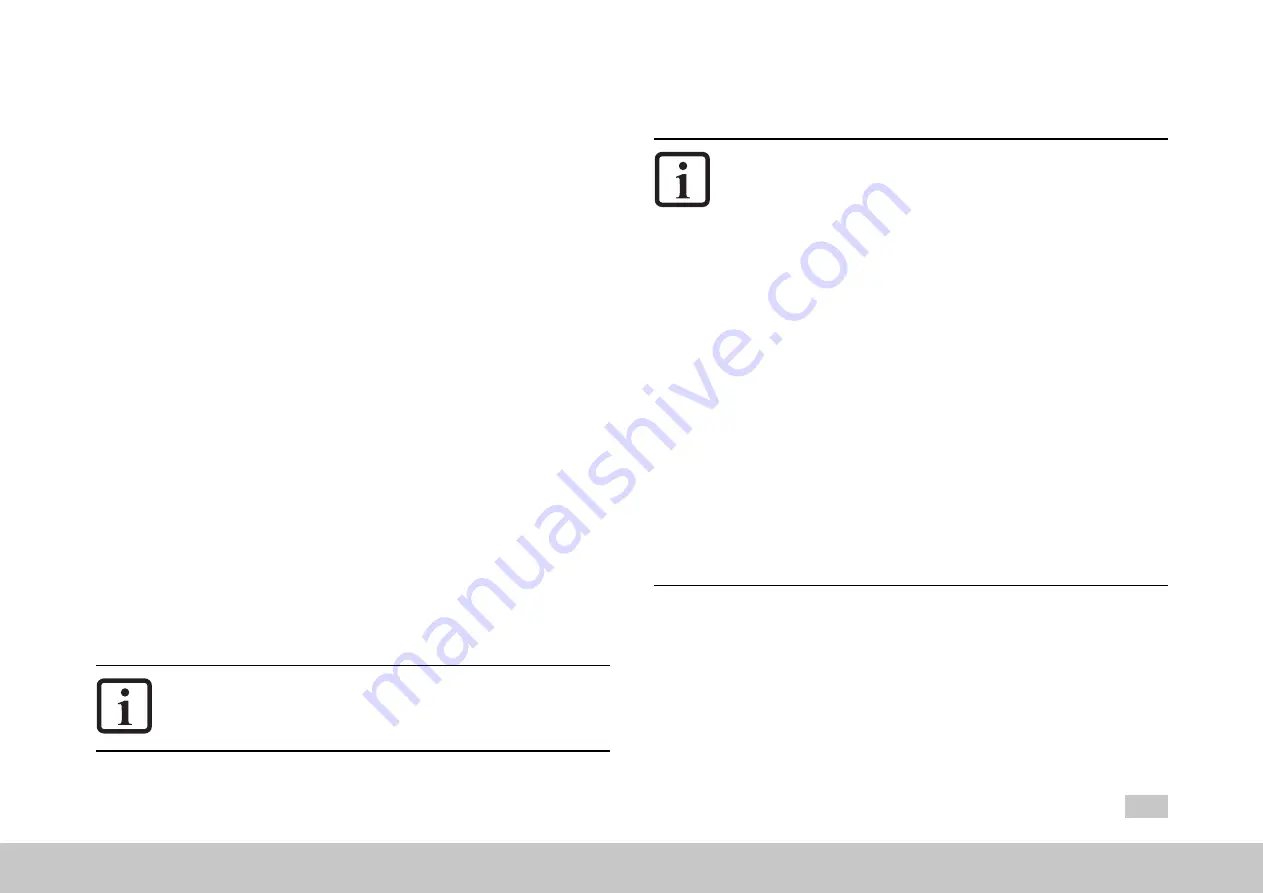
6.3 Encoder offset
“Encoder offset” refers to the commutation offset. This offset is the angular offset
between the motor’s electromechanical layout (U phase orientation) and the zero
position of the commutation encoder (depends on the encoder’s position and
alignment on the motor shaft) in “electrical degrees”. If the encoder’s zero position is
aligned with the direction of the motor’s U phase, the commutation offset is 0
degrees.
The “Encoder selection” screen (see Section "Encoder selection" on page 53) will
show the currently set commutation offset as the “encoder offset” based on the
encoder used for the “commutation and torque control" (MCON) control level.
To determine the offset value again, click on the “Detect” button. In order for this
function to work correctly, the selected encoder for “commutation and torque control”
must be the motor encoder (commutation encoder).
The process takes about 10 seconds. Then the current value of the offset is entered
in the P 349[0] - CON_FM_MConOffset and the original parameter setting is
restored. In order to store the commutation offset in the device in a non-volatile
manner, the device setting must be stored in non-volatile memory.
It is not necessary to determine the commutation offset for standard Moog motors, as
the encoders are aligned. In the case of third-party motors that are not aligned, the
commutation offset needs to be determined with the help of a wizard. For the
definition the motor is run in "Current control" mode (at rated current). For a correct
definition it is necessary for the motor to be able to align itself freely.
A connected brake is automatically vented, provided it is connected to the brake
output and the output has been configured for use of a brake.
NOTE
l
The current used to determine the encoder offset (commutation
offset) is specified by
P 457[0] - MOT_CNom
. This value should
be reduced if the acceleration has too much jerk.
MOOG
ID No.: CB40859-001 Date: 11/2020
MSD Servo Drive - Device Help
55
6 Encoder
6.4 Connections and pin assignations
NOTE
l
This section only lists the most important connectors and pinouts
so as to make commissioning easier.
l
For a full description of the encoder connectors (designation,
position, pinout, function) for correctly installing the devices, see
the “Encoder connection” chapter in the
l
Operation Manual MSD Servo Drive Single-Axis System
(ID No.: CA65642-001),
l
Operation Manual MSD Servo Drive Multi-Axis System (ID
No.: CA97554-001),
l
Operation Manual MSD Single-Axis Servo Drive Compact
(ID No.: CA97555-001),
l
And the MSD Servo Drive Specification on functional
safety in the case of Servo Drives with an “integrated
safety control” design (ID No.: CB38398-001).
l
Please note that the pinouts for evaluating the zero pulse for the
MSD Servo Drive and MSD Single-Axis Servo Drive Compact are
different from each other.
l
If your Servo Drive comes with a technology option with an
encoder function (X8 connector), see the corresponding
Specification for a description of the encoder connections (see
Section "Applicable documentation" on page 12).