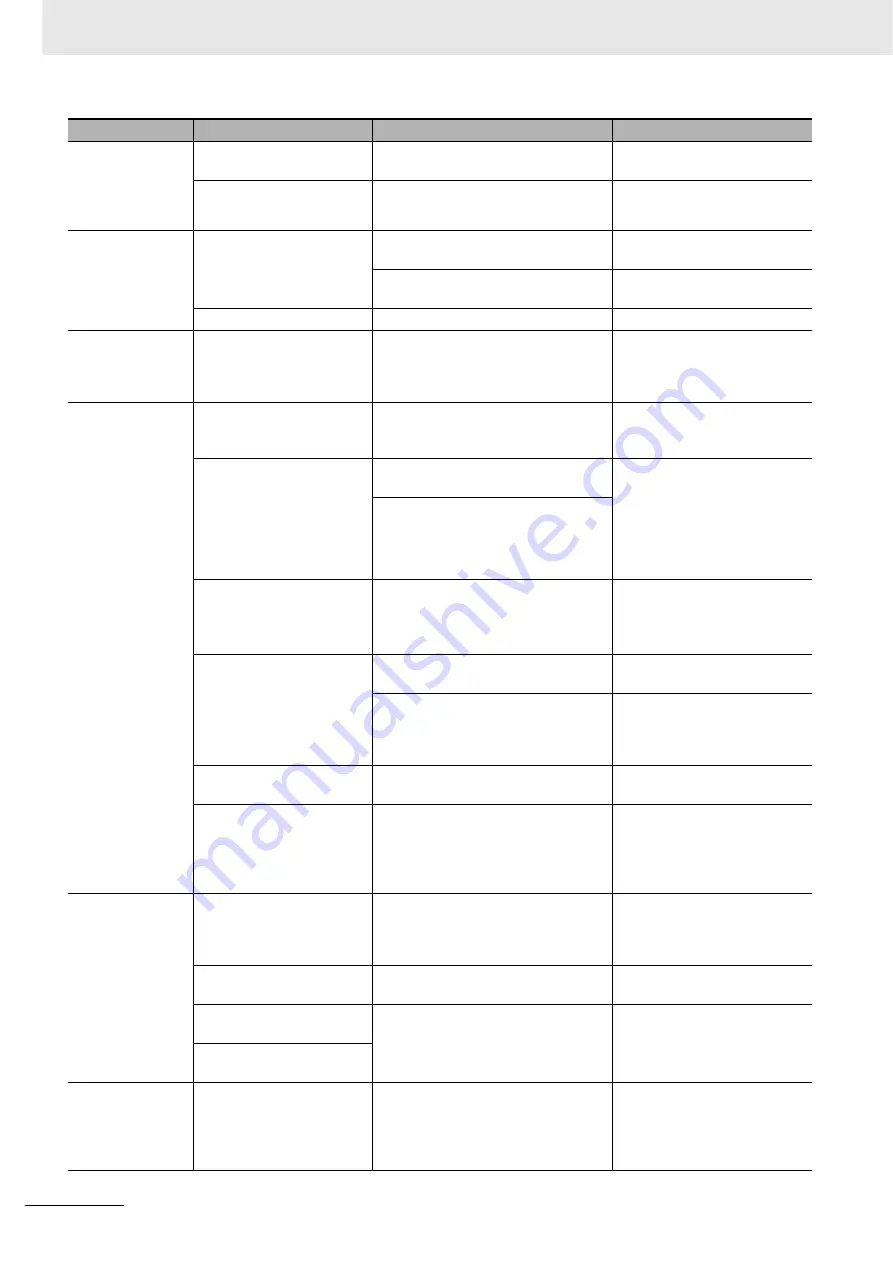
10 Troubleshooting and Maintenance
10 - 18
OMNUC G5-series (Pulse-train Input Type) AC Servomotors and Servo Drives User’s Manual
The Servomotor
operates
momentarily, but
then it does not
operate after that.
The Servomotor power
cable is wired incorrectly.
Check the wiring of the Servomotor
power cable phases U, V, and W.
Wire correctly.
The encoder cable is wired
incorrectly.
Check the encoder cable wiring.
Wire correctly.
The Servomotor
rotates without a
command.
The command pulse input
is incorrect.
Check the command pulse type.
Make sure that the command
pulse input is appropriate.
Check the command pulse voltage.
Connect a resistor that
matches the voltage.
The Servo Drive is faulty.
–
Replace the Servo Drive.
The Servomotor
rotates opposite to
the command
direction.
The CW input and the CCW
input are connected in
reverse.
Check the command pulse type of the
controller and that of the Servo Drive.
Connect the CW pulse signal to
the CW input and the CCW
pulse signal to the CCW input,
respectively.
Motor rotation is
unstable.
The Servomotor power
cable or encoder cable is
wired incorrectly.
Check the wiring of the Servomotor
power cable phases U, V, and W and
that of the encoder cable.
Wire correctly.
The load torque fluctuates
due to eccentricity of the
coupling that connects the
motor shaft to mechanical
systems, loose screws, or
poor engagement between
the pulley and the gear.
Check the connection to mechanical
systems.
Recheck and adjust the
machine.
Try to operate the Servomotor with no
load (by disconnecting the motor from
mechanical systems).
The load’s moment of
inertia exceeds the Servo
Drive’s allowable value.
Try to operate the Servomotor with no
load (by disconnecting the motor from
mechanical systems).
• Reduce the load.
• Replace the Servomotor and
the Servo Drive with larger
capacity ones.
Pulse signal lines are
connected poorly.
Check the pulse signal wiring for the
controller and the Servo Drive.
Wire correctly.
Check the command pulse type of the
controller and that of the Servo Drive.
Set the command pulse type of
the Servo Drive so that it
matches the command pulse
type of the controller.
The gain setting is
inappropriate.
–
Perform manual tuning.
Chattering occurs in an
input signal to CN1.
Check the Operation Command
(RUN), Error Counter Reset Input
(ECRST), Zero Speed Designation
Input (VZERO), and Internally Set
Speed 1/2 (VSEL1/VSEL2) signals.
Wire correctly to prevent
chattering.
The Servomotor is
overheating.
The ambient temperature is
too high.
Check to see if the ambient
temperature around the Servomotor is
over 40°C.
Lower the ambient temperature
around the Servomotor to 40°C
or less. (Use a fan or air
conditioner.)
Ventilation is blocked.
Check to see if ventilation is blocked.
Take measures to improve
ventilation.
The Servomotor is
overloaded.
Try to operate the Servomotor with no
load (by disconnecting the motor from
mechanical systems).
• Reduce the load.
• Replace the Servomotor and
the Servo Drive with larger
capacity ones.
The Servomotor vibrates
during operation.
The Servomotor’s
holding brake does
not work.
Power is supplied to the
holding brake.
Check to see if power is supplied to
the holding brake.
Design the circuit so that
stopping the Servomotor
causes the power supply to the
holding brake to turn OFF when
it holds a load.
Symptom
Probable cause
Check items
Measures
Summary of Contents for G5 R88D-KE Series
Page 3: ...2 Page 2 53 For 1 000 r min Servomotors 900 W to 3 kW Current Contents Corrected Contents...
Page 504: ......
Page 505: ......