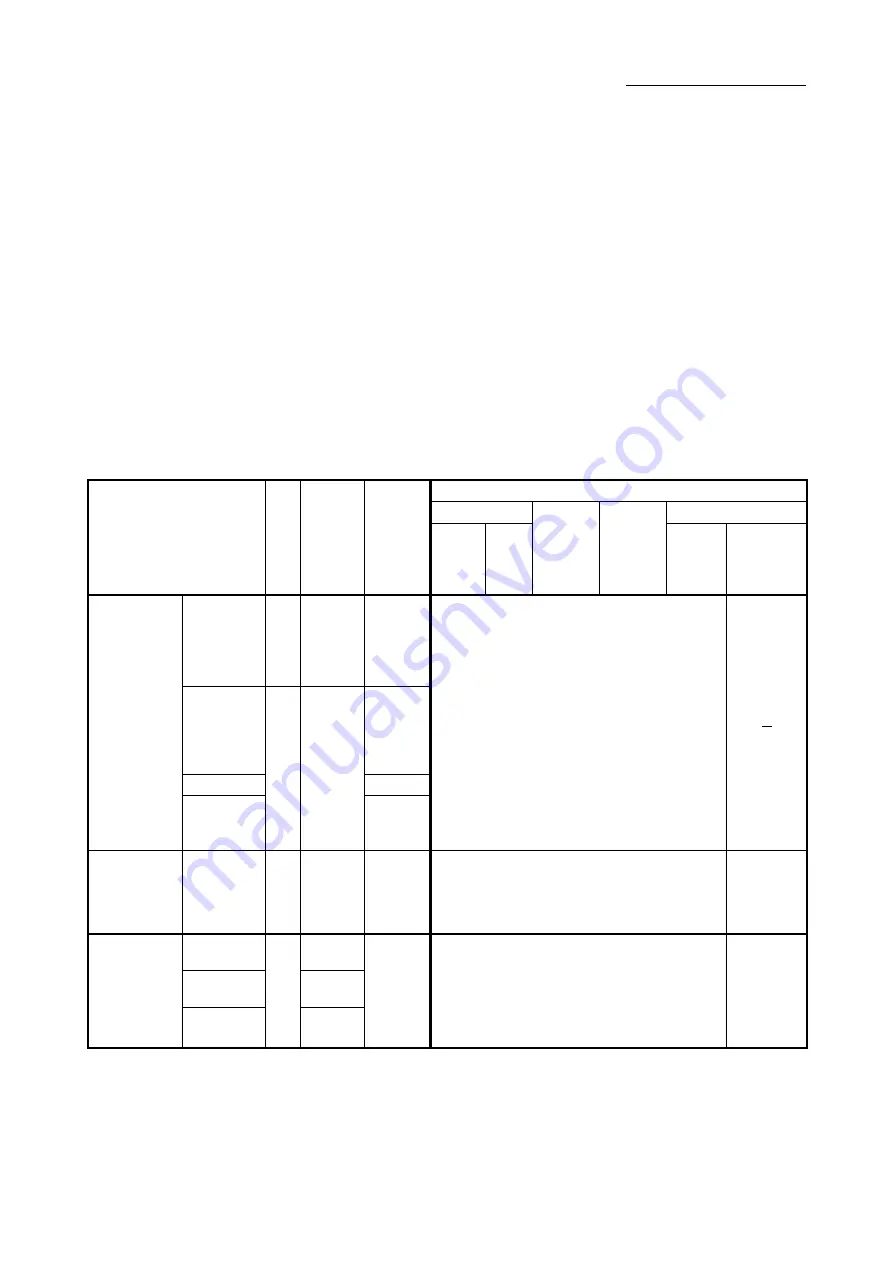
1 - 26
Chapter 1 Product Outline
1.2.3 Outline of stopping
Each control is stopped in the following cases.
(1) When each control is completed normally.
(2) When the servo READY signal is turned OFF.
(3) When a PLC CPU error occurs.
(4) When the PLC READY signal is turned OFF.
(5) When an error occurs in the Simple Motion module.
(6) When control is intentionally stopped
(Stop signal from PLC CPU turned ON, "Stop signal" of external input signal
turned ON, etc.).
The outline for the stop process in above cases is shown below. (Excluding "(1) When
each control is completed normally" above.)
Refer to Section 12.1 "Speed-torque control" for the stop process during the speed
control mode and torque control mode.
Stop cause
Stop
axis
M code
ON signal
after stop
Axis
operation
status
after
stopping
([Md.26])
Stop process
HPR control
Major
positioning
control
High-level
positioning
control
Manual control
Machine
HPR
control
(Note-3)
Fast
HPR
control
JOG/
Inching
operation
Manual
pulse
generator
operation
Forced stop
Forced stop
input to
Simple
Motion
module
All
axes
No
change
Servo
OFF
Immediate stop
For the stop method of the servo amplifier, refer
to each servo amplifier instruction manual.
Servo
READY OFF
• Servo
amplifier
power supply
OFF
Each
axis
No
change
Servo
amplifier
has not been
connected
• Servo alarm
Error
• Forced stop
input to servo
amplifier
Servo
OFF
Fatal stop
(Stop group 1)
Hardware
stroke limit
upper/lower
limit error
occurrence
Each
axis
No
change
Error
Deceleration stop/rapid stop
(Select with "[Pr.37] Stop group 1 rapid stop
selection".)
Deceleration
stop
Emergency
stop
(Stop group 2)
Error occurs
in PLC CPU
All
axes
No
change
Error
Deceleration stop/rapid stop
(Select with "[Pr.38] Stop group 2 rapid stop
selection".)
Deceleration
stop
PLC READY
signal OFF
Turns
OFF
Error in test
mode
(Note-2)
No
change
Summary of Contents for MELSEC Q Series
Page 2: ......
Page 30: ...A 28 MEMO ...
Page 32: ...MEMO ...
Page 97: ...3 29 Chapter 3 Specifications and Functions MEMO ...
Page 102: ...3 34 Chapter 3 Specifications and Functions MEMO ...
Page 282: ...5 162 Chapter 5 Data Used for Positioning Control MEMO ...
Page 374: ...7 16 Chapter 7 Memory Configuration and Data Process MEMO ...
Page 376: ...MEMO ...
Page 400: ...8 24 Chapter 8 HPR Control MEMO ...
Page 425: ...9 25 Chapter 9 Major Positioning Control MEMO ...
Page 528: ...9 128 Chapter 9 Major Positioning Control MEMO ...
Page 554: ...10 26 Chapter 10 High Level Positioning Control MEMO ...
Page 586: ...11 32 Chapter 11 Manual Control MEMO ...
Page 800: ...16 54 Chapter 16 Troubleshooting MEMO ...
Page 830: ...Appendix 30 Appendices MEMO ...
Page 833: ......