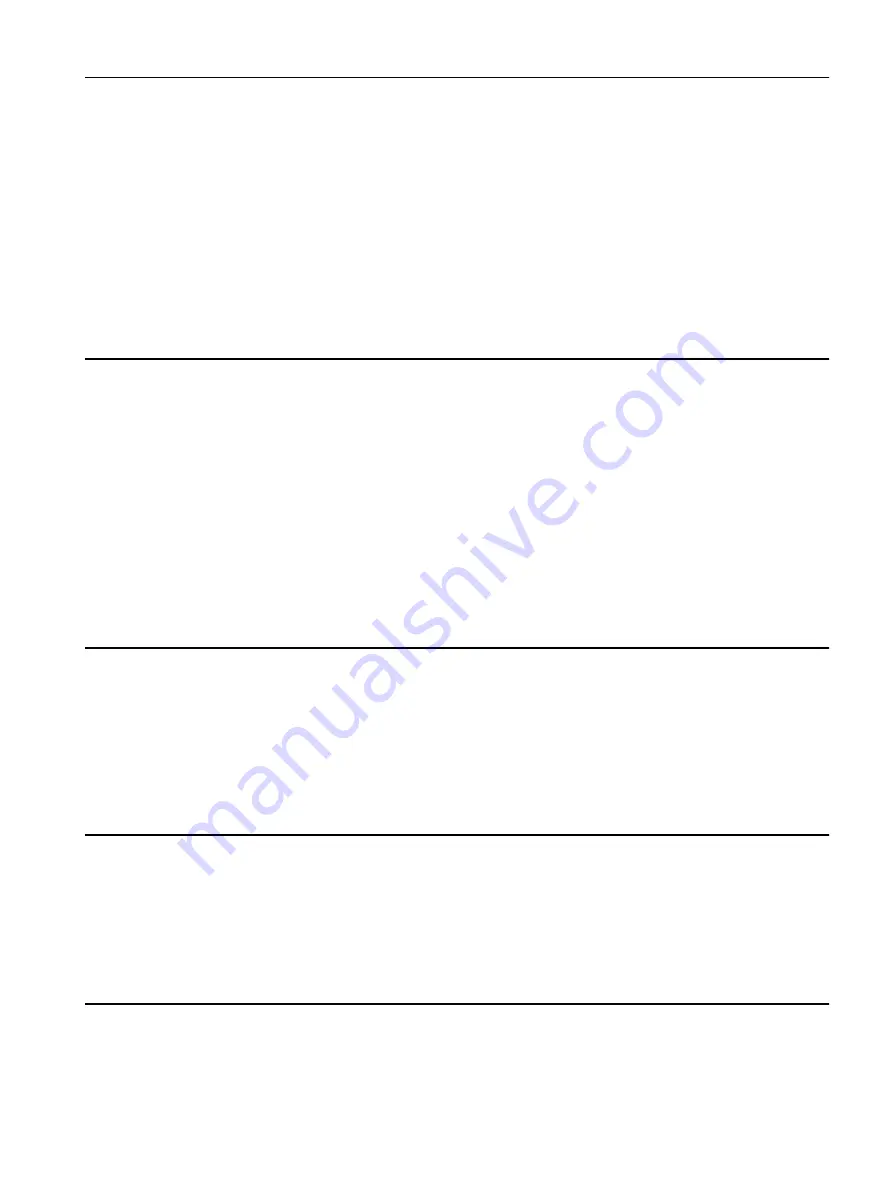
Cause:
Fault value (r0949, interpret bitwise binary):
Bit 1: Switch "Closed" feedback signal missing.
Bit 2: Switch "Open" feedback signal missing.
Bit 3: Switch feedback signal too slow.
After switching, the system waits for the positive feedback signal. If the feedback signal is received later than the specified
time, then a fault trip (shutdown) is issued.
Bit 6: Line Side Switch feedback signal not consistent with the bypass state.
When switching-on or when switching-in the motor, the line side switch is closed without this having been requested from
the bypass.
See also: p1260, r1261, p1266, p1267, p1269, p1274
Remedy:
- check the transfer of the feedback signals.
- check the switch.
F07320
Drive: Automatic restart interrupted
Reaction:
OFF2
Acknowledge:
IMMEDIATELY
Cause:
- the specified number of restart attempts (p1211) has been completely used up because within the monitoring time
(p1213) the faults were not able to be acknowledged. The number of restart attempts (p1211) is decremented at each new
start attempt.
- the monitoring time for the power unit has expired (p0857).
- when exiting commissioning or at the end of the motor identification routine or the speed controller optimization, the drive
unit is not automatically switched on again.
Fault value (r0949, interpret hexadecimal):
Only for internal Siemens troubleshooting.
Remedy:
- increase the number of restart attempts (p1211). The actual number of starting attempts is displayed in r1214.
- increase the delay time in p1212 and/or the monitoring time in p1213.
- either increase or disable the monitoring time of the power unit (p0857).
- reduce the delay time to reset the start counter (p1213[1]) so that fewer faults are registered in the time interval.
A07321
Drive: Automatic restart active
Reaction:
NONE
Acknowledge:
NONE
Cause:
The automatic restart (AR) is active. When the line supply returns and/or the causes of the existing faults are removed the
drive is automatically restarted. The pulses are enabled and the motor starts to rotate.
For p1210 = 26, restarting is realized with the delayed setting of the ON command.
Remedy:
- the automatic restart (AR) should, if required, be inhibited (p1210 = 0).
- an automatic restart can be directly interrupted by withdrawing the switch-on command (BI: p0840).
- for p1210 = 26: by withdrawing the OFF2- / OFF3 command.
A07325
Drive: Hibernation mode active - drive automatically switched-on again
Reaction:
NONE
Acknowledge:
NONE
Cause:
The "hibernation" function is active (p2398). The drive automatically powers itself up again as soon as the restart conditions
are present.
See also: p2398, r2399
Remedy:
Not necessary.
The alarm is automatically withdrawn when the motor is restarted or when the motor is manually switched off.
F07330
Flying restart: Measured search current too low
Reaction:
OFF2 (NONE, OFF1)
Acknowledge:
IMMEDIATELY
Warnings, faults and system messages
9.6 List of fault codes and alarm codes
SINAMICS G120X converter
Operating Instructions, 06/2019, FW V1.01, A5E44751209B AC
1003