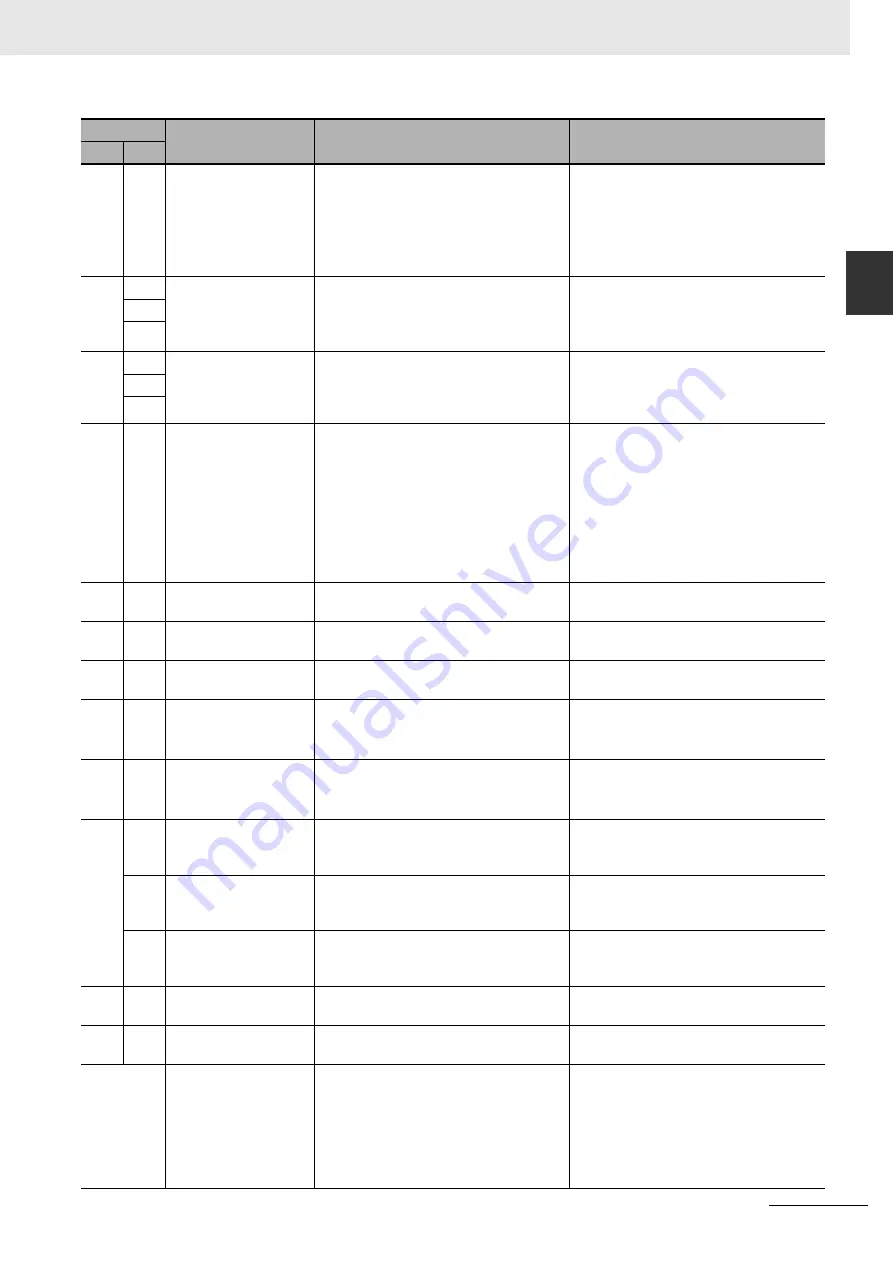
10 - 15
10 Troubleshooting and Maintenance
OMNUC G5-series (Pulse-train Input Type) AC Servomotors and Servo Drives User’s Manual
10-4 T
ro
u
b
lesh
oo
tin
g
10
1
0-4-1
Error Diagnosis with Alar
m Displa
ys
34
0
Overrun Limit Error
The Servomotor exceeded the allowable
operating range set in Overrun Limit
Setting (Pn514) with respect to the
position command input range.
• The gain is not appropriate.
• The value set in Pn514 is too small.
Check the gain (the balance between the
position loop gain and the speed loop
gain) and the inertia ratio.
• Increase the value set in Pn514. Or set
Pn514 to 0 to disable the protective
functions.
36
0
Parameter Error
Data in the Parameter Save Area was
corrupted when the power supply was
turned ON and data was read from the
EEPROM.
• Set all of the parameters again.
• If this error occurs repeatedly, the
Servo Drive may be faulty. In this case,
replace the Servo Drive.
1
2
37
0
Parameter destruction
EEPROM write verification data was
corrupted when the power supply was
turned ON and data was read from the
EEPROM.
The Servo Drive is faulty. Replace the
Servo Drive.
1
2
38
0
Drive Prohibition Input
Error
When Drive Prohibition Input Selection
(Pn504) was set to 0, both the Forward
Drive Prohibition Input (POT) and
Reverse Drive Prohibition Input (NOT)
signals turned ON.
When Pn504 was set to 2, either the
Forward Drive Prohibition Input or
Reverse Drive Prohibition Input signal
turned ON.
Check for any problems with the
switches, wires, and power supplies that
are connected to the Forward Drive
Prohibition Input or Reverse Drive
Prohibition input pin. In particular, check
to see if the external power supply (12 to
24) for sequence input turns ON too
slowly.
43
0
Encoder Initialization
Error
An error was detected during encoder
initialization.
Replace the Servomotor.
44
0
Encoder 1-rotation
Counter Error
An encoder 1-rotation counter error was
detected.
Replace the Servomotor.
45
0
Multi-rotation Counter
Error
An encoder multi-rotation counter error
was detected.
Replace the Servomotor.
48
0
Encoder Phase-Z
Error
A missing phase-Z pulse was detected in
the serial incremental encoder.
The encoder is faulty.
Replace the Servomotor.
49
0
Encoder CS Signal
Error
A logic error was detected in the serial
incremental encoder CS signal.
The encoder is faulty.
Replace the Servomotor.
55
0
Phase-A Connection
Error
An error such as broken wiring was
detected in the external encoder phase-
A connection.
Check the external encoder phase-A
connection.
1
Phase-B Connection
Error
An error such as broken wiring was
detected in the external encoder phase-
B connection.
Check the external encoder phase-B
connection.
2
Phase-Z Connection
Error
An error such as broken wiring was
detected in the external encoder phase-
Z connection.
Check the external encoder phase-Z
connection.
87
0
Emergency Stop Input
Error
The Emergency Stop (STOP) signal was
input.
Check the Emergency Stop (STOP)
signal wiring.
95
0-4
Motor Non-conformity
The Servomotor does not match the
Servo Drive.
Replace the Servomotor with one that
matches the Servo Drive.
Other
numbers
Other errors
The control circuit malfunctioned due to
excess noise or some other problem.
The self-diagnosis function of the Servo
Drive was activated, and an error
occurred in the Servo Drive.
• Turn OFF the power once, and turn it
ON again.
• If the error is displayed even after the
power is turned ON again, the system
may be faulty. Stop using the system,
and replace the motor and/or the
Servo Drive.
Alarm No.
Name
Cause
Measures
Main
Sub
Summary of Contents for G5 R88D-KE Series
Page 3: ...2 Page 2 53 For 1 000 r min Servomotors 900 W to 3 kW Current Contents Corrected Contents...
Page 504: ......
Page 505: ......