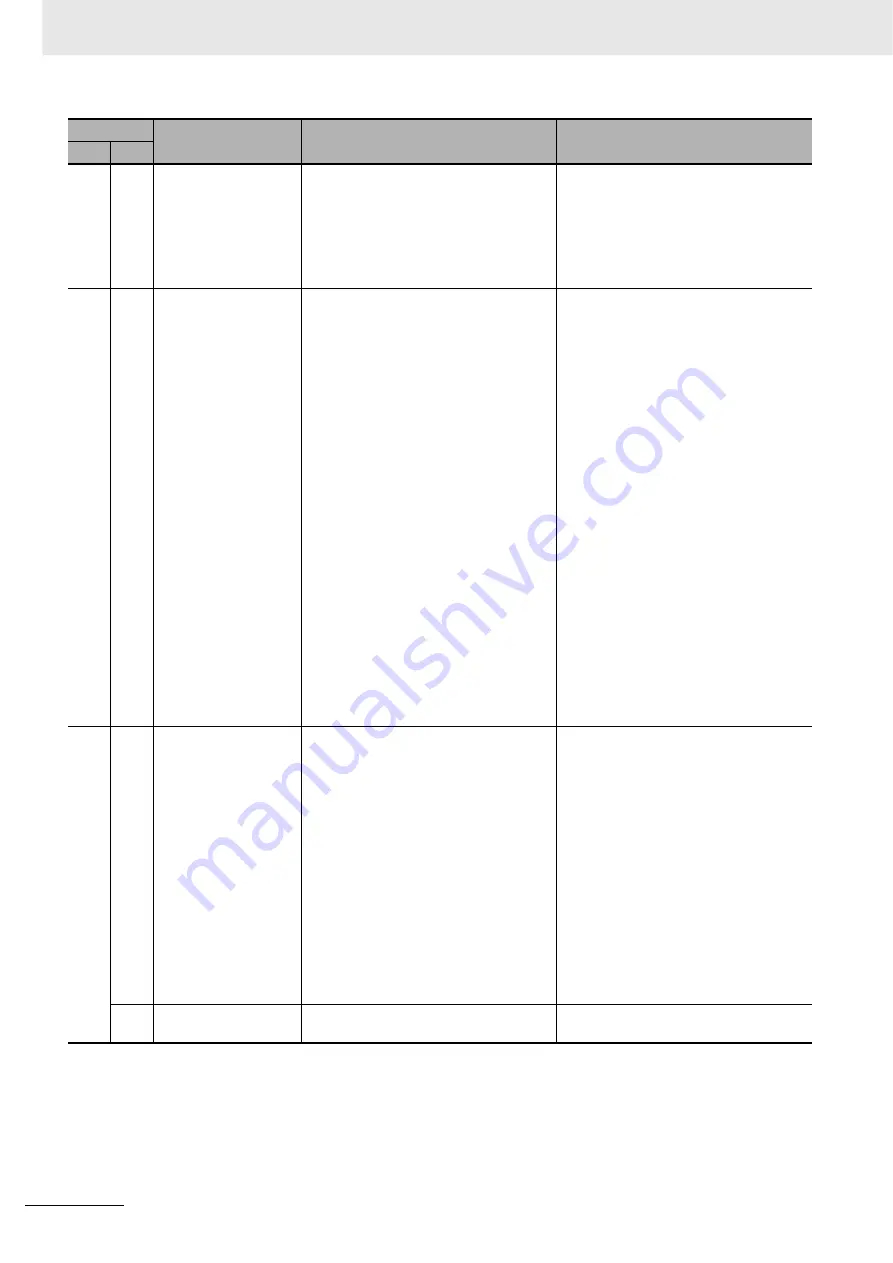
10 Troubleshooting and Maintenance
10 - 12
OMNUC G5-series (Pulse-train Input Type) AC Servomotors and Servo Drives User’s Manual
15
0
Servo Drive Overheat
The temperature of the Servo Drive
radiator or power elements exceeded the
specified value.
• The ambient temperature of the Servo
Drive exceeded the specified value.
• Overload
• Improve the ambient temperature and
the cooling conditions of the Servo
Drive.
• Increase the capacities of the Servo
Drive and the Servomotor. Set longer
acceleration and deceleration times.
Reduce the load.
16
0
Overload
*1
When the feedback value for torque
command exceeds the overload level
specified in Overload Detection Level
Setting (Pn512), overload protection is
performed according to the overload
characteristics.
• The load was heavy, the effective
torque exceeded the rated torque, and
operation continued too long.
• Vibration or hunting occurred due to
faulty gain adjustment. The
Servomotor vibrates or makes unusual
noise. The value set in Inertia Ratio 1
(Pn004) is faulty.
• The Servomotor wiring is incorrect or
broken.
• The machine was hit by an object, or
the machine load suddenly became
heavy. The machine was distorted.
• The electromagnetic brake remains
ON.
• When multiple machines were wired,
the wiring was incorrect and the
Servomotor cable was connected to a
Servomotor for another axis.
Check if torque (current) waveforms
oscillate or excessively swing vertically
with analog output or CX-Drive. Check
the overload warning display and the
load ratio through communications.
• Increase the capacities of the Servo
Drive and the Servomotor.
Set longer acceleration and
deceleration times. Reduce the load.
• Readjust the gain.
• Connect the Servomotor cable as
shown in the wiring diagram. Replace
the cable.
• Remove the distortion from the
machine. Reduce the load.
• Turn OFF the brake.
• Wire the Servomotor and the encoder
correctly so that the wiring matches
the axes.
18
0
Regeneration
Overload
*2
The regenerative energy exceeds the
processing capacity of the Regeneration
Resistor.
• The regenerative energy during
deceleration caused by a large load
inertia increased the converter voltage
across the positive and negative
terminals, and then insufficient energy
absorption by the Regeneration
Resistor further increased the voltage.
• The Servomotor rotation speed is too
high to absorb the regenerative energy
within the specified deceleration time.
• The operating limit of the external
resistor is limited to a 10% duty.
Check the load ratio of the Regeneration
Resistor with CX-Drive. This
Regeneration Resistor cannot be used
for continuous regenerative braking.
• Check the operation pattern (speed
monitor). Check the load ratio of the
Regeneration Resistor and check for
the excessive regeneration warning
display. Increase the capacities of the
Servo Drive and the Servomotor, and
lengthen the deceleration time.
Reduce the Servomotor rotation
speed. Use an External Regeneration
Resistor.
• Set Regeneration Resistor Selection
(Pn016) to 2.
1
Regeneration Tr Error
The Servo Drive regeneration drive Tr is
faulty.
Replace the Servo Drive.
Alarm No.
Name
Cause
Measures
Main
Sub
Summary of Contents for G5 R88D-KE Series
Page 3: ...2 Page 2 53 For 1 000 r min Servomotors 900 W to 3 kW Current Contents Corrected Contents...
Page 504: ......
Page 505: ......