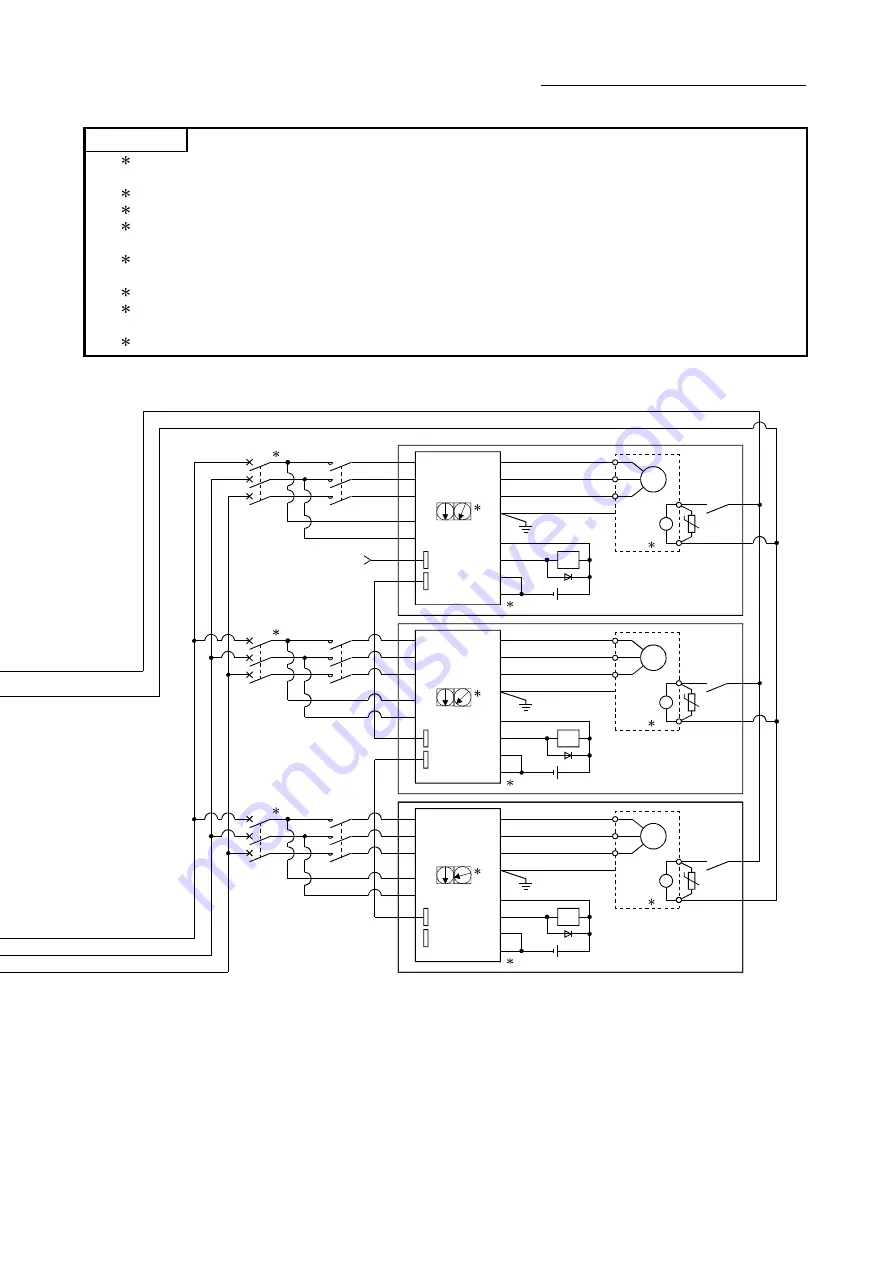
3 - 31
Chapter 3 Specifications and Functions
POINT
(1) 1: Configure up the power supply circuit which switch off the electromagnetic contactor (MC) after detection alarm occurrence on
the PLC CPU.
(2) 2: It is also possible to use a full wave rectified power supply as the power supply for the electromagnetic brake.
(3) 3: It is also possible to use forced stop signal of the servo amplifier.
(4) 4: When MR-J4-GF is used, to set the axis number of servo amplifier, set it using the axis select rotary switch of servo
amplifier. Refer to the servo amplifier instruction manual for details.
(5) 5: The status of forced stop input signal can be confirmed with "[Md.50] Forced stop input". Be sure that the forced stop 24VDC
power supply is not used with the electromagnetic brake of the motor or the electromagnetic valve power supply.
(6) 6: Refer to the servo amplifier instruction manual for selection of the circuit breaker and electromagnetic contactor.
(7) 7: The surge suppressor is recommended to be used for an AC relay or electromagnetic contactor (MC) near the servo amplifier.
Refer to the servo amplifier instruction manual for selection of the surge suppressor for wiring.
(8) 8: Wire the electromagnetic brake power supply and the control power supply using a separate power supply.
(Note-1): Be sure to shut off the both of main circuit power supply L1/L2/L3 and control power supply L11/L21 after disconnection of
CC-Link IE Field Network communication at the time of exchange of servo amplifier. At this time, it is not possible to communicate
between the servo amplifier and Simple Motion module. Therefore, be sure to exchange the servo amplifier after stopping the
operating of machine beforehand.
(Note-2): If the emergency stop signal of Simple Motion module turns OFF when setting of "[Pr.82] Forced stop valid/invalid selection" to "0:
Valid", servomotor is stopped with dynamic brake. (The LED display of servo amplifier indicates "E7.1" (Controller forced stop
input warning).)
CC-Link IE Field Network
L1
L2
L3
U
W
V
L11
L21
CN1A
CN1B
DICOM
ALM
EM2/1
DOCOM
MR-J4-GF
24VDC
U
V
W
Ground
Electro-
magnetic
brake
L1
L2
L3
U
W
V
L11
L21
CN1A
CN1B
DICOM
ALM
EM2/1
DOCOM
MR-J4-GF
24VDC
U
V
W
Ground
Electro-
magnetic
brake
L1
L2
L3
U
W
V
L11
L21
CN1A
CN1B
DICOM
ALM
EM2/1
DOCOM
MR-J4-GF
24VDC
U
V
W
Ground
Electro-
magnetic
brake
MC3
3
4
2
3
2
3
2
6
MCCB4
MC2
6
MCCB3
MC1
6
MCCB2
RA2
RA3
RA4
M
B
RA2
U
M
B
RA3
U
M
B
RA4
U
4
4
0
1
0
2
0
3
Summary of Contents for MELSEC Q Series
Page 2: ......
Page 30: ...A 28 MEMO ...
Page 32: ...MEMO ...
Page 97: ...3 29 Chapter 3 Specifications and Functions MEMO ...
Page 102: ...3 34 Chapter 3 Specifications and Functions MEMO ...
Page 282: ...5 162 Chapter 5 Data Used for Positioning Control MEMO ...
Page 374: ...7 16 Chapter 7 Memory Configuration and Data Process MEMO ...
Page 376: ...MEMO ...
Page 400: ...8 24 Chapter 8 HPR Control MEMO ...
Page 425: ...9 25 Chapter 9 Major Positioning Control MEMO ...
Page 528: ...9 128 Chapter 9 Major Positioning Control MEMO ...
Page 554: ...10 26 Chapter 10 High Level Positioning Control MEMO ...
Page 586: ...11 32 Chapter 11 Manual Control MEMO ...
Page 800: ...16 54 Chapter 16 Troubleshooting MEMO ...
Page 830: ...Appendix 30 Appendices MEMO ...
Page 833: ......