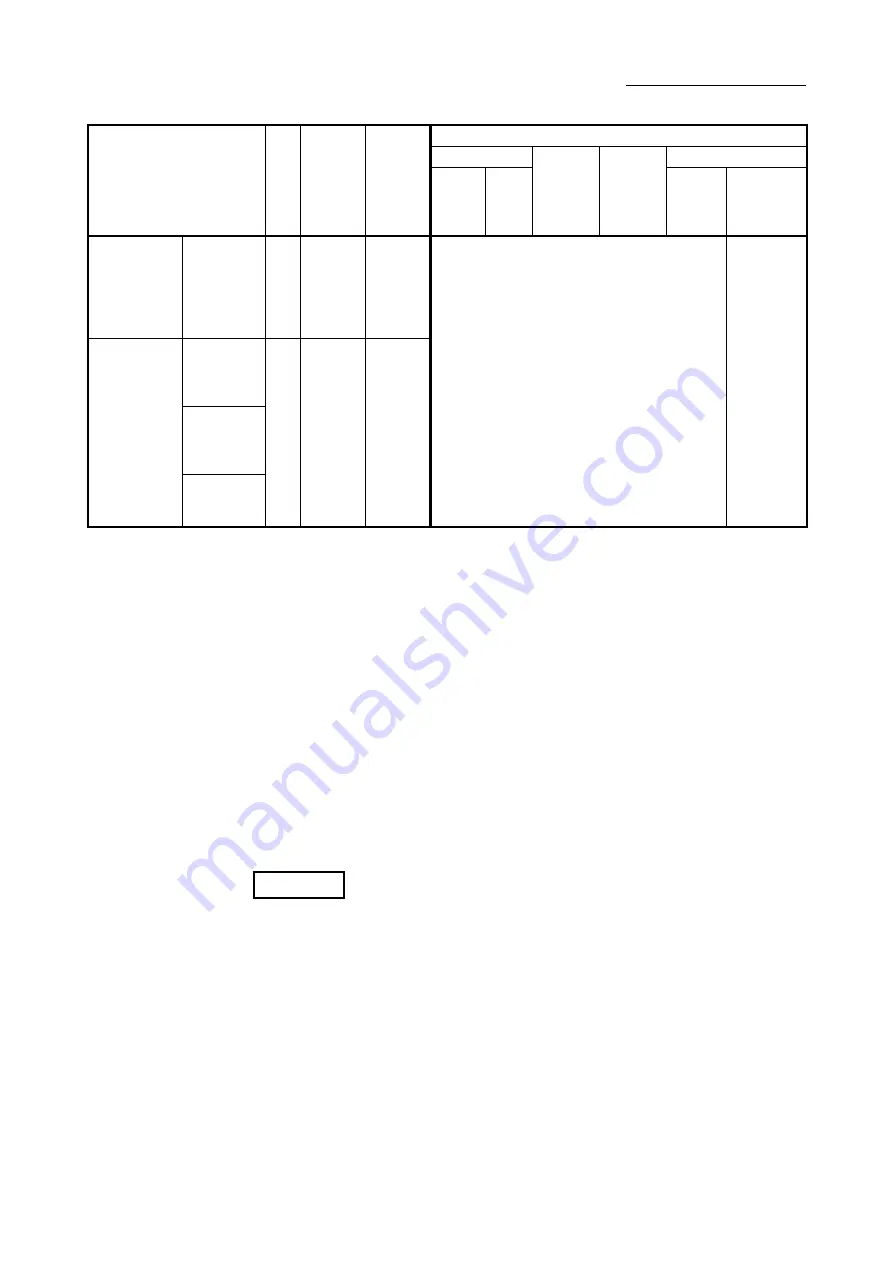
1 - 27
Chapter 1 Product Outline
Stop cause
Stop
axis
M code
ON signal
after stop
Axis
operation
status
after
stopping
([Md.26])
Stop process
HPR control
Major
positioning
control
High-level
positioning
control
Manual control
Machine
HPR
control
Fast
HPR
control
JOG/
Inching
operation
Manual
pulse
generator
operation
Relatively safe
stop
(Stop group 3)
Axis error
detection
(Error other
than stop
group 1 or 2)
(Note-1)
Each
axis
No
change
Error
Deceleration stop/rapid stop
(Select with "[Pr.39] Stop group 3 rapid stop
selection".)
Deceleration
stop
Intentional stop
(Stop group 3)
"Axis stop
signal" ON
from PLC
CPU
Each
axis
No
change
Stopped
(Standby)
"Stop signal"
of external
input signal
ON
"Stop" input
from
GX Works2
(Note-1): If an error occurs in a positioning data due to an invalid setting value, when the continuous positioning control uses multiple
positioning data successively, it automatically decelerates at the previous positioning data. It does not stop rapidly even the setting
value is rapid stop in stop group 3. If any of the following error occurs, the operation is performed up to the positioning data
immediately before the positioning data where an error occurred, and then stops immediately.
• No command speed (Error code 503)
• Outside linear movement amount range (Error code 504)
• Large arc error deviation (Error code 506)
• Software stroke limit + (Error code 507)
• Software stroke limit - (Error code 508)
• Sub point setting error (Error code 525)
• End point setting error (Error code 526)
• Center point setting error (Error code 527)
• Outside radius range (Error code 544)
• Illegal setting of ABS direction in unit of degree (Error code 546)
(Note-2): The failure during the test mode occurs in the following case.
• When the communication cannot be executed between the personal computer and the PLC CPU
(Note-3): The stop process when using the driver HPR method follows the specification of the servo amplifier. [CiA402 mode]
REMARK
Provide the emergency stop circuits outside the servo system to prevent cases
where danger may result from abnormal operation of the overall system in the event
of an external power supply fault or servo system failure.
Summary of Contents for MELSEC Q Series
Page 2: ......
Page 30: ...A 28 MEMO ...
Page 32: ...MEMO ...
Page 97: ...3 29 Chapter 3 Specifications and Functions MEMO ...
Page 102: ...3 34 Chapter 3 Specifications and Functions MEMO ...
Page 282: ...5 162 Chapter 5 Data Used for Positioning Control MEMO ...
Page 374: ...7 16 Chapter 7 Memory Configuration and Data Process MEMO ...
Page 376: ...MEMO ...
Page 400: ...8 24 Chapter 8 HPR Control MEMO ...
Page 425: ...9 25 Chapter 9 Major Positioning Control MEMO ...
Page 528: ...9 128 Chapter 9 Major Positioning Control MEMO ...
Page 554: ...10 26 Chapter 10 High Level Positioning Control MEMO ...
Page 586: ...11 32 Chapter 11 Manual Control MEMO ...
Page 800: ...16 54 Chapter 16 Troubleshooting MEMO ...
Page 830: ...Appendix 30 Appendices MEMO ...
Page 833: ......