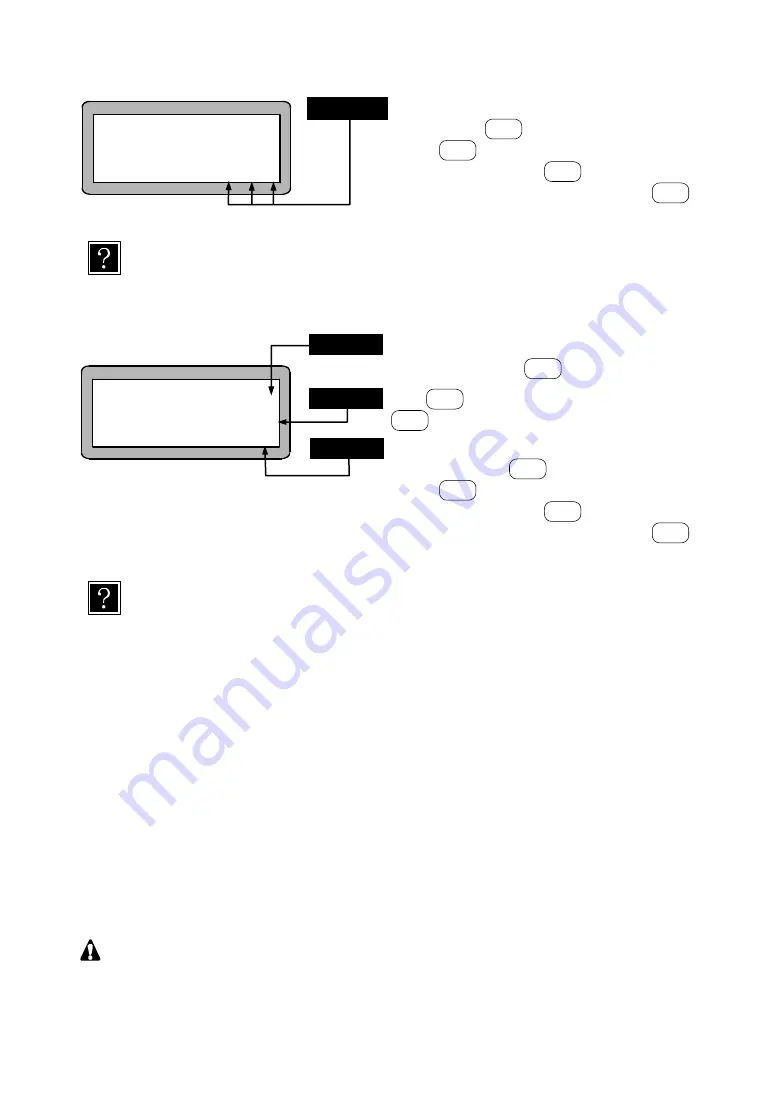
13
– 9
13.2.19 Setting of task return to origin output
Use the numeric keypad to designate the output
bit and press
ENT
.
When
NEXT
is pressed, the next screen will
display, and when
-NEXT
is pressed, the
previous screen will display. Press
ESC
to
return to the PARA mode screen.
The return to origin completion output explained in section 10.2.14 will turn ON when
all axes have return to the origin. The return to origin completed output can be set for
each task with this setting.
13.2.20 Setting of CC-Link
Use the numeric keypad to enter the station
number, and press
ENT
.
Use
ALT
to select BAUD RATE, and press
ENT
.
Use the numeric keypad to enter the option flag
value, and press
ENT
.
When
NEXT
is pressed, the next screen will
display, and when
-NEXT
is pressed, the
previous screen will display. Press
ESC
to
return to the PARA mode screen.
●The STATION option sets the CC-Link unit station number. This controller occupies
the four consecutive stations from the station number that was set. Therefore, the
valid range of setting values is 1 to 61. The setting is invalid if the 0 station or 62
station or higher is set.
(Initial value: 0, Setting range: 0 to 99)
●The BAUD RATE option sets the CC-Link transmission speed. The settable
transmission speed varies depending on the total cable length, CC-Link version, and
cable types.
(Initial value: 156K, Selection range: 156K, 625K, 2.5M, 5M, 10M)
●When the thousands place of the option value is set to "0", all system input and
general-purpose input from CC-Link is enabled.
When "1" is set, system input and general-purpose input (ports 1 to 3) of the master
unit is enabled from the input/output connectors.
(Initial value: 0000, Setting range: 0000 to 9999) (Refer to section 11.2.3.)
●The functions below are assigned to the ones place of the option value.
0: Normal
7: Maximum torque limit function (Refer to section 11.6)
8: Selection table extension in external point designation mode (Refer to section 11.5)
9: Speed control mode (Refer to section 11.4)
The other functions are assigned to the ones, tens and thousands place of
the option value. Change a value after understanding the contents of the
applicable function well. When a value is changed carelessly, the robot may
move unexpectedly and a machine or a workpiece may be damaged or
someone may be injured.
[
P
A
R
A
]
M
2
0
C
C
S
T
A
T
I
O
N
: 0
1
-
L
i
n
k
B
A
U
D
R
A
T
E
:
1
5
6
K
O
P
T
I
O
N
:
0
0
0
0
[
P
A
R
A
]
M
1
9 T
1
:
0
-
0
1
-
0
T
A
S
K H
O
M
E T
2
:
0
-
0
1
-
0
P
O
S
I
. O
U
T T
3
:
0
-
0
1
-
0
T
4
:
0
-
0
1
-
0
STEP 1
STEP 1
STEP 2
STEP 3
CAUTION
Summary of Contents for CA20-M10
Page 2: ......
Page 14: ...XII 21 6 Spare parts 21 5 21 6 1 Controller spare parts 21 5 21 6 2 Axis spare parts 21 5...
Page 24: ...1 10 This page is blank...
Page 104: ...4 20 This page is blank...
Page 112: ...5 8 This page is blank...
Page 152: ...7 20 This page is blank...
Page 190: ...10 20 This page is blank...
Page 234: ...11 44 This page is blank...
Page 244: ...12 10 This page is blank...
Page 286: ...15 4 This page is blank...
Page 300: ...17 12 This page is blank...
Page 352: ...18 52 This page is blank...
Page 382: ...21 6 This page is blank...
Page 383: ......
Page 384: ...Back cover Q3178E 03 APR 20...